Connected technologies are on the rise throughout the manufacturing and distribution value chain. Industry 4.0, as this digital and physical integration has been dubbed, seems to be reshaping how products are designed, produced, distributed and everything in between.
This is bringing a number of benefits to companies that are widely touted, including smarter production processes and more insight into customers, thus more relevant products and services.
But one benefit that may be less understood and pursued is the ability of Industry 4.0 to transform the warehousing and distribution function into a more strategic asset. Warehousing is likely not the first thing that comes to mind when one thinks of strategy. Yet Industry 4.0 could transform distribution centers (DCs) into strategic facilities that are viewed by management as a source of competitive edge.
The evolution of automation
While the more ingenious use of space and its positive impact on productivity are nothing new, automation in DCs has historically been limited. Typically, only centers that deal in standardized product shapes and types have been able to take on automation. And those that do typically keep their robotic systems separated from workers for safety concerns, thus limiting their capabilities and utility.
But expectations for DCs are changing. They are now often expected to perform as “throughput centers,” accommodating shorter, faster supply chains and moving products quickly. An example is the e-commerce fulfillment centers, which deal with fast enough throughputs to justify automation but also house diverse products and must endure seasonal demand. Industry 4.0 enables DCs to evolve to meet these demands while simultaneously improving productivity and reducing risk.
From automated to “smart”
As Industry 4.0 technologies advance, automation is able to combine with other robotic technologies for the most efficient, intelligent systems – ones that are able to work safely and seamlessly alongside humans. Here are five relatively new capabilities that supply chain executives can consider in transforming their DCs into a smarter environment.
• Adaptive robots and connected automated guided vehicles: As shopping habits, the demands placed on DCs and the types and numbers of objects in facilities expand, the call for innovative, unique solutions grows. While the typical method of transporting goods around the warehouse was automated guided vehicles (AGVs), aided by markers or other navigation guides, advanced technologies can enhance this by creating a digital record to guide robots in their surroundings.
• Semiautonomous machines add value: The automation of outbound packaging, shipping and gift-wrapping is the focus of several companies, for unit picking. To this end, sensor detection technology using automatic format adjustment has been designed to handle packaging. By picking up changes in product qualities via sensors, the control system would be automatically notified to reset and ensure selection and use of the correct packing box. The process cuts down on the amount of time it takes to switch up configuration and readjustment, and should automatically reject products if they are classified incorrectly. By doing this without stopping the system in the event of an error, productivity improves. Data is also picked up by the system, which sets up predictive maintenance capabilities going forward.
• Next-gen distribution operations: As omnichannel capabilities become a growing area of focus, DCs are under ever growing expectation to churn through a large volume of orders. These pressures likely necessitate new, modular technologies that can efficiently maneuver real-time automation systems and ever more sophisticated transactions.
By closely tracking the assets of automation and arranging them in a new way, warehouse execution systems (WES) can continually hone performance and make the most of labor resources. Their capabilities run the gamut from processing initial orders, all the way to routing and directing automated equipment. Waveless (pull-based) processing, which processes order requirements from hosts and should then delegate work to the best machine and labor resources, aids the process further by adjusting physical movement.
• Smart, automated facility management: Within the management of DC facilities, Industry 4.0 technologies are finding new uses. Environmental features such as humidity or HVAC, for example, are among the systems that can be controlled remotely for optimal energy efficiency. IoT applications can also make use of these sensors to accumulate additional data about the conditions inside these facilities. Properly gathered and analyzed, this information can be used to strategically and proactively manage buildings for continually improved efficiency.
• Safety enhancements and modularity: One of the most important features of robot actuation and sensors is safety enhancement. This can be achieved by giving highly automated technologies the means to operate effectively in an environment where humans and robots work together. By optimizing the use of sensors to pick up when human workers enter or approach their area, robots can instantly adjust their activity to ensure safety.
Integrating the digital and the physical in the warehouse
Industry 4.0 capabilities can not only be considered in the context of improving the physical nature of the DC, but also in light of how they could help streamline the work processes that depend on the DC. Here are three examples:
• Supply chain information sharing: Thanks to Industry 4.0, DCs can better plan for demand and how the supply chain responds to it. Partially enabled by the improved traceability of products and interconnected technologies, Industry 4.0 technologies can collect the resulting operational data and make it available to every stage of the supply chain.
• Procurement: By comparing all product inventory and controlling for discrepancies, Industry 4.0 can also streamline procurement. In the event of inconsistencies, compliance would be notified and updates automatically fielded to adjust characteristics in management systems as needed.
• Supply planning and resource allocation: Thanks to the cloud-access capabilities of Industry 4.0 technologies, real-time data sharing across the supply chain is also accessible to stakeholders. Data flow should continue to improve as the number of smart devices exchanging information grows, creating opportunities for synchronizing activity and enabling stakeholders to allocate resources in a strategic way, maximizing efficiency.
Implementing Industry 4.0 for the distribution center
Companies that adapt their DCs to changing expectations while harnessing new, Industry 4.0 capabilities have the opportunity to elevate their centers into a more strategic component of the enterprise. It's another example of how any organization today can be a technology company, using new technologies to maximize efficiency, leapfrog competitors and develop new business models and processes.
———
Contact Piyush Sampat at [email protected].
Full report may be found here.
As used in this document, “Deloitte” means Deloitte Consulting LLP, a subsidiary of Deloitte LLP. Please see http://www.deloitte.com/us/about for a detailed description of the legal structure of Deloitte LLP and its subsidiaries. Certain services may not be available to attest clients under the rules and regulations of public accounting.
SC
MR
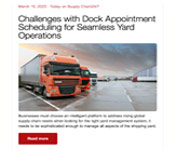
Latest Supply Chain News
Latest Resources

Explore
Latest Supply Chain News
- How to improve demand forecasts for new product families
- Services sector sees growth in October, reports ISM
- Balanced supply chain management Part 4: The key—leading beyond the silo
- Managing inbound freight: What has changed in two decades?
- Inbound freight: Often a missed opportunity
- Aggregators sitting on the throne of Africa’s e-commerce supply chains: What lessons can we learn?
- More latest news
Latest Resources
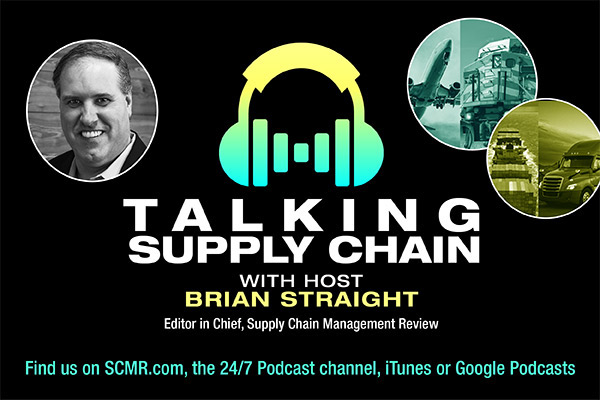
Subscribe
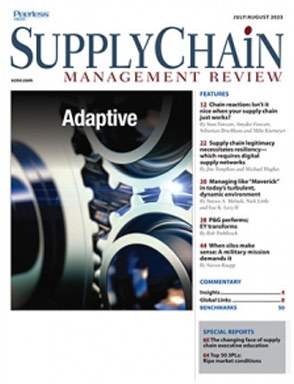
Supply Chain Management Review delivers the best industry content.
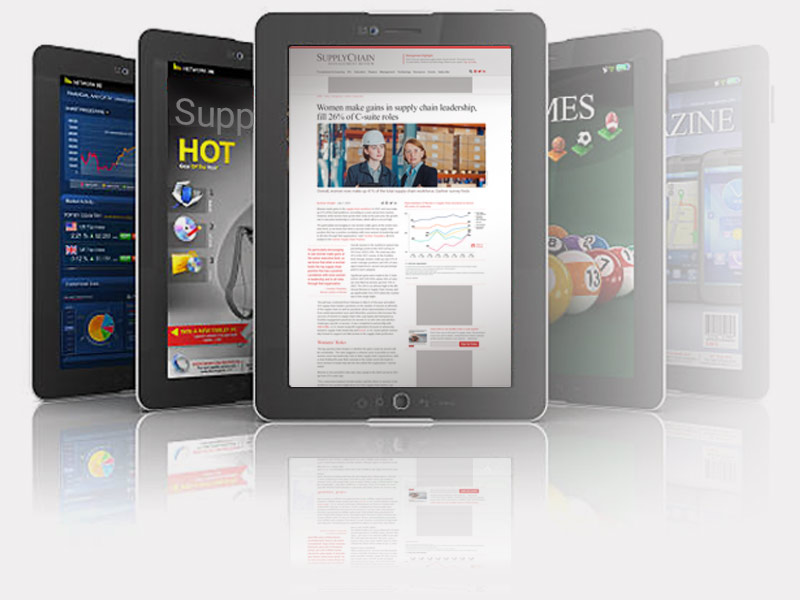
Editors’ Picks



