Editor’s Note: Supply Chain Management Review published Building a total cost framework for 3D Printed Parts, an article by Jeannette Song, William McCall and Ryan Hayford, in the November 2021 issue of the magazine. Based on original research by Song and McCall, with input from Russell E. King and Tali Rosman, the article discussed advancements in 3D printing that have put the technology within reach of more manufacturing organizations. It also includes a total cost framework for assessing which parts may be economical to produce in an additive manufacturing environment. Below, we offer the original research, which includes the mathematics behind the analysis, along with references for practitioners who wish to learn more about the topic.
Abstract
Along with the steady progress of additive manufacturing (AM), more and more companies realize its potential impact on spare parts management. To aid companies in identifying which parts are suitable to transition from traditional manufacturing (TM) to AM, we present a new costing framework for breakeven analysis between AM and TM.
The breakeven point is the annual production quantity where AM and TM have the same unit total cost, below which AM is preferable. Deviating from the existing methods in software packages and academic papers that focus on portions parts’ lifecycles in isolation, our framework accounts for costs across all phases of the parts’ lifecycle and is hence scalable in evaluating a large portfolio of parts a company may have.
We explore in detail a set of changes to the typical inventory total cost function and discuss estimating methods for the function’s parameters for AM and TM. We demonstrate that the breakeven points generated from our model are typically higher than those prescribed by the exiting models, depending on the part’s lifecycle phase. For the end-of-life, all-time-buy parts, we find that dual sourcing from TM and AM leads to significant cost savings over single sourcing from AM or TM.
1.) Introduction
Additive Manufacturing (AM), or 3D printing, initially found success in prototyping as well as in jigs and fixtures by offering a high level of design freedom (“complexity is free”) and short design/build cycles leading to a faster time to market. Recent applications in low volume production have leveraged AM’s ability to make weight optimized geometries and to consolidate separate components (Wagner & Walton, 2016). In a particularly notable example, an aircraft engine consolidated 855 components into just 12 parts. The new design weighed less, used 20% less fuel, and produced 10% more power (Kellner 2017). In these contexts, AM is often the lowest cost solution because of the high upfront tooling costs associated with Traditional Manufacturing (TM).
While AM will continue to grow in these areas, a topic of increasing interest is the production of spare parts via AM (Walter, Holmström, & Yrjölä, 2004). Indeed, major manufacturing companies are now producing end use spare parts (Daimler, 2017; Deutsche Bahn, 2018; Volvo, 2018). These firms often maintain portfolios of spare parts amounting to tens of thousands of stock keeping units (SKU) and worth of tens of millions of dollars (Wagner & Lindemann, 2008). A similar situation occurs for transportation service providers, such as rail and shipping companies (Foundry Management and Technology 2019).
This partly explains why the global spare parts market for just metal components was $526 billion in 2019 (Global Market Reports 2020). For many of these businesses, spare parts make up double digit percentages of revenue (Cohen et al., 2006, Wagner, Jönke, & Eisingerich, 2012), thus effective spare parts management is crucial in protecting the bottom line (Kennedy, Patterson, & Fredendall, 2002).
Currently, most spare parts are made with TM methods, both subtractive, like CNC, and forming, like casting. These processes usually require high upfront tooling costs, centralized production, and high setup costs when switching to produce a different part. Consequently, sourcing (or producing) spare parts via TM entails batch ordering, transportation, long lead times, and significant warehoused inventory, resulting in high costs associated with maintaining slow moving inventories with uncertain demand.
AM offers a potential solution to this challenge due to its virtue of flexible production with low setup costs between printing different parts (D’Aveni, 2018; Holmström & Gutowski, 2017; Khajavi, Holmström, & Partanen, 2018). It is also more mobile, enabling decentralized, local production. Sourcing from AM implies lower ordering costs and shorter lead times, which translate into lower inventory levels and lower annual inventory related costs, including ordering, holding, and obsolescence costs. AM also has much lower upfront costs compared to TM since it does not need tooling. The tradeoff is that AM usually incurs a higher marginal unit production cost (Khajavi, Deng, Holmström, Puukko, and Partanen 2018).
Despite the potential benefits of AM, however, the current adoption of AM for spare parts is still low (Howleg & Pil 2015). This is not just because of technical limitations of the technology but also the lack of scalable analytical tools for identifying scenarios where AM lowers the overall costs. Indeed, the motivation of our research rests on the observations of the latter.
There are several popular software tools (Protolabs 2021, Varotsis 2018, Xometry 2021) to assess if a part can be printed, but most of them only provide unit production or upfront tooling costs and neglect other cost areas of the product lifecycle, which presents challenges to companies who would like to evaluate the AM potential for a wide range of spare parts in various stages of the lifecycle. Even more importantly, a typical AM vs. TM breakeven analysis identifies an annual order quantity where AM and TM have the same unit total upfront and production cost, ignoring the differences in inventory costs (Xometry 2020).
For spare parts the initial tooling costs are sunk so the breakeven point tends to be zero, meaning that TM is always the lowest cost option. With the inclusion of inventory costs a breakeven point for spare parts is likely to change. The academic literature, on the other hand, presents methods for calculating inventory costs of AM vs TM but do not discuss how to estimate the cost parameters. They also ignore other costs in product lifecycle such as upfront tooling cost. These weaknesses prevent the frameworks from being operationalized in practice.
In order to operationalize AM for spare parts, each SKU requires a detailed assessment of both technical (“can it be printed?”) and economic (“is printing cost effective?”) aspects.
Current best practice is for the technical and economic assessments to be executed independently by experts using specialized tool sets. Separate assessments work well when considering a small number of SKUs but scaling to cover entire portfolios would be very effort intensive. For businesses to scale their use of AM for spare parts the assessments must be automated.
In this paper we present a total cost framework that considers the unique supply chain impacts of AM and can be operationalized for all parts of the product lifecycle. We accomplish this in three steps. In the first step, we detail a unified total cost function tailored for parts.
We assume the part production/inventory is controlled by an (r,q) policy, where r is the reorder point and q is the order quantity. In the second step, we provide methods for estimating each of the inputs of the total cost function. Finally, we illustrate the framework through three example scenarios from different phases of the product life: 1) the initial phase, where the part is used in low volume series production of the original equipment, 2) the spare part phase, where the equipment is not produced but the part still is for aftersales spares , 3) the final phase, where the TM production of the end-of-life part where is stopping and an all-time-buy is required but AM continues to be a sourcing option. We compare the results of the breakeven analysis modeled with and without the addition of inventory costs.
For initial, low volume production (scenario 1) we found that the inclusion of inventory costs in the comparison increases the AM vs TM breakeven point. We also found in the normal, spare part scenario that including the inventory costs produced a breakeven point where previous there was none (TM was always less costly). In the final, all-time-buy scenario, we found that dual sourcing from TM and AM was significantly less costly than single sourcing from AM or TM. In each scenario, we demonstrate that the breakeven point for AM vs TM is higher with the inventory costs considered.
2. Related Literature
Various scholars from the academic community have paid attention to the impact of AM on spare parts inventory management and the supply chain in general. See, for example, Holmström, Partanen, Tuomi, & Walter 2010, Khajavi, Holmström, & Partanen 2018, Knofius, van der Heijden, Zijm 2018, Lindemann, Reiher, Jahnke, & Koch 2015, Westerweel, Basten, & van Houtum 2018, Zhang, Westerweel, Basten, & Song (2020) and the references therein.
Within the literature, Heinen and Hoberg (2019) appears to be the most relevant to our work. These authors analyze a set of 67,219 spare parts with actual part level data for TM production cost, TM lead time, minimum order quantity, and demand. They assume an (r,q) policy is used under TM and an (s,s-1) base-stock policy is used under AM, and compute the optimal policy parameters. Using conservative values of TM order costs (10% of TM production cost) and AM production premium (+300%) they found that 2% of total units and 8% of SKUs were candidates for AM. Different from their model, our framework considers a more general (r,q) policy for AM, which includes their (s,s-1) base-stock policy as a special case. We also include the upfront tooling cost for parts in the early stage of the product lifecycle and part obsolescence cost for parts in the late stage of the lifecycle. In addition, we allow dual sourcing from both TM and AM.
Knofius et al. (2016) present a top down analysis that ranked a set of 40,330 spare parts based on a weighted score to find the best fit parts for AM. The analysis considers demand rate, lead time, response time, remaining usage period, manufacturing and ordering costs, safety stock costs, number of supply options, and supply risk. The authors found that only 2.8% of the parts were both technical and economically feasible for AM. Different from their weighted score model, we consider the relative AM and TM costs for each SKU.
Song and Zhang (2020) present a model to help a company decide which parts to print-on-demand using an in-house 3D printer and which parts to stock by using (r,q) policies and sourcing from TM. Because the 3D printer has a finite capacity, assigning more parts to the on-demand mode would increase the congestion at the printer and hence lengthening the delivery time of the parts. In other words, the AM option entails an endogenous stochastic lead time.
The authors developed an algorithm compute the near optimal policy. In a numerical experiment with 1,152 cases in a synthetic data set varying the procurement cost, AM procurement premium, holding cost rate, back order costs, demand rate, demand rate, demand composition, and printer speed, they numerically identify set of parts for print-on-demand and the optimal (r,q) inventory policy for the rest of the parts.
They found average cost savings of 5% over the sole TM sourcing option. Different from their model setting, our framework assumes a constant lead time for the AM option, which is applicable when the AM supplier has sufficient capacity and can quote a constant lead time, and is consistent with other works reviewed here. See Zhang, Westerweel, Basten, & Song (2020) for more discussions on this issue. While Song and Zhang focus on the mature stage of parts’ lifecycle and on-demand printing with AM, our work allows the full spectrum of the life and assumes make-to-stock with AM using (r,q) policies. This is also consistent with Zhang et al. (2020).
Sirichakwal and Conner (2016) They assume a (s,s-1) inventory policy for AM instead of the more general (r,q) policy which they use for TM. They also assume there is an expediting supply source to cover any stockout. For each setting they present a cost function, based on which theyconduct a series of numerical sensitivity experiments varying lead time, holding cost, and demand rate. For each scenario they find the optimal inventory plociy for AM and TM and then determine the lowest cost source. They found that the shorter lead times of AM lead to reductions in inventory carrying costs.
They also identified that the low demand levels create very non-linear costs curves for holding costs and stock out risk as the target stock level changes. They then utilize their cost function and inventory policy optimization methods to reassess a breakeven analysis case study presented by Atzeni & Salmi (2012) by adding inventory costs. The original case study calculated the breakeven point as N=42 units using only upfront tooling and unit production costs; inventory costs were not considered.
The authors calculated the inventory costs for AM and TM with several different values for AM lead-time, and showed that for all AM had less inventory costs than TM at the breakeven point under. This indicated that the true breakeven point was greater than N=42 units; however, the new breakeven point was not calculated. Our total cost framework further builds on this with refinement to the inventory costing so that we are able to estimate the true breakeven point; not just say that it is higher. Additionally, our framework uses simpler inventory policy optimization methods that eliminate the saw tooth pattern in their cost curves; thus preventing multiple intersections of the AM and TM cost curves.
Feldmann, C. & Pumpe, A. (2017) break down the SCOR model into different cost drivers and identifies which are most affected by switching to AM. The authors identified 16 cost areas expected to have major impacts due to the change to AM: Source - inbound expedited freight, capital charges, scrap disposal, out of stock costs, depreciation, tooling costs; Make - labor costs, tooling, depreciations, disposal, direct material; Deliver - outbound expedited freight, customs duties and trade barriers, capital charges finished goods, infrastructure, scrap disposal. In our cost model, each of these are captured in either the upfront, production, or inventory costs.
The total cost framework
We now present our total cost framework, which is developed based on our in-depth analysis and understanding of industrial data and consultation with practitioners.
3.1 Inventory system and policy
We consider a company that manages multiple independent parts with no correlated demand parts using an inventory system. Following the standard, well justified assumption in the literature, we assume the demand process for each part follows a Poisson process. The lead times for reordered parts from both TM and AM are considered as fixed. Unsatisfied demand is backlogged. For each part, the company would like to maintain a predetermined service level, i.e., the in-stock rate. Under this setting, it is known that the optimal inventory policy that minimizes the long-run average inventory ordering holding is an (r,q) policy, and there is an iterative algorithm that can compute the exact optimal policy parameters; see Zipkin (2000). For this reason, we use an (r,q) inventory policy for both AM and TM, although the policy parameters differ. Thus, the analysis for each part is the same, only parameters for that analysis vary.
For ease of implementation and scalability, instead of using the exact optimization algorithm, we use simple and closed-form formulas to approximate the optimal policy parameter. In particular, we approximate the lead time demand, which has a Poisson distribution, by a Normal distribution. We set the reorder quantity by the EOQ (or MOQ) formula, and we set the reorder point to be the base-stock level with a pre-specified service level. These approximations are commonly adopted which guarantees good performance. See Zhang, Westerweel, Basten, & Song (2020) for more detailed discussions and references; these authors adopt the same approximations as ours. These formulas are intuitive and are taught in master level (such as MBA) courses that cover inventory models, they can also be straightforwardly coded in a spreadsheet, therefore easy to operationalize and customize. The computation is simple and fast, and hence scalable.
3.2 Total cost function
The normal cost function for an economic order quantity model is:
Annual Cost = Purchase Cost + Order Cost + Holding Costs
(see Zipkin 2000), i.e.,
T_a=CD_a+K D_a/Q+hI_avg (1)
where
.
This cost function works well to estimate annual costs for SKUs in series production, but for spare parts the overall lifecycle costs must be considered. Adapting the total cost function to cover the full lifecycle for spare parts requires several changes as described below.
Convert from annual cost to lifecycle cost by multiplying the annual cost function by the expected years of demand,
Addition of upfront costs, i.e., all of the costs incurred to make a SKU ready for production. Transitioning from TM to AM is likely to incur some switching costs in the form of redesign and verification. Upfront costs also include any tooling that would be needed for AM or TM,
More precise average inventory on hand. When annual demand is large, the average inventory on hand is dominated by the order quantity. But at low demand levels, the reorder point and expected demand in lead time become critical considerations,
Addition of recurring costs. During series production, recurring costs like tool storage and maintenance are relatively small, but for spare parts they can become significant cost factors,
Modification of obsolesce costs. Obsolesce is normally part of the unit holding costs. However, this neglects to consider how obsolesce as an annual percentage can vary with total demand. Intuitively, as the ratio of average inventory on hand to total future demand increases, the obsolesces costs should also increase. Simply put, the more stock kept on hand the more units that need to be scraped when demand ends. This is particularly evident when there are minimum order quantities. The total cost function for spares assumes that an amount equal to the average inventory on hand will be scrapped over the full lifecycle.
Compiling the aforementioned requirements, a new cost function is:
Total Cost = Upfront costs + Years*(Production Cost + Order Cost + Holding Costs + Additional Costs) + Obsolesce Costs
That is, T_lc=U+YD_a C+Y(K D_a/Q+hI_avg+A)+CI_avg (2)
where
All other variables carry over from the original function in Equation (1).
A typical AM vs TM breakeven analysis only considers the first two terms; upfront costs (U) and direct production costs (YDaC). Excluding the inventory costs would yield an incomplete result. Note that the average inventory on hand excludes pipeline inventory. This is because units in transit do not incur warehousing costs. And typically the duration of transportation is less than the payment terms so there is not cost of capital.
3.3 Estimating variables for the Total Cost Function
The same total cost function should be used for both the AM and TM sourcing options, only the inputted variables will differ. Among these variables, only Y and Da are the same for both AM and TM. Estimating some of the variables, like P and U, require expert knowledge or specialized software tools. But the remainder can be broken down into components which can be estimated using information from the business. Specifically:
Variable Estimation:
Upfront Costs
For spare parts, the upfront costs for TM are normally zero, as it is the current part design where the upfront cost has already paid for during the equipment production stage. For AM some amount of redesign and verification may be needed. If there are tooling costs for TM or AM (for example new production or the tooling is not available), then it will need to be estimated as well.
Estimations of tooling costs should consider the specifications of the SKU (geometry, material, tolerances, etc.) as well as the requirements of the process. However, a detailed discussion of unit costs is beyond the scope of this paper as there are several specialized software packages commercially available (Protolabs 2021, Varotsis 2018, Xometry 2021).
Unit Production/Purchase Cost
For TM this cost should be captured from existing data in the company’s ERP system. If the TM cost is not available (example: data is out of data or new production) then it will need to be estimated. The AM unit costs will also need to be estimated unless the SKU has been made with AM before.
Estimations of unit costs should consider the specifications of the SKU (geometry, material, tolerances, etc.) as well as the requirements of the process (equipment amortization, labor, consumables, etc.). However, a detailed discussion of unit costs is beyond the scope of this paper as there are many specialized software packages commercially available (Protolabs 2021, Varotsis 2018, Xometry 2021).
Annual Mean Demand
The annual mean demand is the same for AM and TM. Should be captured from existing enterprise data systems (ERP/PLM)
Years Of Demand
Years of demand is the number of years that the Annual Mean Demand is expected to last. Same for AM and TM. Should be captured from existing enterprise data systems (ERP/PLM)
Fixed Order Costs
The fixed ordering costs are a composite of several underlying factors. Typical categories are administrative (scheduling, communications, etc.), operations if internal (machine set up, etc.) logistics if external (packaging, freight, etc.). These costs are highly variable between businesses and should be estimated in detail for each product family (e.g., polymers, metals)
AM tends to have a lower ordering cost than TM for two reasons. First, while TM can only make one SKU per batch AM can mix them. So, machine set up costs often get added to the production cost instead of ordering costs. Second, TM is more susceptible to stock out costs than AM.
Stockout Costs Included in Ordering Costs
Absent from the total cost function is a distinct calculation of the cost of shortages. Any time a SKU stocks out and demand cannot be met additional costs may be incurred. This could be because demand was higher than expected or the supply chain was disrupted. Examples of additional costs include lost revenue, expedited freight, response team salary, SLA breakage fees, and customer satisfaction.
Other approaches in literature calculate these costs by estimating the average number of units on back order and assigning a cost for each. This approach has two drawbacks.
First, it requires a measurement for the cost of a unit on backorder, this data may not be available (Heinen and Hoberg 2019). Second, the discrete nature of Poisson distribution and the low demand in lead time of spare makes the cost estimation overly sensitive and jumpy.
An alternative approach is recommended where each order of a SKU to a vendor is a risk event and is assigned an additional cost. This additional cost is estimated by first measuring all of the annual costs associated with supply chain disruptions for spare parts, and then dividing this cost by the annual number of orders to vendors for spare parts. The number of orders to vendors should be readily available, and measuring the overall costs is more straightforward than at the SKU level. In the context of supply chain, the primary benefit of AM is its responsiveness. So, when calculating ordering costs for AM the stockout costs should be set to zero.
Annual Unit Holding Cost
For the annual unit holding cost, example factors that should be considered for both AM and TM: cost of capital, insurance, taxes, deterioration, and warehousing. All of these should be readily available from corporate financing. Note that obsolesce is not included in holding cost for this model.
Except warehousing, the above cost components are all normally expressed as a percentage of the unit cost. Warehousing costs more dependent on the amount of storage space needed. ~Annual cost per cubic volume of storage space * required storage volume of one unit. Though the warehousing cost for AM and TM should be the same their unit cost is different and correspondingly their holding costs will be different.
Order Quantity
Once K and h are known the most cost effective order quantity can be estimated using the economic order quantity. Since K and h are different for AM and TM they will have different order quantities. This should be compared any minimum order quantity requirements in place. For TM the actual reorder quantity may be available from the ERP system.
Lead Time
For TM lead time should be captured from existing enterprise data systems (ERP/PLM). If no data is available, then the average value of lead times for spare parts in that product family (metals/polymer/etc.) could be used. A review of online AM service bureaus shows lead times for as short as 1 day for polymer parts and 3 days for metal parts. Conservative estimations for all internal processes would be half a week (3.5 days) for polymer parts and one week (7 days) for metal parts.
Reorder Point
When considering shortage costs the optimal reorder point covers demand equal to the critical ratio. The critical ratio is defined as the cost of a shortage divided by the sum of the shortage cost and the holding costs. Heinen and Hoberg (2019) assumed the holding costs to be 20% of the unit costs. In Table 1 a holding cost of 20% and the shortage cost in the first column are used to calculate a set of critical ratios in column 2. Then for each combination of critical ratio and demand in lead time the optimal reorder point is found using a Poisson distribution.
Table 1 shows that for low demand levels the optimal reorder is insensitive to changes in the shortage cost. In Table 1 there is no demand level where doubling any shortage cost changes the optimal reorder point by more than one. This means that a critical ratio estimated using top level holding and shortage costs is a reasonable proxy for the SKU specific critical ratio. Even if the actual shortage costs for a SKU were half or double the average the impact to the optimal reorder point would be small.
A further simplification is to set the critical ratio based on the business goals. For example, if the business has a goal of 95% delivery readiness then 95% can be used as the service level. Since reorder point is insensitive to the service level any reasonable value (example: 90% to 98%) can be used.
Additional Recurring Costs
Tooling for TM processes incurs recurring costs in several forms, most notable ones are storage and maintenance. If the SKU is outsourced there may be direct payments to the vendor. If the TM process is internal, then costing could come from operations. This should be zero for AM since it is a toolless process.
Effect of Life Cycle Phase
To illustrate the impact of the inventory costs on breakeven analyses a theoretical example part was modeled and explored in three different scenarios, one for each different stage of a product life cycle. We illustrate the framework through three example scenarios from different stages of the product life cycle 1) Series production of the original equipment 2) After sales spares where the equipment is not produced but the part still is 3) End of life where the TM production of the spare is stopping and an all time buy is required but AM continues to be a sourcing option.
The parameters for U and C in Table 2 were estimated using online service bureau costing tools. The remaining parameters were estimated using aggregate data from research partners.
4.1 Initial phase
A breakeven analysis is most commonly used to assess if AM is a cost effective option for SKUs with low demand levels. Typically, these analyses do not consider inventory costs but still show that AM is a cost effective alternative to TM below some quantity. Table 3 shows the breakeven point without inventory costs is 100 units per year and with inventory costs the breakeven increases to 138 per year. The shift from 100 to 138 is driven by disparate inventory costs for AM and TM.
Figure 1 shows how the inventory costs increase the total costs for both AM and TM but the impact is less for AM than TM. At the breakeven point of 138 per year the inventory costs for AM are $0.97, or 6% of the production and upfront. For TM inventory costs are $4.35, or 35% of the production and upfront costs.
4.2 Spare Part Phase
A similar breakeven analysis can be applied to the same component as a spare part. The tooling costs are already paid for and changing to AM has switching costs. Without inventory costs TM is always less costly than the AM costs regardless of the demand level so there is no breakeven point. This is illustrated in the Figure 2 where the TM cost is flat and is never intersected by the AM cost curve.
If the inventory costs are factored in the result is significantly different with a breakeven point at 15 units per year. Here the inventory costs are more than four times as much as the production costs. Of the $20.45 in inventory costs roughly two thirds come from the annual tool maintenance and storage costs.
Additionally, the 15 units per year over 5 years implies a total of 75 units while the optimal order quantity is greater at 87. If AM was not an option in this scenario a typical response would be to initiate an all time buy to cover the remaining demand.
4.3 Final Phase
We consider two sub-scenarios in this example.
4.3.1 AM vs TM all-time buy
All time buys to cover remaining demand are often triggered by to supply chain disruptions, vendor requirements, or excessive ordering costs. The uncertainty of the future demand generally requires purchasing more units be purchased than are expected on average resulting in an excess number of units. The total cost function can be modified to reflect the one-time order and the cost of the excess units.
T_ATB=U+K+Y(CD_a+hI_avg+A)+CE_ATB
where
EATB = expected excess units need to cover upper demand limit
Iavg = average inventory on hand = ((D_a Y-E_ATB ))/2+E_ATB
All other variables carry over from the TLC function.
The required excess number of units is reflective of the acceptable risk for the business instead of a need to cost optimize for a specific SKU. The total future demand can be model using a normal distribution. The mean and standard deviation of the distribution can be estimated using high and low estimated (example 5th and 95th percentile) demand level. Then using a stock out risk set by the business the purchase quantity can be directly calculated.
For the all-time-buy scenario the upfront tooling costs for TM are already paid and changing to AM will have some switching cost. Over 10 years the low and high demand level are estimated at 500 and 1000 total units for an average of 750. Assuming that the business has a maximum stock out risk of 5% 1000 units would be purchased for the all time buy.
Table 5 compares managing the remaining demand with recurring AM production and an all time buy of TM units; in this case sourcing from TM is more cost effective.
4.3.2 Dual sourced AM and all-time buy TM
A third option to sole sourcing the SKU is to dual source from both AM and TM. Some portion of the demand is covered by an all time buy from the TM source and the remaining demand is covered by recurring AM production. The total cost of the dual option is the sum of all time buy TM and recurring AM policies. It is the sequential nature (first use the TM parts then print the AM parts) that differentiates this approach from that in the 2021 paper by Knofius, N., van der Heijden, M.C., Sleptchenko, A., & Zijm, W.H.M. They present methods to evaluate if both AM and TM are concurrent sourcing options rather than and all time buy scenario.
For a given target stockout risk [SORT] a certain number of TM units should be purchased. Based on the number of TM units purchased there is an expected number of AM units needed and a number of excess TM units. Both of these values are positive, similar to how an inventory policy can have both a positive inventory on hand and a positive number of units on back order.
The optimal SORT can be found by searching a set of values from the business’s maximum stock out risk (in this example 5%) to 99% at preset increments. Searching SORT values less than the maximum is not needed as those are cover by the regular TM all time buy. And SORT values greater than 99% are nearly equivalent to sourcing all AM units.
Here is some guidance for estimating key parameters:
QTY of TM units purchased = QATB = Demand(1- SORT )
QTY of AM units required = [Demand(1- SORT /2) – QATB]*SORT
QTY of excess TM units =[QATB - Demand((1- SORT )/2)] *[1-SORT]
Table 6 shows the results of a small subset of SORT values for the example part. A target stock out risk of 75% yield the lowest cost dual source solution. Table 7 compares the optimal dual source cost to the optimal single source costs for AM and TM. In this scenario, dual sourcing offers a further cost improvement on the both of the single source options by leveraging the strengths of each.
Figure 3 shows how the risk of a stockout decreases as the number of TM parts increases. Even at the safety stock quantity of 1,000 units the risk of a stock out is not zero. Comparing to the optimized quantity (“Buy”) and the additional needed AM units (“+3D”) shows how leveraging AM as a secondary source can reduce the total number of units required.
Comparison with the Common Cost Assumptions
To facilitate the understanding of our proposed costing framework, it helps to contrast it with the common cost model assumptions employed for numerical experiments in the literature as listed below. These assumptions are convenient for numerical modeling and, in fact, required if data is limited. However, an operationalized framework should endeavor to use actual data to achieve the most accurate result. For this reason, we comment on each of these common assumptions listed below to caution potential pitfalls.
No upfront costs for tooling or design for AM or TM. In reality, spare parts may incur costs when switching to AM for design and validation. These costs will vary from part family to part family. Additionally, this assumption limits the framework to spare parts as new parts will have significant design, tooling, and validation costs.
Ordering cost is much lower than the unit production cost or the fixed ordering cost is a set ratio of the unit production cost. This assumption often leads to an (s, s-1) policy for both AM and TM. In reality, the fixed ordering cost is independent from the production costs and can vary greatly between AM and TM. For example, AM is less susceptible to supply chain disruption. Also, for some processes the ordering costs are much higher than the production cost for a single unit.
AM production cost is a set ratio of TM production cost. While it is reasonable to assume that AM unit production costs are higher than TM ratio between them is highly variable. Even if TM cost data is available the AM costs must be estimated separately.
AM lead time is a set ratio of the TM lead time. AM lead time is typically shorter than TM lead time but the ratio can vary greatly. The lead time for AM can be as short as a few days if in house or could nearly equal the TM lead time if outsourced.
Holding cost is a set ratio of the part’s production cost. Holding costs are a composite of many separate discrete factors like the cost of capital, warehousing, and obsolesce. While some factors like the cost of capital are uniform between parts, other, especially obsolesce, vary greatly from part to part.
To further explore these models a comparison can be made between an example presented in by Heinen and Hoberg (2019) (H&H for short) and scenario 2 in the previous section. Heinen and Hoberg considers SKU A with the properties listed in Table 8 columns 2 and 3. The values for AM production cost, TM ordering cost, AM lead time, and holding cost for both AM and TM are all direct percentages of the production cost for TM. Heinen and Hoberg consider back order costs in the same way but proved to be small and are excluded from this comparison for simplicity. In columns 4 and 5 are an alternative set of proposed values derived using the practices previously described in this paper.
Table 9 shows the resulting inventory policies a cost breakdown at the current demand level (9.6 units per year). We find the total cost for AM and TM are both higher and TM still proves to be the most cost effective option. The key difference between the two models is demonstrated in Figure 4. The methods proposed by Heinen and Hoberg yield the non-intersecting dashed curves for AM and TM; while in the proposed total cost framework there is a breakeven at 1.5 units per year.
The presence of a breakeven point can be attributed to the differences in how the inputted variables are estimated. Methods that assume the variables are proportional to the Ctm (h =20%, b = 200%, k=100%, Cam=200%) or the same between AM and TM (ie lead-time) will always generate non-intersecting curves because Ctm is effectively the only independent variable. The key exception is if the SKU has an MOQ; like SKU B in Heinen and Hoberg 2019. In order to accurately capture the nuances of inventory costs the variables of the total cost function must be measured for each business’s supply chain.
We established a unified, scalable total cost framework for companies to evaluate the AM opportunity for their big portfolios of part. The cost function contains cost factors that apply to parts in all stages in the lifecycle, the calculations are simple and can be easily implemented in a spreadsheet. Applying this tool in a variety of scenarios with industrial supported data, our primary finding is that the inventory costs must be considered in breakeven analyses for AM vs TM, especially for spare parts. In some scenarios the inventory costs have an outsized effect and change the outcome of the analysis if not been included. We contributed to the field by showing how a total cost model could be operationalized to measure all inventory costs and avoid being overly sensitive.
The presented examples focus on different scenarios across the product lifecycle for a single part, this research could be expanded by applying the analysis to a portfolio of spare part SKUs. Analysis at the portfolio level requires 1) integrations with ERP and PLM for key data 2) CAD driven costing tools for unit production and tooling costs 3) automated workflow to combine the discrete sub-analyses. Additionally, scenario 1 (low volume production) could be exampled to include a dual sourcing option where 3D functions as a rapid response source.
About the authors: Jeannette Song, Ph.D., is the R. David Thomas Professor of Business Administration and Professor of Operations Management in the Fuqua School of Business of Duke University. She can be reached at [email protected]
William McCall is the Director of Operations at Xerox Additive Manufacturing. He can be reached at [email protected]
Acknowledgements: The authors acknowledge the contributions of Russell E. King, Ph.D. and Tali Rosman. Russell E. King is the Henry A. Foscue Distinguished Professor of İndustrial and Systems Engineering at North Carolina State University. He can be reached at [email protected]. Tali Rosman is the general manager of additive manufacturing at Xerox Corporation. She can be reached at [email protected].
References
Atzeni, E., Salmi, A. (2012) Economics of additive manufacturing for end-usable metal parts. Int J Adv Manufacturing Technol, 62,1147–1155.
Cohen, M. A., Agrawal, N., Agrawal, V. (2006). Winning in the aftermarket. Harvard Business Review, 84, 129–138.
Daimler, A. G. (2017). Premiere at Mercedes-Benz Trucks: New from the 3D printer: The first spare part for trucks made of metal. Retrieved from http://media.daimler.com/marsMediaSite/en/instance/ko/Premiere-at-Mercedes-Benz-Trucks-New-from-the-3Dprinter-the-first-spare-part-for-trucks-made-of-metal.xhtml?oid=23666435.
D’Aveni, R. A. (2018). The 3-D printing playbook. Harvard Business Review, 96, 106–113.
Deutsche Bahn, A. G. (2018). 3D printing: Replacement on time increases train availability. Retrieved from https://www.deutschebahn.com/en/Digitalization/DB_Digital/productworld/
3dprint-1214672
Feldmann, C. & Pumpe, A. (2017). A holistic decision framework for 3D printing investments in global supply chains. Transportation Research Procedia, 25, 677-694, ISSN 2352-1465, https://doi.org/10.1016/j.trpro.2017.05.451
Foundry Management & Technology. (2019). Availability, Reliability Make the Case for 3DP. Retrieved from https://www.foundrymag.com/materials/media-gallery/21932037/availability-reliability-make-the-case-for-3dp
Global Market Reports. (2020). Global Metal Spare Parts Market. Retrieved from https://growthmarketreports.com/report/metal-spare-parts-market-global-industry-analysis
Heinen J. & Hoberg K. (2019). Assessing the potential of additive manufacturing for the provision of spare parts Journal Operations Management, 65, 810–826. https://doi.org/10.1002/joom.1054
Holmström, J., & Gutowski, T. (2017). Additive manufacturing in operations and supply chain management: No sustainability benefit or virtuous knock-on opportunities? Journal of Industrial Ecology, 21, 21–24.
Holmström, J., Partanen, J., Tuomi, J., & Walter, M. (2010). Rapid manufacturing in the spare parts supply chain: Alternative approaches to capacity deployment. Journal of Manufacturing Technology Management, 21, 687–697.
Holweg, M. (2015). The limits of 3D printing. Retrieved from https://hbr.org/2015/06/the-limits-of-3d-printing.
Holweg, M., & Pil, F. K. (2004). The second century: Reconnecting customer and value chain through build-to-order. Cambridge, MA: MIT Press.
Kellner, T. (2017). An Epiphany Of Disruption: GE Additive Chief Explains How 3D Printing Will Upend Manufacturing. General Electric Report. Retrieved from https://www.ge.com/news/reports/epiphany-disruption-ge-additive-chief-explains-3d-printing-will-upend-manufacturing
Kennedy, W., Patterson, W. J., & Fredendall, L. D. (2002). An overview of recent literature on spare parts inventories. International Journal of Production Economics, 76, 201–215.
Khajavi, S. H., Deng, G., Holmström, J., Puukko, P., & Partanen, J. (2018). Selective laser melting raw material commoditization: Impact on comparative competitiveness of additive manufacturing. International Journal of Production Research, 56, 1–23.
Khajavi, S. H., Holmström, J., & Partanen, J. (2018). Additive manufacturing in the spare parts supply chain: Hub configuration and technology maturity. Rapid Prototyping Journal, 24, 1178–1192.
Knofius, N., van der Heijden, M. C., & Zijm, W. H. M. (2016). Selecting parts for additive manufacturing in service logistics. Journal of Manufacturing Technology Management, 27, 915–931. https://doi.org/10.1108/JMTM-02-2016-0025
Knofius, N., van der Heijden, M. C., & Zijm, W. H. M. (2018). Moving to additive manufacturing for spare parts supply. In A. Chikán (Ed.), Book of abstracts: 20th international symposium on inventories (p. 62). Budapest, Hungary: International Society for Inventory Research.
Knofius, N., van der Heijden, M.C., Sleptchenko, A., & Zijm, W.H.M. (2021). Improving effectiveness of spare parts supply by additive manufacturing as dual sourcing option. OR Spectrum, 43, 189–221. https://doi.org/10.1007/s00291-020-00608-7
Lindemann, C., Reiher, T., Jahnke, U., & Koch, R. (2015). Towards a sustainable and economic selection of part candidates for additive manufacturing. Rapid Prototyping Journal, 21, 216–227.
Protolabs. (2021). Change is Good: The Evolution of a Digital Quoting Platform. Retrieved from https://www.protolabs.com/resources/blog/change-is-good-the-evolution-of-a-digital-quoting-platform/
Sirichakwal, I. & Conner, B. (2016), Implications of Additive Manufacturing for Spare Parts Inventory. 3d Printing and Additive Manufacturing, 3,53-56
http://doi.org/10.1089/3dp.2015.0035
Song, J. & Zhang, Y. (2020). Stock or Print? Impact of 3D Printing on Spare Parts Logistics.
Management Science, 66, 3086-3878.
Varotsis,A. (2018). From CAD to CNC in 3 Steps. Retrieved from https://www.machinedesign.com/3d-printing-cad/article/21837356/from-cad-to-cnc-in-3-steps
Volvo, C. E. (2018). Volvo CE moves into 3D printing of parts. Retrieved from https://www.volvoce.com/global/en/news-andevents/news-and-press-releases/2018/volvo-ce-moves-into-3dprinting- of-parts/.
Wagner, S. M., Jönke, R., & Eisingerich, A. B. (2012). A strategic framework for spare parts logistics. California Management Review, 54, 69–92.
Wagner, S. M., & Lindemann, E. (2008). A case study-based analysis of spare parts management in the engineering industry. Production Planning and Control, 19, 397–407.
Wagner, S. M., & Walton, R. O. (2016). Additive manufacturing’s impact and future in the aviation industry. Production Planning & Control, 27, 1124–1130.
Walter, M., Holmström, J., Yrjölä, H. (2004). Rapid manufacturing and its impact on supply chain management, in: Proceedings of the Logistics Research Network Annual Conference 2004, Dublin, Ireland.
Westerweel, B., Basten, R. J. I., & van Houtum, G. J. (2018). Traditional or additive manufacturing? Assessing component design options through lifecycle cost analysis. European Journal of Operational Research, 270, 570–585.
Xometry. (2020). What is the 3D Printing vs Injection Molding Cost-per-Unit Breakeven? Retrieved from https://www.xometry.com/blog/3d-printing-vs-injection-molding-breakeven/
Xometry. (2021). How Instant Quoting is Revolutionizing the Manufacturing Industry. Retrieved from https://www.xometry.com/blog/instant-quoting-revolutionizing-manufacturing-industry/
Zhang, Y., Westerweel, B., R. Basten, J.-S. Song. (2020). Distributed 3D printing of spare parts via IP licensing. https://papers.ssrn.com/sol3/papers.cfm?abstract_id=3682086
Zipkin, P. (2000). Foundations of inventory management. McGraw-Hill Book Co.
SC
MR
MR

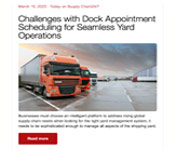
Latest Supply Chain News
- Balanced supply chain management Part 4: The key—leading beyond the silo
- Managing inbound freight: What has changed in two decades?
- Inbound freight: Often a missed opportunity
- Aggregators sitting on the throne of Africa’s e-commerce supply chains: What lessons can we learn?
- Cross-border transport 2024: Navigating the surge
- More News
Latest Resources

Explore
Latest Supply Chain News
- Balanced supply chain management Part 4: The key—leading beyond the silo
- Managing inbound freight: What has changed in two decades?
- Inbound freight: Often a missed opportunity
- Aggregators sitting on the throne of Africa’s e-commerce supply chains: What lessons can we learn?
- Cross-border transport 2024: Navigating the surge
- Nine questions are the key to AI success in building resilient supply chains
- More latest news
Latest Resources
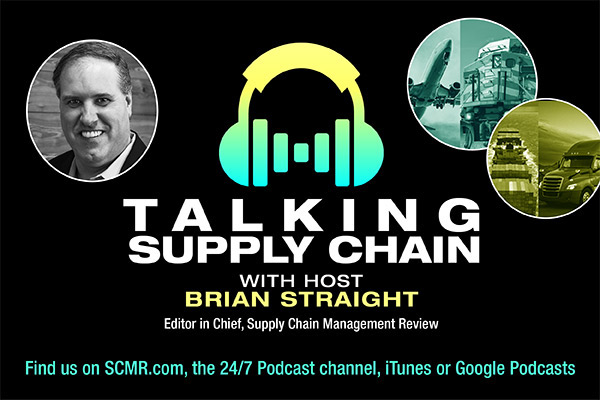
Subscribe
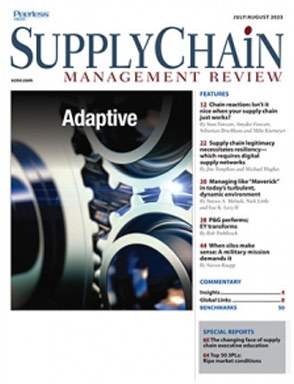
Supply Chain Management Review delivers the best industry content.
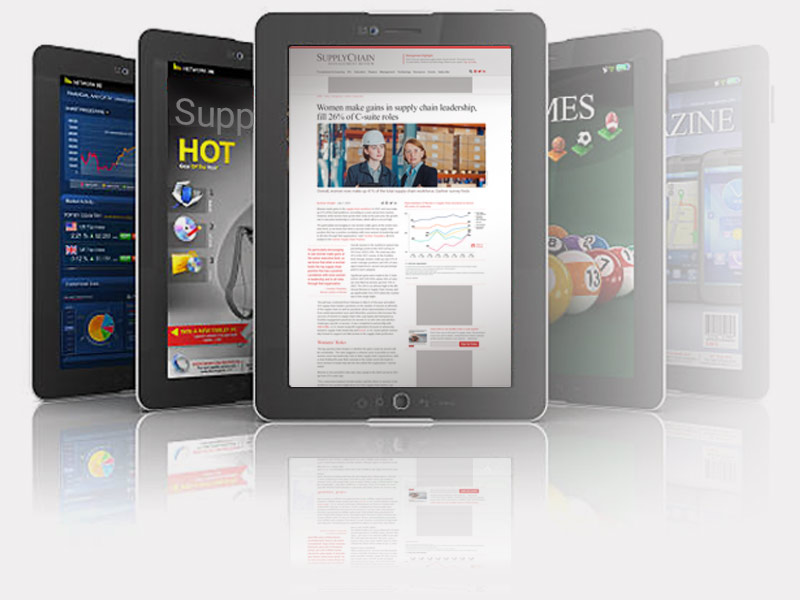
Editors’ Picks



