Warehouse automation has evolved over the past few decades - from the use of sortation systems to conveyors/AGV's to RFID systems to complex WMS and WCS systems. In recent years, the focus on being able to profitably cater to customer's preferences and omnichannel fulfillment strategies has led companies to aggressively seek advanced automation and robotics solutions.
The pressure of managing labor shortages in concert with wage hikes while improving speed and accuracy of operations to increase productivity per square foot are driving organizations to look at advancements in technologies to help them control the three big costs—labor, time and real estate.
For example, companies are now investing heavily in robotics in their warehouses and distribution centers, with Amazon leading the way. Vision and computer guided robots are performing storage and handling activities such as loading, unloading, putaway and retrieval functions. Autonomous robots travel untethered among storage racks in a distribution center and move up and down aisles to stack and retrieve cases. They coordinate with more-conventional robots that perform simpler tasks to enable fulfilment. We're even seeing camera-mounted drones being used to take inventory in the warehouse. Kroger, Walmart, Macy's, Target and Coca-Cola are just a few leading companies that are testing and investing in the next generation of advanced warehouse automation. Their use is the next logical step to leverage efficiencies in supply chains that are already under severe pressure to speed up order fulfillment and reduce costs.
While investing in advanced automation might seem to be the best way to manage fulfillment, the analysis to determine the best fit and return on investment is often insufficient or influenced by the automation and robotics manufacturer or reseller. Before signing off on any investment in automation, companies must be able to filter out the noise - both positive and negative - and perform due diligence based on strategic fit and sound analytics to determine what is the right solution for them.
In our interactions, we find that there is a significant interest in incorporating advanced automation and robotics, especially by e-commerce companies. We have also observed that companies have achieved varying levels of success, and often failure, in warehouse operations with and without automation. We're familiar with a leading distributor of pharmaceuticals and medical equipment whose main DC can handle large volumes with mostly manual operations and a large cosmetics company was forced to discard its automation over time due to cost pressures arising from changes in business environment and acquisitions that did not conform to existing operations.
In another case, new automation had been improperly evaluated and was underutilized, leading to a higher handling cost per unit and lower throughput as compared to manual processes.
On the other end of the spectrum are companies like Amazon, which has executed its automation strategy well and is looking to expand its footprint of robotics to additional warehouses. Also, a leading fast fashion e-commerce company has leveraged an automated RFID-based pouch sortation system to assemble an order for a customer that enables a 24-hour cycle time from checkout to ship.
Investing in advanced automation and robotics has plenty of upside and addresses a number of challenges faced by warehouses today:
• Robotics deliver a quicker return on Investment and pare labor costs over the long term – estimates range from reducing labor costs by 80% and operating costs by about 20%, according to reports in the Wall Street Journal and Bloomberg.
• Automation address the issue of labor shortages - eliminates concerns on overtime, shift scheduling, peak season spikes etc.
• It also reduces the risk of workplace injuries and safety related claims
• The Journal also reports that at a time when the growth of e-commerce is driving up commercial rents, automation enables better use of space available with an estimated reduction of warehouse sizes by up to 25% to 40%.
Despite the benefits, advanced automation and robotics come with a hefty price tag. The initial investment in the technology can be prohibitive – anywhere between $40-to-$100 million by some reports - depending on the size and complexity. In addition, partial automation in a network of warehouses can potentially lead to a sub-optimal performance and/or increase in operational costs.
Another consideration that often gets ignored during the decision making is the lifecycle of the hardware and software. Often times the technology applications outrun the hardware systems. A report in Inbound Logistics estimated that the useful life of software systems in distribution applications will sustain only 25 percent of the projected lifespan of an automated hardware implementation.
Also, today's commercially feasible robots are only capable of doing a small piece of the work involved in processing an order. While very efficient, these robots are limited to case/pallet level of operations. They transport shelves to associates who pick items from the shelf and put them to a shipping carton, or, they convey a tote to a pick location, where an associates retrieves the item needed. While progress is being made in getting robots to detect and pick a single item from a carton or bin, but we are at early stages in their adoption.
Taking a scientific approach
Organizations operate at different levels of maturity and there is no one size fits all solution to automation. The automation needs of an organization should be driven by the goals they are trying to achieve and the problems they are looking to solve. Before making a large investment, we suggest that companies conduct a detailed data driven, fact-based assessment across people, process and technology to identify the right fit. A good approach includes:
• Identifying the company's strategic objectives and direction
• Understanding the maturity of warehouse operations, complexity of processes, existing automation, technology landscape and labor management practices
• Developing a detailed operations profile, determine distribution cost per unit (CPU) and overall cost to serve
• Studying and analyzing individual process performance and efficiency to benchmark operations, performance and costs against industry standards
• Identifying the gaps, improvements and the strategy for automation to achieve desired objectives
• Use optimization and simulation tools to analyze warehouse performance by determining tradeoffs on improving existing processes vs. making new investments and validating the return on investment of the proposed initiatives
• Developing a logistics operating model by aligning the organization long term goals, growth plans to the operations strategy and planned initiatives
This exercise should not be carried out in isolation but should comprise a cross-functional team of warehouse engineers, HR, finance and management. By performing a scientific assessment and benchmarking operations, organizations can create a roadmap that results in best in class logistics by incorporating process improvements and right level of the automation at appropriate phases. While there is no wrong time to consider automation in the warehouses, the optimal time to perform an assessment is when a distribution center expands, relocates, or consolidates. It is also possible that sometimes investing in automation is not necessarily the best option, but could be down the line at a later stage.
Make an impact
While e-commerce companies are leading the way in the adoption of advanced automation and robotics, it does not mean that other industries should lag behind. There is significant momentum to buy newer technologies, but the real challenge is identifying the right replacement and determining what level of automation is best suited for the organization. All industries – and organizations with complex distribution requirements - should learn lessons from the early adopters and invest time in analytically identifying those technologies that align with the business strategy and will have the most impact on their warehouse operations.
About the Authors
Venkat Madduri is a business analyst in TCS’ Supply Chain Consulting & Services Integration practice. Mark Newberry is a partner in TCS’ Supply Chain Consulting & Services Integration practice. Andrew Crane is a senior consultant in TCS’ Supply Chain Consulting & Services Integration practice. They can be reached at [email protected], [email protected], [email protected].
SC
MR
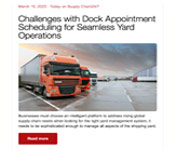
More Automation
- Looking back at NextGen 2024
- AI is moving omnichannel closer to the customer
- Robotic use grows by 10%
- The art of winning at supply chain technology: Lessons from managing tech for the largest private trucking fleet in the U.S.
- NextGen Supply Chain Conference set for October 21-23
- How to identify and eliminate internal demons in supply chain management
- More Automation
Latest Podcast
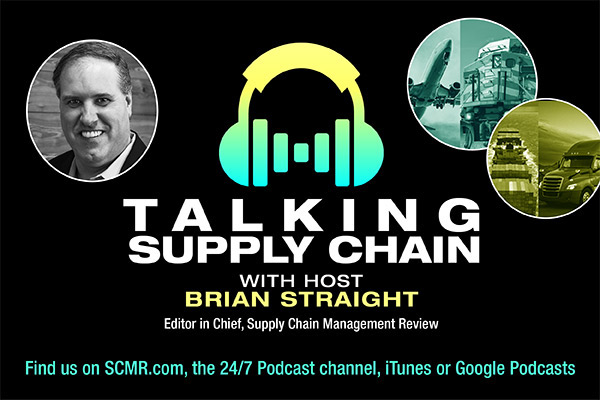
Explore
Topics
Software & Technology News
- Nine questions are the key to AI success in building resilient supply chains
- Looking back at NextGen 2024
- AI is moving omnichannel closer to the customer
- How technological innovation is paving the way for a carbon-free future in logistics and supply chains
- Körber Supply Chain Software’s Craig Moore says MercuryGate acquisition is about the customer
- Robotic use grows by 10%
- More Software & Technology
Latest Software & Technology Resources
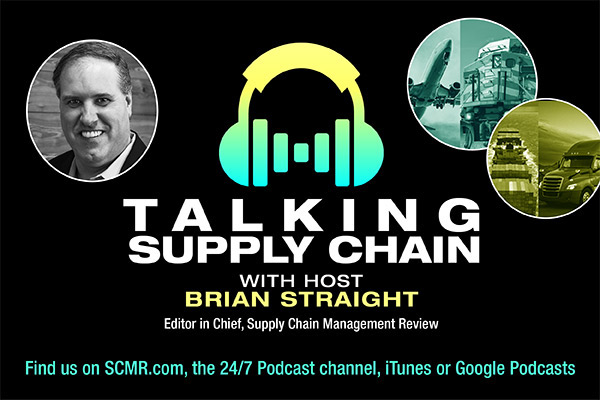
Subscribe
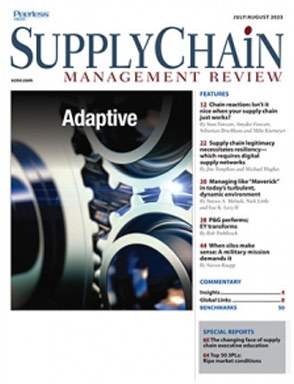
Supply Chain Management Review delivers the best industry content.
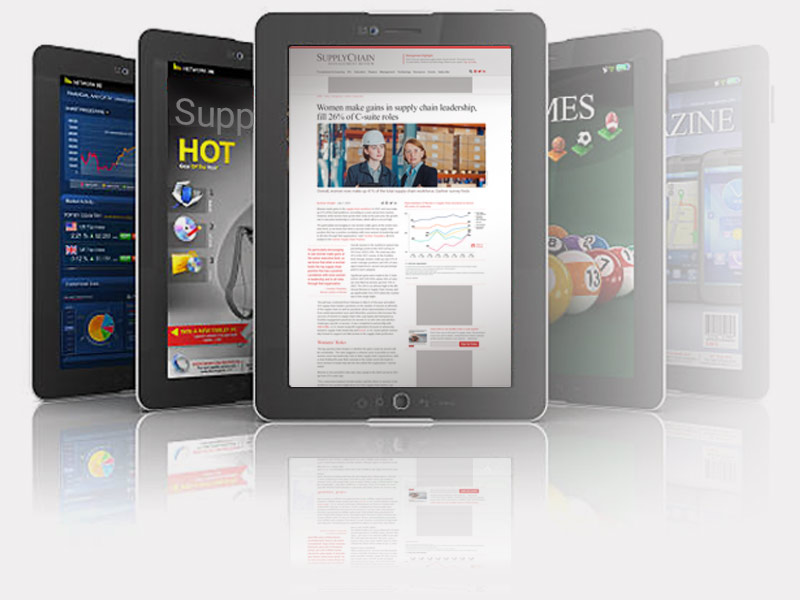
Editors’ Picks

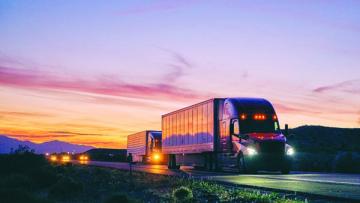

