Sorry, but your login has failed. Please recheck your login information and resubmit. If your subscription has expired, renew here.
July-August 2024
Artificial intelligence is everywhere these days. But what if it isn’t? I would guess that at least 50%, and probably closer to 70%, of the article pitches I receive these days involve AI. Most conversations I’ve had at conferences this year have at least touched on AI and its impact on the supply chain. Almost every technology company touts its AI-infused software. It seems that AI is not only mainstream, it’s Main Street. Browse this issue archive.Need Help? Contact customer service 847-559-7581 More options
Manufacturing remains a critical area of investment for many business leaders. In APQC’s 2024 Supply Chain Priorities and Challenges research, 72% of organizations named manufacturing as a priority for the year with regard to investing resources, innovation, and hiring.
This critical function is under increased pressure. Challenges related to geopolitical tensions, climate change, labor shortages, and cyberattacks continue to result in supply chain disruptions that affect manufacturing capabilities. In addition, supply chains experience risk on a smaller scale, such as disruptions for a particular supplier or a particular distribution channel.
With all these factors affecting the supply chain, it is important for manufacturing organizations to remain resilient so that they can both anticipate and mitigate the impact of disruptions. According to APQC’s research, organizations recognize disruptions as an area to focus on for manufacturing. However, the results are mixed regarding how organizations are building resilience in the face of potential disruptions.
SC
MR
Sorry, but your login has failed. Please recheck your login information and resubmit. If your subscription has expired, renew here.
July-August 2024
Artificial intelligence is everywhere these days. But what if it isn’t? I would guess that at least 50%, and probably closer to 70%, of the article pitches I receive these days involve AI. Most conversations I’ve… Browse this issue archive. Access your online digital edition. Download a PDF file of the July-August 2024 issue.Manufacturing remains a critical area of investment for many business leaders. In APQC’s 2024 Supply Chain Priorities and Challenges research, 72% of organizations named manufacturing as a priority for the year with regard to investing resources, innovation, and hiring.
This critical function is under increased pressure. Challenges related to geopolitical tensions, climate change, labor shortages, and cyberattacks continue to result in supply chain disruptions that affect manufacturing capabilities. In addition, supply chains experience risk on a smaller scale, such as disruptions for a particular supplier or a particular distribution channel.
With all these factors affecting the supply chain, it is important for manufacturing organizations to remain resilient so that they can both anticipate and mitigate the impact of disruptions. According to APQC’s research, organizations recognize disruptions as an area to focus on for manufacturing. However, the results are mixed regarding how organizations are building resilience in the face of potential disruptions.

An area of focus
APQC’s Supply Chain Priorities and Challenges research shows that managing disruptions is the top focus area for manufacturing in 2024 (Figure 1). Adaptability is key to this effort; organizations must build contingency plans for their production and shipping capabilities.
The second focus area for manufacturing is production management. This is an enabler of adaptability, as it requires solid processes and the ability to identify areas for change. It also requires data management that supports risk identification and mitigation.
The third area of focus identified in APQC’s research is automation and robotics. The adoption of technology can facilitate an organization’s preparedness for disruptions and boost its resiliency. This rapidly changing area of supply chain requires careful consideration to ensure the organization adopts technology that will best support its processes and business needs.
Key components of resilience
APQC also conducted research in collaboration with BCG to evaluate the range of supply chain resilience capabilities organizations need to thrive. The project involved surveying 185 companies, with quantitative data collected as well as information on practices related to establishing visibility and assessing risk.
One area examined in the research is organizations’ flexibility and transparency in manufacturing. The project defined flexibility to include the extent of network redundancy and whether an organization has a robust stockpile strategy. It defined transparency to include the visibility of an organization’s inventories, capacity, and supply forecasts.
Flexibility. Manufacturing flexibility has room for improvement within organizations. At the median, non-retail/wholesale organizations have only 25% of their revenue coming from products that could be manufactured at more than one plant. Similarly, at the median only 26% of retail and wholesale organizations’ total contract manufacturing spend comes from products that could be manufactured at a different facility.
These results indicate a large amount of risk assumed by these organizations. Should a trade route become inaccessible due to a natural disaster or political conflict, it may be difficult to get products out of a given facility. This can in turn lead to stockouts for products that cannot be manufactured at any other location, making a significant impact on an organization’s revenue, customer satisfaction, and reputation.
Industry plays a role when it comes to having a robust stockpile strategy for inventory. At the median, non-retail/wholesale organizations have 35% of their revenue come from raw materials or make-to-stock finished goods inventory with a robust stockpile strategy in place. Retail and wholesale organizations have a median of 50% of their revenue coming from inventory with a robust stockpile strategy.
The non-retail organizations are again putting themselves at risk by lacking a robust stockpile strategy. If a disruption leads to manufacturing delays, these organizations may have limited inventory on hand to fulfill orders. In an extended disruption, this again can lead to decreased revenue and a negative effect on reputation.
Transparency. Transparency has two components: visibility, or the ability to collect accurate information from all parts of the supply chain, and disclosure, or the ability to communicate this information both internally and externally. Transparency of capacity, inventories, and forecasts throughout the value chain is key to building resilience. As shown in Figure 2, most respondents among non-retail/wholesale organizations have at least some transparency for all of these items.

Two benefits of supply chain transparency are directly related to resilience: positive reputation and the ability to meet legal requirements. Reputation impacts an organization’s relationship with both its customers and its partners. Transparency can provide customers as well as regulators with visibility into the sourcing of parts and other materials that ultimately end up in a product. This provides peace of mind that the organization is able to ensure a consistent supply of materials without any legal issues.
For business partners, transparency can support their risk management. They can gain insight into the value chain, thus ensuring stability for their customers and partners. This is a shift in how supply chains have been run, as many companies have feared that revealing too much about their operations would undermine their advantage in their respective markets.
Another valuable aspect of transparency is the ability to meet legal requirements. Organizations face increased regulations regarding the source of materials for products and the ability to plan for potential disruptions. Having the ability to collect and disclose this information enables organizations to meet the requirements of these regulations.
How technology supports resilience
Many organizations have access to technology that supports transparency, as more supply chains embrace digitization. Although this technology implementation is not uniform across or even within organizations, it supports mature decision making as well as the adoption of specific automation systems in manufacturing.
Real-time manufacturing data. Gaining access to real-time production data enables a company to connect partners from across the supply chain to the manufacturing process. According to APQC’s data, 48% of respondents have access to real-time manufacturing data at specific facilities, and 8% have real-time data accessible throughout the enterprise.
Decision-making maturity. The decision-making maturity of an organization depends on the type and amount of data and analytics it possesses. Access to real-time manufacturing data enables an organization to make data-driven decisions, thus bolstering its resiliency. According to APQC’s research, only 42% of organizations are making decisions based on advanced analytics and predictive algorithms, the most mature capability an organization can have.
Automation systems. Figure 3 presents the most commonly implemented automation systems for organizations’ manufacturing. Each provides a benefit to an organization’s resilience. However, the fact that the most commonly implemented system has been adopted by only 57% of organizations indicates that many companies have room for growth.

The top two systems, predictive maintenance and autonomous machining, streamline manufacturing tasks and reduce the need for human intervention. Predictive maintenance allows organizations to optimize maintenance tasks in real time, accomplishing two goals of extending the life of equipment while minimizing disruptions to operations. Autonomous machining ensures that the manufacturing process occurs with minimal human involvement. It also supports real-time data analysis and decision-making, leading to increased efficiency in manufacturing and increased accuracy of supply chain data.
The next two systems, advanced planning and scheduling and advanced control and optimization, track and schedule production. Advanced planning and scheduling systems use algorithms to optimize demand, capacity, and production schedules. This not only results in more efficient production, but also more resilient production that can quickly adapt to unexpected changes. Advanced control and optimization uses software that tracks and regulates production stages. These tools yield higher productivity and cost savings for manufacturing.
Production-line simulation enables organizations to identify the potential effects of changes to their manufacturing systems, including production lines. They can model different scenarios with their manufacturing processes and use the results to make better informed decisions about how to address changes to production. Conducting these tests can bolster organizations’ resilience as it enables them to understand how mitigation steps can affect their production overall.
Use a phased approach to resiliency
About half of organizations identify managing supply chain disruptions as a top priority for manufacturing. To build resiliency against disruptions, organizations must incorporate flexibility and transparency into their supply chain operations. So far, organizations’ ability to build these traits has been mixed.
APQC recommends that organizations support their resilience by making real-time manufacturing data accessible throughout the enterprise, leveraging analytics and predictive algorithms when making decisions, and implementing a variety of automation systems in their manufacturing. They can accomplish all of these tasks through a phased approach.
The first step is to assess current capabilities and perform a risk assessment to identify potential threats. Based on the risk assessment, the next step is to develop a strategy that prioritizes the biggest risks and includes risk mitigation plans for each. The third step is to take action by addressing risks and building capabilities that create visibility into the end-to-end supply chain.
Although organizations can identify many points to address in their efforts to build resiliency, they do not need to act on all of them at once to gain a competitive advantage. They can continue to take a phased approach that addresses key risks and other potential weaknesses in the supply chain as they arise. •
About APQC
APQC helps organizations work smarter, faster, and with greater confidence. It is the world’s foremost authority in benchmarking, best practices, process and performance improvement, and knowledge management. APQC’s unique structure as a member-based nonprofit makes it a differentiator in the marketplace. APQC partners with more than 500 member organizations worldwide in all industries. With more than 40 years of experience, APQC remains the world’s leader in transforming organizations. Visit us at apqc.org and learn how you can make best practices your practices.
About the author
Marisa Brown is senior principal research lead, supply chain management, APQC. She can be reached at [email protected].
SC
MR

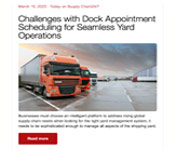
More Benchmarks
What's Related in Benchmarks

Explore
Topics
Procurement & Sourcing News
- Gen AI on Gartner’s Hype Cycle fast track to mainstream adoption
- Reglobalization drives the modern supply chain network
- Mapping the impact of geographic differences on global supply chain practices
- Join the Real Housewives of Supply Chain, change leaders in exclusive sessions at NextGen Supply Chain Conference
- Global footwear innovator taps 3PL expertise to boost U.S. presence
- Use value to drive organizational change
- More Procurement & Sourcing
Latest Procurement & Sourcing Resources
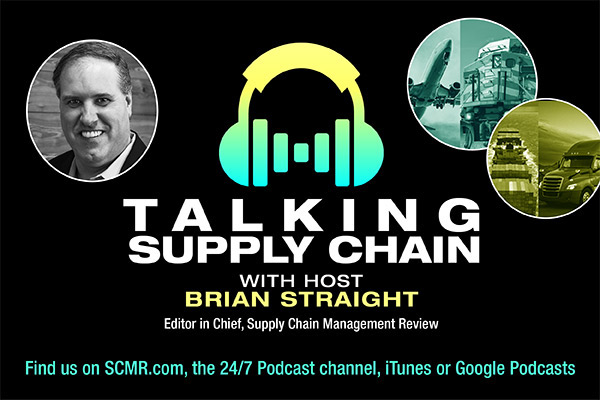
Subscribe
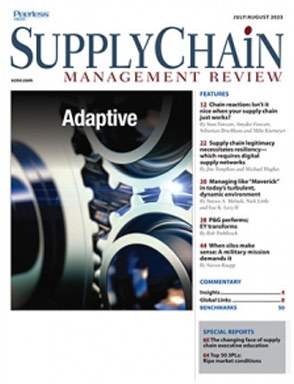
Supply Chain Management Review delivers the best industry content.
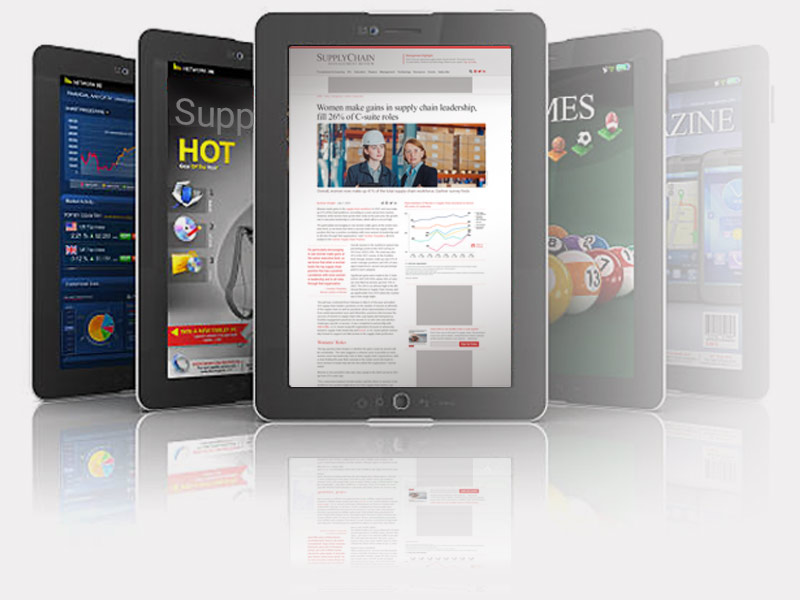
Editors’ Picks



