Sorry, but your login has failed. Please recheck your login information and resubmit. If your subscription has expired, renew here.
May-June 2014
Getting the most from Sales and Operations Planning is a combination of people, processes, and technology. The Red Wing Shoe Company details the steps it took to improve S&OP processes, slash its S&OP planning efforts by 50 percent, and align manufacturing with sales—all while growing its business. Browse this issue archive.Need Help? Contact customer service 847-559-7581 More options
To streamline their deliveries to customers, many organizations have adopted continuous replenishment programs. By monitoring customer inventories and automatically replacing used materials when needed, these organizations have also taken steps to improve their operations by eliminating the need for purchase orders and other related paperwork. Continuous replenishment programs offer the additional potential to create close relationships with customers that can increase customer loyalty.
According to APQC’s Open Standards Benchmarking in logistics, only a slight majority (57 percent) of participating organizations have implemented continuous replenishment programs for their customers. Of this group, 27 percent have extensively implemented these programs. To determine whether these programs offer the potential for superior logistics performance, APQC compared the logistics performance of organizations that have adopted these programs against that of organizations that have not adopted continuous replenishment. The data indicates that the two groups have similar inventory carrying costs, but that organizations with continuous replenishment programs need fewer full-time equivalent employees (FTEs) in logistics, have a higher perfect order performance rate, and ship a greater amount of their sales orders as part of full-load shipments.
Inventory and Staffing Needs
APQC’s data indicates a similar inventory carrying cost for organizations that have and have not implemented continuous replenishment programs. At the median, organizations that provide these programs for their customers have a 4 percent inventory carrying cost as a percentage of their average inventory value. Organizations that have not implemented these programs have an inventory carrying cost of 4.2 percent of their average inventory value.
![]() |
This complete article is available to subscribers
only. Click on Log In Now at the top of this article for full access. Or, Start your PLUS+ subscription for instant access. |
Not ready to subscribe, but need this article?
Buy the complete article now. Only $20.00. Instant PDF Download.
Access the complete issue of Supply Chain Management Review magazine featuring
this article including every word, chart and table exactly as it appeared in the magazine.
SC
MR
Sorry, but your login has failed. Please recheck your login information and resubmit. If your subscription has expired, renew here.
May-June 2014
Getting the most from Sales and Operations Planning is a combination of people, processes, and technology. The Red Wing Shoe Company details the steps it took to improve S&OP processes, slash its S&OP planning… Browse this issue archive. Access your online digital edition. Download a PDF file of the May-June 2014 issue.
![]() |
Download Article PDF |
To streamline their deliveries to customers, many organizations have adopted continuous replenishment programs. By monitoring customer inventories and automatically replacing used materials when needed, these organizations have also taken steps to improve their operations by eliminating the need for purchase orders and other related paperwork. Continuous replenishment programs offer the additional potential to create close relationships with customers that can increase customer loyalty.
According to APQC’s Open Standards Benchmarking in logistics, only a slight majority (57 percent) of participating organizations have implemented continuous replenishment programs for their customers. Of this group, 27 percent have extensively implemented these programs. To determine whether these programs offer the potential for superior logistics performance, APQC compared the logistics performance of organizations that have adopted these programs against that of organizations that have not adopted continuous replenishment. The data indicates that the two groups have similar inventory carrying costs, but that organizations with continuous replenishment programs need fewer full-time equivalent employees (FTEs) in logistics, have a higher perfect order performance rate, and ship a greater amount of their sales orders as part of full-load shipments.
Inventory and Staffing Needs
APQC’s data indicates a similar inventory carrying cost for organizations that have and have not implemented continuous replenishment programs. At the median, organizations that provide these programs for their customers have a 4 percent inventory carrying cost as a percentage of their average inventory value. Organizations that have not implemented these programs have an inventory carrying cost of 4.2 percent of their average inventory value.
![]() |
SUBSCRIBERS: Click here to download PDF of the full article. |
SC
MR
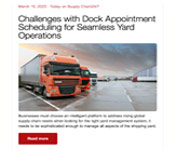
Latest Supply Chain News
- Tariffs, taxes and trade: The impact of Trump’s reelection on the supply chain
- How to improve demand forecasts for new product families
- Services sector sees growth in October, reports ISM
- Balanced supply chain management Part 4: The key—leading beyond the silo
- Managing inbound freight: What has changed in two decades?
- More News
Latest Podcast
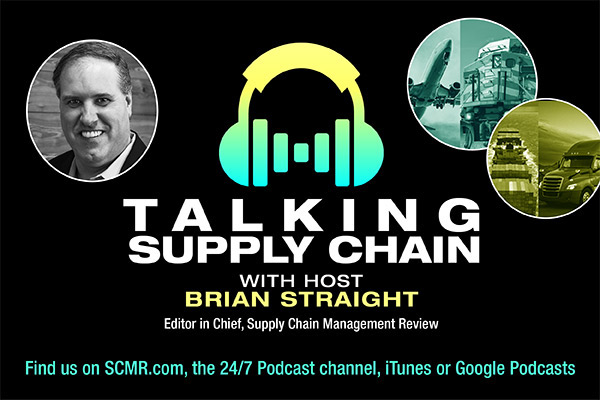
Explore
Latest Supply Chain News
- Tariffs, taxes and trade: The impact of Trump’s reelection on the supply chain
- How to improve demand forecasts for new product families
- Services sector sees growth in October, reports ISM
- Balanced supply chain management Part 4: The key—leading beyond the silo
- Managing inbound freight: What has changed in two decades?
- Inbound freight: Often a missed opportunity
- More latest news
Latest Resources
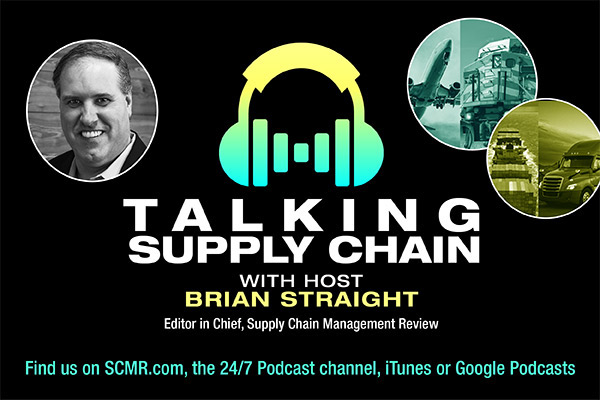
Subscribe
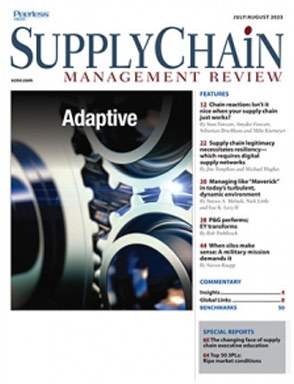
Supply Chain Management Review delivers the best industry content.
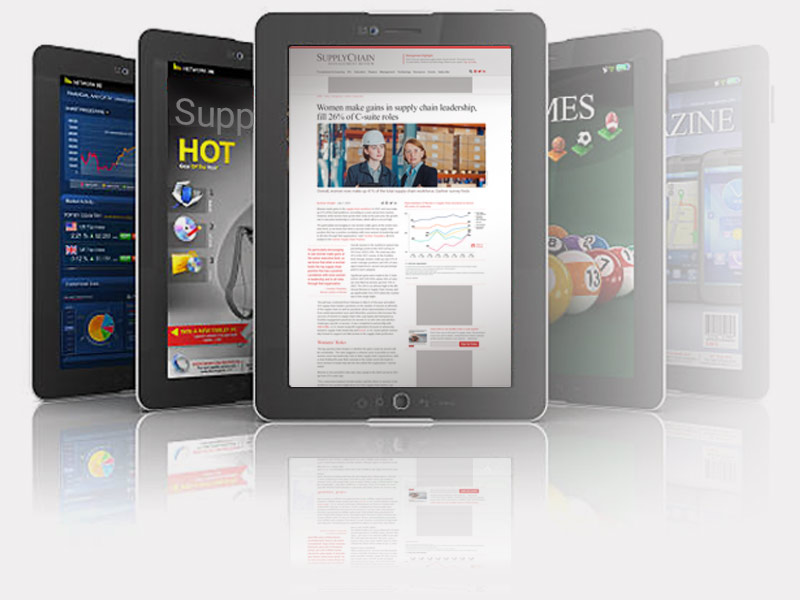
Editors’ Picks



