Sorry, but your login has failed. Please recheck your login information and resubmit. If your subscription has expired, renew here.
May-June 2015
As supply chain managers we are challenged year in and year out to figure out new, innovative ways to improve our operations. We have to translate educated guesses about what’s next into new investments in our processes. Such may be the case with robotics, 3D printing and additive manufacturing, and investments in new mobile technologies. However, successful planning, including planning for risk, resiliency, and flexibility, can help prepare you for whatever is next. Browse this issue archive.Need Help? Contact customer service 847-559-7581 More options
Superior supply chain planning requires excellent insight into customer demand for products and the availability of materials from suppliers. Many organizations look to data collected internally to better understand these factors, but others collaborate with external supply chain partners as well. Collaboration with customers and suppliers can provide organizations with valuable perspectives on the supply chain that can result in benefits for all involved.
To determine the extent to which external collaboration can benefit supply chain planning efforts, APQC looked at data from its Open Standards Benchmarking in supply chain planning.* Participating organizations provided the extent to which their sales and operations planning processes involve external demand collaboration with customers, and the extent to which these processes involve external supply planning collaboration with suppliers. APQC grouped organizations based on the degree to which they engage in each type of external collaboration. The data indicates that organizations with more collaboration with either of these external groups have more accurate forecasts and more efficient planning operations.
Working with Customers Means Getting More
The data indicates that organizations collaborating more with their customers to determine demand more accurately predict the needs of their businesses with fewer staff and for a similar cost as organizations that conduct less collaboration with their customers. Those organizations collaborating more with their customers from some to a very great extent have a lower average monthly national forecast error than organizations that only collaborate with their customers to little or no extent. Those with more collaboration have a median error of 5.2 percent, whereas organizations with less collaboration have a median error of 13 percent. Organizations are clearly seeing benefits from greater collaboration with their customers to better determine demand for products. By getting the customer perspective on the market, organizations are able to more accurately determine how much product they should produce and keep on hand.
![]() |
This complete article is available to subscribers
only. Click on Log In Now at the top of this article for full access. Or, Start your PLUS+ subscription for instant access. |
SC
MR
Sorry, but your login has failed. Please recheck your login information and resubmit. If your subscription has expired, renew here.
May-June 2015
As supply chain managers we are challenged year in and year out to figure out new, innovative ways to improve our operations. We have to translate educated guesses about what’s next into new investments in our… Browse this issue archive. Access your online digital edition. Download a PDF file of the May-June 2015 issue.
![]() |
Download Article PDF |
Superior supply chain planning requires excellent insight into customer demand for products and the availability of materials from suppliers. Many organizations look to data collected internally to better understand these factors, but others collaborate with external supply chain partners as well. Collaboration with customers and suppliers can provide organizations with valuable perspectives on the supply chain that can result in benefits for all involved.
To determine the extent to which external collaboration can benefit supply chain planning efforts, APQC looked at data from its Open Standards Benchmarking in supply chain planning.* Participating organizations provided the extent to which their sales and operations planning processes involve external demand collaboration with customers, and the extent to which these processes involve external supply planning collaboration with suppliers. APQC grouped organizations based on the degree to which they engage in each type of external collaboration. The data indicates that organizations with more collaboration with either of these external groups have more accurate forecasts and more efficient planning operations.
Working with Customers Means Getting More
The data indicates that organizations collaborating more with their customers to determine demand more accurately predict the needs of their businesses with fewer staff and for a similar cost as organizations that conduct less collaboration with their customers. Those organizations collaborating more with their customers from some to a very great extent have a lower average monthly national forecast error than organizations that only collaborate with their customers to little or no extent. Those with more collaboration have a median error of 5.2 percent, whereas organizations with less collaboration have a median error of 13 percent. Organizations are clearly seeing benefits from greater collaboration with their customers to better determine demand for products. By getting the customer perspective on the market, organizations are able to more accurately determine how much product they should produce and keep on hand.
![]() |
SUBSCRIBERS: Click here to download PDF of the full article. |
SC
MR
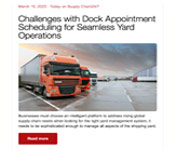
Latest Supply Chain News
Latest Podcast
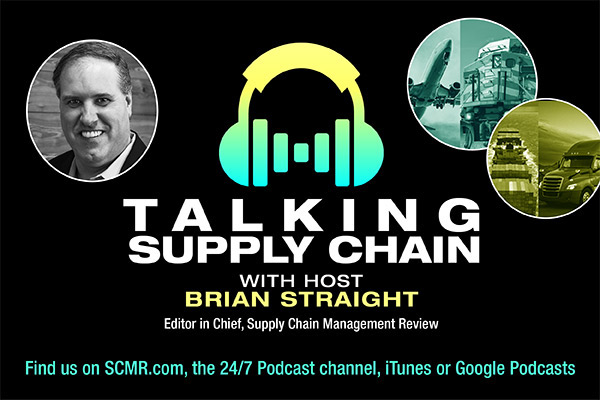
Explore
Topics
Latest Supply Chain News
- 2024 Warehouse/DC Operations Survey: Technology adoption on the rise
- Benchmarking the complexity of ESG reporting
- Looking back at NextGen 2024
- The Corporate Sustainability Due Diligence Directive
- How to make your CFO a supply chain superfan
- AI is moving omnichannel closer to the customer
- More latest news
Latest Resources
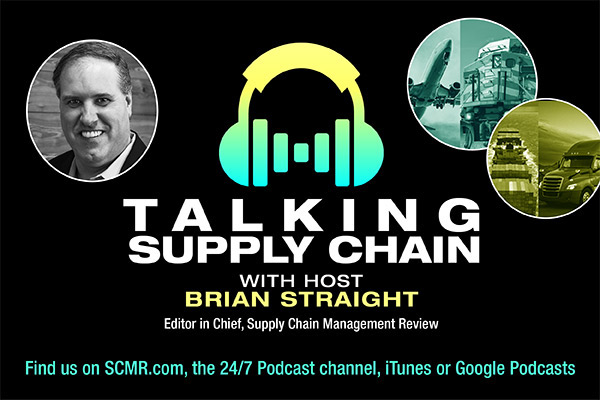
Subscribe
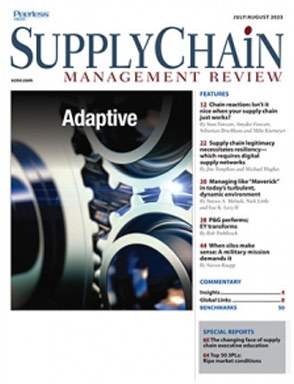
Supply Chain Management Review delivers the best industry content.
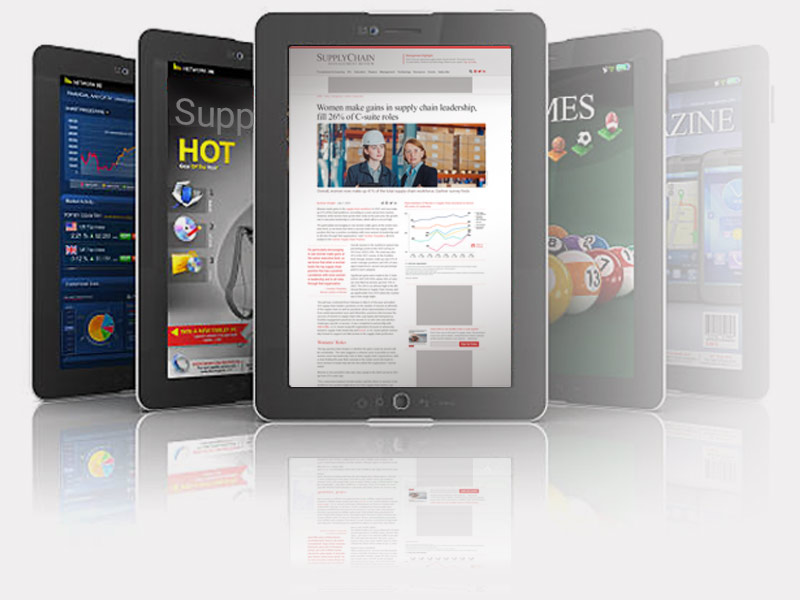
Editors’ Picks



