Sorry, but your login has failed. Please recheck your login information and resubmit. If your subscription has expired, renew here.
September-October 2014
2014 marks the 10 year anniversary of the Gartner Supply Chain Top 25 ranking. This year we have a diverse set of large, global companies with mature, demand-driven supply chains. There are lessons to be learned from these supply chain leaders, many of whom have led their industries over the past decade. Browse this issue archive.Need Help? Contact customer service 847-559-7581 More options
While conventional supply chains seek to efficiently move products in a linear fashion from raw materials to end consumers, a “circular” or “closed-loop” supply chain is one that is also dependent on feeding used products back as raw materials. The resulting circular supply chain poses unique challenges and opportunities for supply chain professionals.
Successfully building and managing such a system requires new and unconventional thinking. That’s what the Milwaukee, Wisc.-based global manufacturer Johnson Controls has done to incorporate automotive battery recycling into its business
Distinguishing Features
There are plenty of economic incentives for re-thinking the auto battery supply chain. As much as 80 percent of the materials used to make auto batteries can be derived from recycled batteries. The metals, plastics, and acid used to make conventional auto batteries can all be recycled. This creates a significant business benefit by minimizing the impact of price volatility of these commodities and providing raw materials at a more competitive cost. Moreover, automotive batteries contain hazardous materials. The best and most responsible form of minimizing the health and environmental risks is to recycle them.
![]() |
This complete article is available to subscribers
only. Click on Log In Now at the top of this article for full access. Or, Start your PLUS+ subscription for instant access. |
Not ready to subscribe, but need this article?
Buy the complete article now. Only $20.00. Instant PDF Download.
Access the complete issue of Supply Chain Management Review magazine featuring
this article including every word, chart and table exactly as it appeared in the magazine.
SC
MR
Sorry, but your login has failed. Please recheck your login information and resubmit. If your subscription has expired, renew here.
September-October 2014
2014 marks the 10 year anniversary of the Gartner Supply Chain Top 25 ranking. This year we have a diverse set of large, global companies with mature, demand-driven supply chains. There are lessons to be… Browse this issue archive. Access your online digital edition. Download a PDF file of the September-October 2014 issue.![]() |
Download Article PDF |
While conventional supply chains seek to efficiently move products in a linear fashion from raw materials to end consumers, a “circular” or “closed-loop” supply chain is one that is also dependent on feeding used products back as raw materials. The resulting circular supply chain poses unique challenges and opportunities for supply chain professionals.
Successfully building and managing such a system requires new and unconventional thinking. That’s what the Milwaukee, Wisc.-based global manufacturer Johnson Controls has done to incorporate automotive battery recycling into its business
Distinguishing Features
There are plenty of economic incentives for re-thinking the auto battery supply chain. As much as 80 percent of the materials used to make auto batteries can be derived from recycled batteries. The metals, plastics, and acid used to make conventional auto batteries can all be recycled. This creates a significant business benefit by minimizing the impact of price volatility of these commodities and providing raw materials at a more competitive cost. Moreover, automotive batteries contain hazardous materials. The best and most responsible form of minimizing the health and environmental risks is to recycle them.
![]() |
SUBSCRIBERS: Click here to download PDF of the full article. |
SC
MR
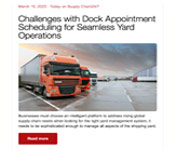
Latest Supply Chain News
Latest Podcast
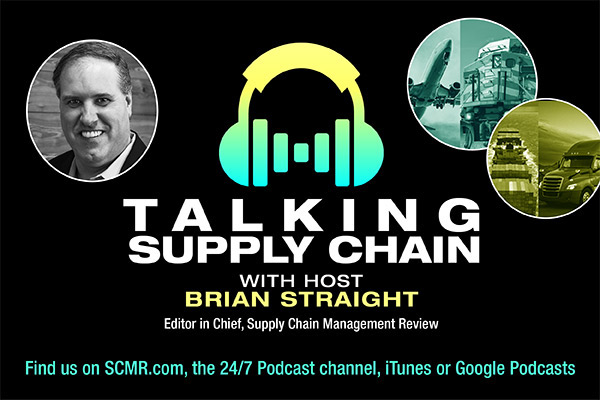
Explore
Latest Supply Chain News
- 2024 Warehouse/DC Operations Survey: Technology adoption on the rise
- Benchmarking the complexity of ESG reporting
- Looking back at NextGen 2024
- The Corporate Sustainability Due Diligence Directive
- How to make your CFO a supply chain superfan
- AI is moving omnichannel closer to the customer
- More latest news
Latest Resources
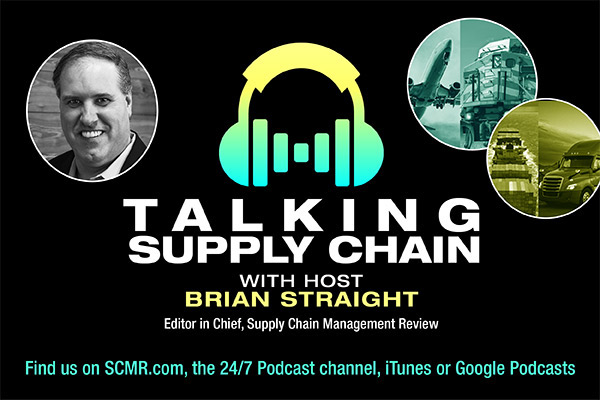
Subscribe
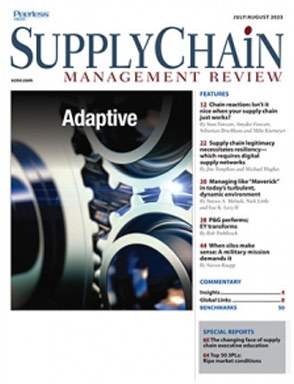
Supply Chain Management Review delivers the best industry content.
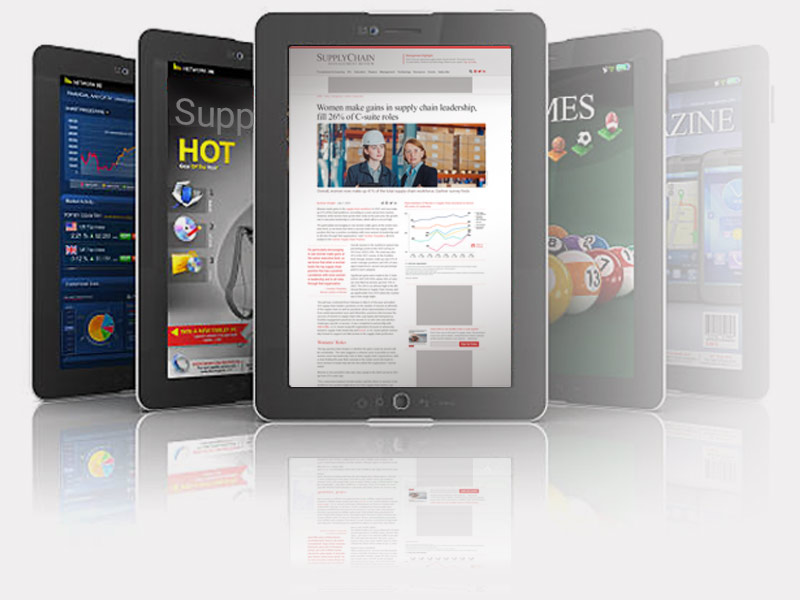
Editors’ Picks



