Editor’s Note: The SCM thesis Tradeoffs in Strategic Capacity Planning Under Demand Uncertainty was authored by Jimmy Rose and Matthias Stolz and supervised by Dr. Maria Jesus Sáenz ([email protected]). For more information on the research, please contact the thesis supervisor.
In the medical device industry, supply chain investment decision-making can be especially challenging. New, innovative products with uncertain demand forecasts combined with complex supply chains that have long investment lead times can make it difficult for decision-makers to minimize the risk of lost sales. Hence, these investment decisions can significantly impact a company’s customer satisfaction ratings and financial performance.
Under these circumstances, how should medical device companies decide how much to invest in their supply chains while taking the uncertainty of their demand forecasts into account? These questions are often too complex for subject matter experts to answer effectively using traditional tools and methodologies.
New analytical approaches are needed that allow for the visualization, exploration, and quantification of the tradeoffs between scenarios to make informed decisions.
Developing a comprehensive yet applicable methodology
To better understand these challenges, we worked with a global developer, manufacturer, and marketer of medical devices that frequently faces complex strategic supply chain investment decisions. We combined the key insights gained from executive interviews with an extensive literature review, to develop an alternative modeling methodology. The methodology evaluates the impacts of different levels of demand uncertainty and business rule constraints on supply chain investment decisions and the risk of lost sales. Our methodology also leverages scenario simulation, optimization, and visualization tools.
Leveraging the power of visualization
To test our methodology, we modeled the supply chain for a set of medical devices used in surgical procedures. We began by simulating demand forecasts for existing products as well as two new products. The new products were planned replacements for existing ones, creating more uncertainty for supply chain investment decision-makers in both the timing of new product adoption and the magnitude of potential sales.
To manage the number of scenarios to be optimized while ensuring that an appropriate range of demand uncertainties could be quantified, the number of scenarios was reduced based on quartile boundaries. A total of 2,400 scenarios were optimized using actual supply chain capacities, costs and lead times for expansion, and budget constraints. To manage a large number of optimization outputs, we designed a business intelligence (BI) dashboard so that the results of the optimizations could be visualized and optimized.
From intuitive to less intuitive insights
The test results for our project sponsor’s supply chain yielded the following insights:
- Exploring a large range of demand uncertainties can determine how sensitive a supply chain is to demand changes.
- Scenario reduction based on uncertainty coverage efficiently reduces the number of required optimizations while still allowing the impacts of demand uncertainty to be evaluated.
- The methodology developed during this project identifies primary and secondary capacity bottlenecks and the investments required to eliminate those bottlenecks.
- Investment decisions are particularly sensitive to investments in capacity and inventory levels; constraining one increases and advances investment in the other, as inventory pre-builds and capacity investments are direct tradeoffs.
- Constraining both manufacturing capacity and inventory generates solutions with higher total costs.
Visualization through BI dashboards allows for scenarios to be identified and compared quickly and easily and reveals less intuitive insights to support decision-making tradeoffs. It is primarily through the less intuitive insights that new value is created, as these insights reveal ways to either reduce risk or improve investment efficiencies that are not identified using traditional methods.
Every year, approximately 80 students in the MIT Center for Transportation & Logistics’s (MIT CTL) Master of Supply Chain Management (SCM) program complete approximately 45 one-year research projects.These students are early-career business professionals from multiple countries, with two to 10 years of experience in the industry. Most of the research projects are chosen, sponsored by, and carried out in collaboration with multinational corporations. Joint teams that include MIT SCM students and MIT CTL faculty work on real-world problems. In this series, they summarize a selection of the latest SCM research.
SC
MR

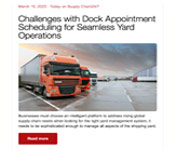
Latest Supply Chain News
Latest Podcast
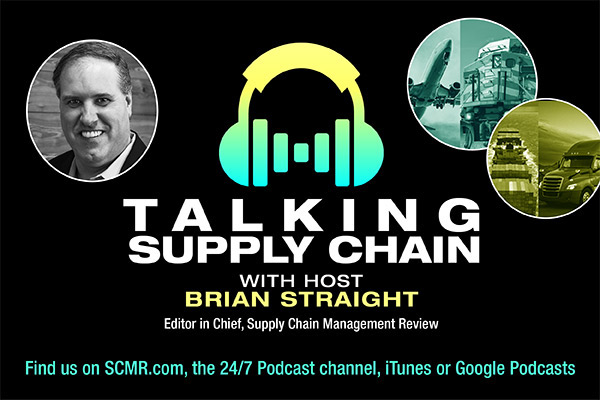
Explore
Latest Supply Chain News
- Strengthening customer fulfillment: Building a strategic stakeholder network
- The hard job of teaching soft skills
- Trump picks former Wisconsin congressman Sean Duffy for DOT secretary
- Made in Mexico, manufactured by China
- Retail sales see gains in October, reports Commerce and NRF
- Balancing green and speed: Home delivery insights from the pandemic era
- More latest news
Latest Resources
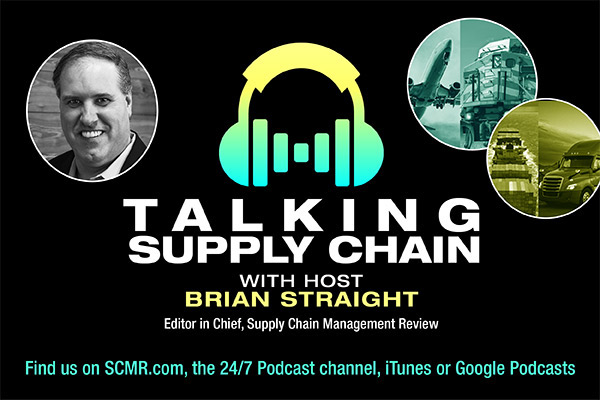
Subscribe
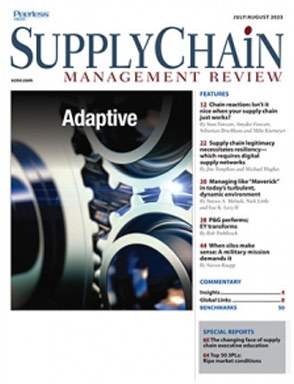
Supply Chain Management Review delivers the best industry content.
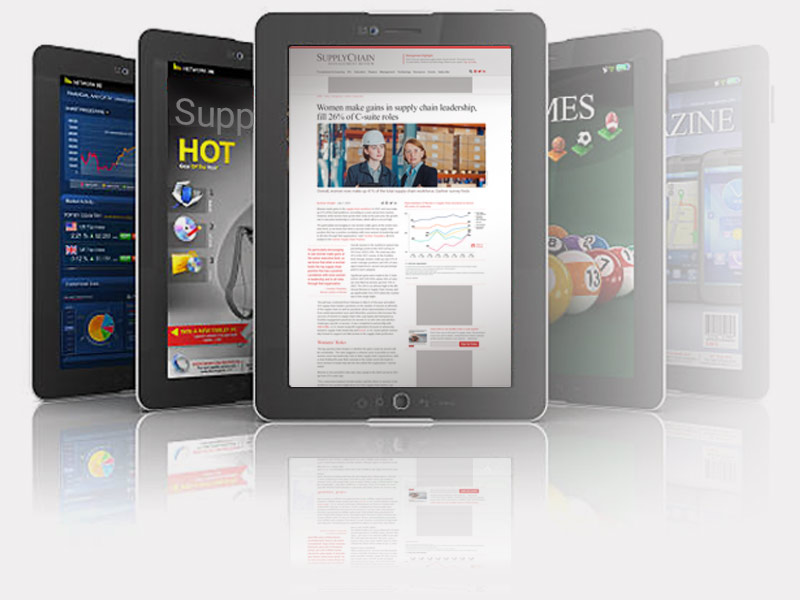
Editors’ Picks

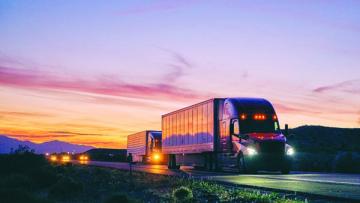

