Braskem, a multi-billion dollar petrochemical company, is confronting a business challenge most companies would envy: Over the next several years, its global supply chain must expand to to handle a projected 30% increase in volume. Making the most of digital technologies for major efficiency gains is one obvious key to success. The question for any company trying to increase and accelerate its supply chain capabilities is what approach will enable it to reach that goal?
The answer for Braskem, working in conjunction with A.T. Kearney, is to apply the Agile process pioneered for rapid software development to its supply chain. Agile is enabling Braskem to pursue major performance breakthroughs while working in small, rapid increments that yield quick but tangible results with very low risk.
For those unfamiliar with the term, Wikipedia defines Agile as follows:
“Agile software development is an approach to software development under which requirements and solutions evolve through the collaborative effort of self-organizing and cross-functional teams and their customer(s)/end user(s). It advocates adaptive planning, evolutionary development, early delivery, and continual improvement, and it encourages rapid and flexible response to change.” Figure 1 illustrates the process.
[Figure 1: Agile process]
To begin the process, A.T. Kearney led a workshop to orient Braskem's North America supply chain team to the Agile process. Amazon Web Services contributed insights based on its extensive experience. Following the workshop, Braskem began actively experimenting with Agile through a series of steps:
Step 1. Assembled a cross functional team (supply chain planning, operations, customer service, procurement, sales and IT) which first defined North Star—a visionary future state for supply chain performance—then ideated a list of possible initiatives to achieve that vision.
Step 2. Launched six Agile initiatives in parallel, rapidly experimenting with potential solutions. One such initiative was to leverage Robotic Process Automation (RPA) to automate shipping and inventory picking operations. The bot-based solution eliminated inventory inaccuracy in a pilot warehouse within eight weeks.
Step 3. Scaled successful solutions. For example, the bot-based solution was brought to four other terminals, automating 50% of all rail car shipments and eliminating 80% of the warehouse operators' computer tasks within two months. This relieved shipping personnel from tedious transactional activities so they could focus more on exceptions that require human attention. This also freed up capacity to address unique client requirements and to take on higher volumes of work as the company grows.
Because Agile originated in the software industry, some may assume it is only applicable in the IT world. However, Braskem's cross-functional Agile teams are effectively tackling business process challenges as well.
For example, as the company's business volume grows, blind spots in customer service and supply chain are more problematic. Sales representatives too often need to check with supply chain before they can commit to the inventory availability requested by their customers, while customer service reps don't have all the information they need to immediately update customers that are inquiring about the status of their orders. To address those issues, Agile team members from three functions (sales, customer service and supply chain) concurred that they were spending too much time chasing each other for information, which in turn hindered their efforts to sustain and improve service levels as the company grows.
Supply chain leadership considered implementing a SAP/Transportation Management System. That, however, would have been a big ticket item that would likely take a year or more to implement. Instead, IT joined the Agile team to seek more immediate solutions.
First, the team carefully specified the kinds of information required by each role in customer service and supply chain to effectively meet customer needs. Customer service, for example, needs to know when an order was promised and if delivery may be delayed. Supply chain needs timely, accurate forecasts of upcoming product demand. Operations needs current information on inventory availability to begin shipment tendering activity.
In response, the Agile team decided to pursue a straightforward “minimum viable product” that ensures that every role has the information it needs at its fingertips. Relatively simple tweaks in the company's existing planning software provided access to much of the targeted information; as a result, supply chain activity is now more frequently updated and the software is more widely accessible. Today, all the players know if orders are being processed on schedule and who to consult to resolve order issues or make schedule adjustments. Sales can more confidently make inventory availability commitments to customers.
It hasn’t all been smooth sailing. Initially, there was skepticism as to whether an approach designed for software development could be applied to the challenges of a global supply chain. The Braskem team also needed to adjust its resource commitments. While IT organizations are intrinsically project-based, lending themselves to participation in Agile teams, Braskem's problem-solving expertise resides in operations people whose jobs demand their attention throughout the day.
With experience, those early doubts quickly dissipated. Operations employees tend to be gratified when they can achieve meaningful results quickly—especially when the solutions they generate remove frustrating obstacles from their own work. And, being part of high-profile Agile projects also provides more opportunities for Braskem's people to showcase their skills and experience leadership roles. And, by carefully monitoring the outcomes of the projects, Braskem leadership has found that devoting some of its human capital to Agile initiatives makes sound business sense.
Agile has also helped close the distance between business operations and IT, as the process allows those functions to roll up their sleeves together to solve shared problems. There is now a much stronger sense of partnership and collaboration across the company's high tech and operations specialists.
Just over a year into the experiment, Agile is proving a uniquely practical response to the growing complexity in Braskem's business landscape. It simplifies complex problems to their core, and then generates solutions that can be piloted and proven in a matter of weeks. This stands in clear contrast with the more common tendency to respond to complex problems with complex solutions that can take years to implement.
In an operating environment that changes from one month to the next, long-term solutions may no longer be applicable when they finally come to fruition, leaving an organization even further behind than when it started. Agile, on the other hand, responds to complexity with simplicity. And that is a key to ensuring supply chains can continually adapt in real time.
Kevin Towles is Director, Planning, Strategy, and Product Management at Braskem, where he leads North American Supply Chain.
Abhinav Agrawal is a Partner in the Digital Practice of A.T. Kearney, the global management consulting firm.
Andrew Walberer is a Partner in A.T. Kearney’s Chemicals Industry Practice.
Balu Balagopal is a Partner in A.T. Kearney's Energy & Process Industries Practice.
SC
MR
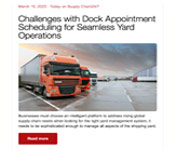
Latest Supply Chain News
- Made in Mexico, manufactured by China
- Retail sales see gains in October, reports Commerce and NRF
- Balancing green and speed: Home delivery insights from the pandemic era
- AdventHealth named top healthcare supply chain by Gartner
- Geopolitical readiness in supply chains: Strategic challenges for leaders
- More News
Latest Podcast
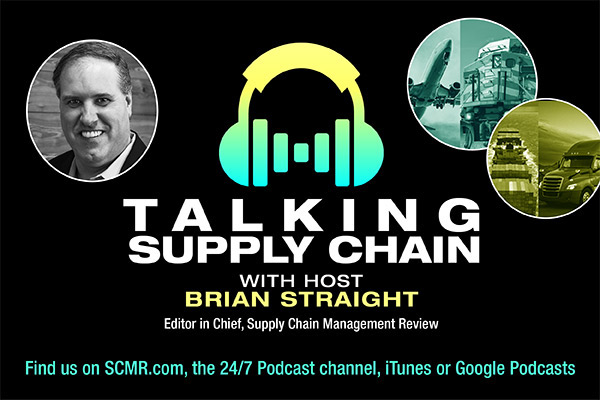
Explore
Latest Supply Chain News
- Made in Mexico, manufactured by China
- Retail sales see gains in October, reports Commerce and NRF
- Balancing green and speed: Home delivery insights from the pandemic era
- AdventHealth named top healthcare supply chain by Gartner
- Geopolitical readiness in supply chains: Strategic challenges for leaders
- Unlocking retention: The role employee engagement plays
- More latest news
Latest Resources
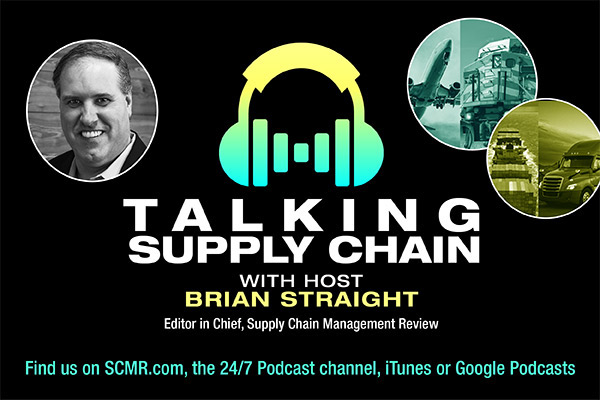
Subscribe
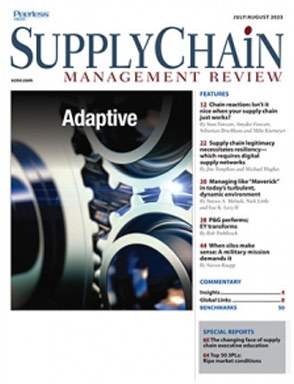
Supply Chain Management Review delivers the best industry content.
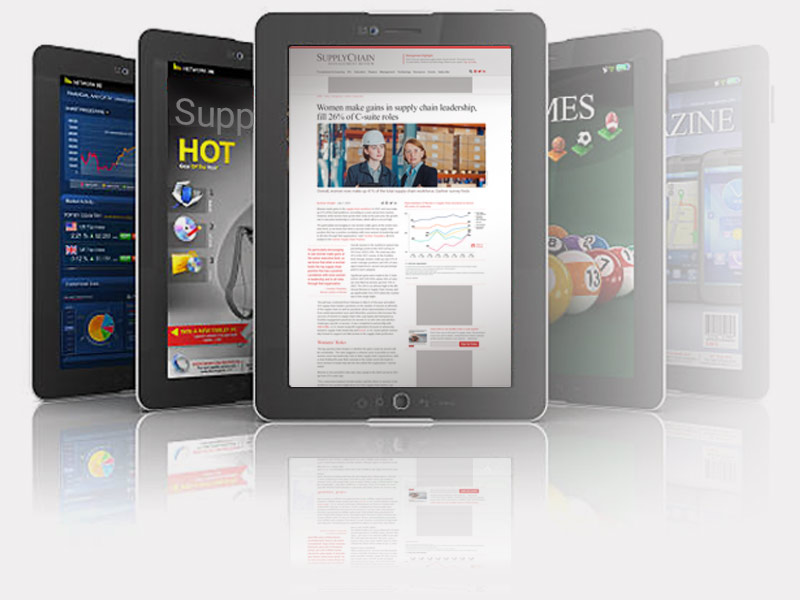
Editors’ Picks

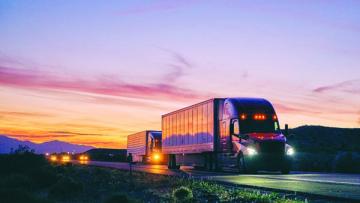

