Editor’s Note: Boris Shiklo is CTO at ScienceSoft, where he is responsible for the company's long-term technological vision and innovation strategies. Under his supervision, the company's development team has successfully fulfilled complex projects of over 80,000 man-hours in Healthcare, Banking & Finance, Retail, Telecommunications, Public Sector and other domains.
According to the recent survey conducted by Geodis, 77% of enterprises claim to have limited visibility into their supply chains, which results in frequent delivery delays and demand-supply mismatches. The good news is that these issues can be mitigated with the Industrial Internet of Things (IIoT). Applied for supply chain optimization, IIoT addresses the root cause of supply chain inefficiencies – the lack of prompt and reliable supply chain data – and thus eliminates its consequences.
To realize the promised benefits, enterprises may start the implementation of IIoT-driven solutions with a basic architecture and then expand it both vertically (adding new architecture components and improving solution's technical capabilities) and horizontally (using the established technological infrastructure to digitize another supply chain segment).
In this article, we'll show how to roll out IIoT solutions for the supply chain in a way that allows boosting the agility of supply chain processes without incurring excessive investments.
Four steps to supply chain digitalization
Manufacturing supply chains are complex in terms of the number of players they comprise (e.g., material suppliers, procurement managers, buyers, inventory managers, etc.) and the interactions among these players. Rolling out an IIoT solution that caters for the needs of all supply chain participants at once is an effort-intensive initiative that is impractical from the investments perspective. A much more feasible scenario is to opt for the iterative approach to supply chain digitalization, which involves the following steps:
- Step 1. Assessing the current level of supply chain visibility and identifying the least transparent supply chain segments, e.g., procurement, warehousing, outbound deliveries.
- Step 2. Rolling out a basic IIoT solution built on a simple and flexible architecture to optimize supply chain segments with the lowest transparency.
- Step 3. Amplifying the solution's functionality with advanced components such as predictive analytics and control applications (vertical expansion).
- Step 4. Extending the solution's scope to other supply chain segments (horizontal expansion).
Step 1. Assess the supply chain visibility and identify the starting point of the supply chain transformation
An effective supply chain transformation starts with a comprehensive evaluation of supply chain visibility. For that, it is critical to identify which data about supply chain operations is available to the supply chain players and to which extent the available data is accurate, up-to-date, and representative of reality.
Once you have uncovered existing visibility flaws, determine which supply chain segments are affected by the limited availability of data the most. Say, you manufacture temperature-sensitive products. Once you've loaded the products into trucks, you lose track of the products' conditions and get your customer's feedback regarding product quality only upon delivery. To address this issue, it makes sense to start the digital transformation of your supply chain with monitoring product conditions within the outbound deliveries segment by equipping the trucks with temperature sensors and connecting the sensors to the cloud software.
Step 2. Transform the supply chain
Irrespective of what supply chain segment you choose to digitize first, it makes sense to start an IIoT solution implementation with a basic architecture flexible enough to allow for further expansion. An IIoT architecture making up the foundation of solutions for the supply chain management usually comprises the following layers:
- Data collection layer Depending on a solution's purpose, the data collection layer may comprise RFID tags (used for tracking the locations and properties of items) or sensors (used for monitoring temperature, humidity, and other ambient parameters in which products are stored and transported) attached to product packages, crates, warehouse shelves, or trucks used for product transportation.
- Data filtering layer The data filtering layer is presented by field and cloud gateways. Field gateways are hardware devices that serve as a link between sensors, RFID readers and the cloud part of an IoT solution. Field gateways take data from sensors and/or RFID readers and preprocess it, which includes aggregation and message filtering. The cloud gateways ensure smooth and secure data transmission between the filed gateways and the cloud part of an IIoT solution.
- Data storage layer The data storage layer is comprised of a data lake and a big data warehouse. A data lake stores all the incoming data in its raw form. Once the data is required for analysis, it is extracted from a data lake and loaded to a big data warehouse. Apart from the data about items' locations and ambient conditions collected from RFID tags and sensors, the big data warehouse stores metadata (e.g., the information about RFID readers' installation time and locations), as well as contextual information – past product sales data, regional demand figures, etc. – fetched from ERP.
- Descriptive analytics layer The descriptive analytics layer allows finding trends and correlations in the data fetched from RFID tags and sensors and visualizing the obtained insights in the form of easy-to-understand reports. This allows supply chain players to gain an at-a-glance view into such supply chain management aspects as inventory availability and distribution, statuses of inbound and outbound deliveries, and more.
- User communication layer The user communication layer enables bi-directional communication between the supply chain specialists and an IIoT system. For example, a specialist can use a web or a mobile application to request information from an IIoT system (e.g., search for product items, check items' properties) and supply an IIoT system with additional context information (e.g., add properties to an SKU description).
Step 3. Amplify the solution's functionality
Once you have a basic IIoT solution implemented, and it drives operational and business improvements, you may want to consider expanding the solution's technical capabilities by integrating the following advanced components:
- Predictive analytics Predictive analytics allows deriving actionable insights from multiple data sources and detecting the combinations of factors that have an effect on the supply chain efficiency. One of the areas where predictive analytics drives substantial improvements is inventory optimization. For inventory optimization, a data set that includes historical sales data, regional demand figures, and information about current inventory volumes across multiple storage facilities is run through machine learning (ML) algorithms. The ML algorithms detect the correlations hidden in the data to recommend inventory volumes required for the upcoming production cycle, and offer the way to distribute inventory across storage facilities according to the regional demand and seasonality.
- Control applications Control applications allow an IIoT solution to function with a certain degree of automation. For instance, an IIoT-based inventory management solution can be integrated with a warehouse heating, ventilation, and air conditioning (HVAC) system to provide for real-time temperature adjustments. The analytics component of an IIoT solution analyzes the data from temperature sensors installed throughout a warehouse against the data about products' recommended storage conditions and their shelf time to dynamically adjust the warehouse temperature. Then control applications send a command to HVAC system's actuators to adjust the temperature in order to maintain appropriate product storage conditions.
Step 4. Extend the solution's scope to other supply chain segments
Once you see that an IIoT solution pays off in a given supply chain segment, you can use the established infrastructure to make IIoT work for another segment of the supply chain as well.
For instance, a manufacturer uses an inventory tracking system for tracking the locations of their inventory items in a manufacturing facility and a local warehouse.
The company sees value driven by the inventory tracking solution and decides to extend the solution's scope to monitoring outbound deliveries and order fulfillment. The manufacturer deploys a network of RFID readers across regional distribution centers and connects the readers to the already available cloud software. Now, as RFID-labeled products are delivered to the distribution centers, they are automatically scanned by the RFID readers, which transmit the information to the cloud software. The manufacturer can remotely track whether all of the requested products are delivered and whether the order is fulfilled on time.
To sum it up
Implementing connected supply chain solutions iteratively helps to start getting a payoff earlier, as even a basic IIoT solution can already drive operational improvements. To be able to scale, make sure the initial architecture is flexible enough to allow integrating new architecture modules and extending the solution's functionality to other segments of the supply chain.
SC
MR

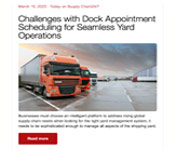
Latest Supply Chain News
Latest Podcast
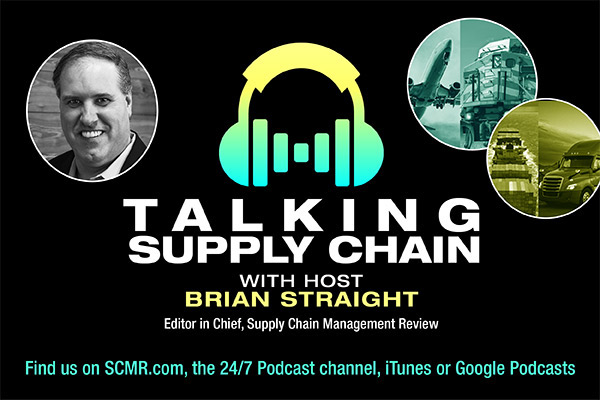
Explore
Business Management News
- AdventHealth named top healthcare supply chain by Gartner
- Unlocking retention: The role employee engagement plays
- Can supply chain managers embrace an entrepreneurial mindset?
- Challenges to ESG reporting
- With capacity to spare, logistics real estate demand remains subdued
- How to improve demand forecasts for new product families
- More Business Management
Latest Business Management Resources
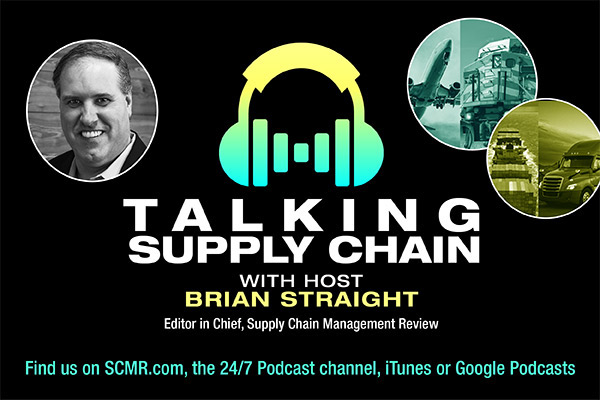
Subscribe
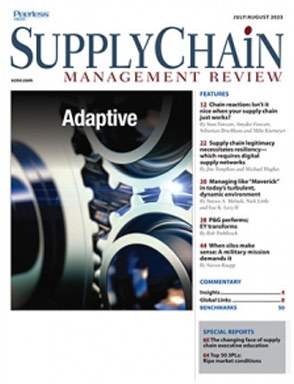
Supply Chain Management Review delivers the best industry content.
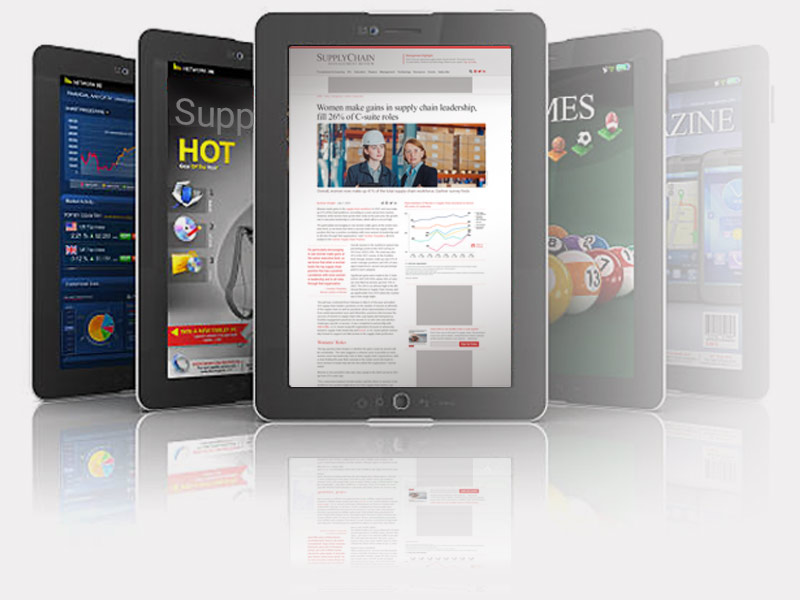
Editors’ Picks

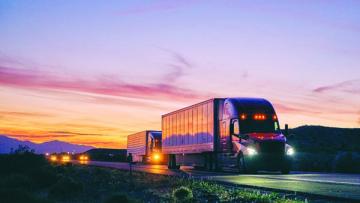

