After a 20-year plus career in supply chain and operations management, there is still one thing that I see very little written about in most journals and publications. Culture. I’m not sure why, but it would appear, at least from the outset, that with the very significant developments in technology and productivity tracking, the reasons for developing culture appear less pressing. The actual opposite is true.
In my early days as a senior operations supervisor, we removed large portions of entire shifts from the floor to do what we called “Culture Training.”
Led by supervisors and managers, we walked team members through various role plays and real-life scenarios that mirrored their daily challenges of dealing with our internal and external customers. Above all else the focus was respect, empathy and consideration for others with an overriding theme of integrity and sincerity.
Attendees were broken into competitive groups that remained intact for the entire day of the program. They were awarded a certificate at the end of the program, and a group picture was displayed in the warehouse foyer celebrating their achievement. Lunch was also provided for the group during their training day. The time was filled with videos and activities that challenged groups to think, reflect and share with each other.
The director of operations not only signed everyone’s certificates, but would visit the session during the day, shake participants hands and briefly address the group about their value to the company. Part of my duties as a “Culture Trainer” was to foster the culture that had been established and clarified in these sessions, and to teach my peers to do the same.
Sounds almost too good to be true. Right? Yes, perhaps it was, but what it did was send a very clear and concise message to all about the value of cooperation, honest communication and teamwork.
The value of people
This program lasted for about 3 years. Then, as production volumes and expectations quickly grew, the ability to carve out this valuable time became less and less viable. It was impossible to budget. There was certainly no visible, trackable KPI. The value was long term at best, but what became just as obvious was its absence. We experienced an increase in discipline-related issues involving behavior, language and attendance. Overall people just seemed not to care as much about their jobs.
For a while, at the beginning we all liked who we worked for, what we did and who we worked with. It was the definition of a great job. The program was never reinstated. It was replaced with posters filled with catchy slogans that covered the cafeteria walls and the foyer. But they were rarely read and ever more rarely followed.
I believe there is a lesson there for supply chain managers. Regardless of your size or capability, your supply chain success will ultimately rely on the people who run it. Were they hired for character or skill? We all know that you can virtually train anyone to perform a skill but it is another thing entirely to teach them to care.
The value of people and how we treat them is probably far more important now than it has ever been. It was not too long ago that we talked to each other rather than texting, emailing or sending a tweet. As global supply chains increasingly focus on AI, robotics and other emerging technologies that involve less human interaction, it is perhaps prudent to keep in mind the meaning of such words as sincerity. I hope we all work “without wax.”
Fred Demers is a Consulting Supply Chain and Logistics Professional. He and can be reached by email at [email protected].
SC
MR
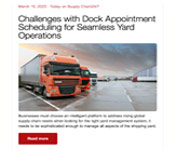
Latest Supply Chain News
Latest Podcast
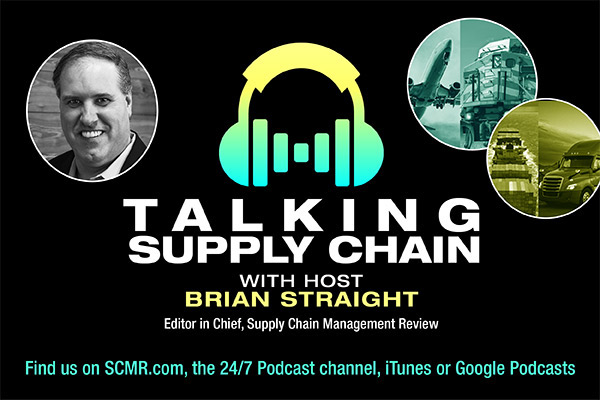
Explore
Latest Supply Chain News
- 2024 Warehouse/DC Operations Survey: Technology adoption on the rise
- Benchmarking the complexity of ESG reporting
- Looking back at NextGen 2024
- The Corporate Sustainability Due Diligence Directive
- How to make your CFO a supply chain superfan
- AI is moving omnichannel closer to the customer
- More latest news
Latest Resources
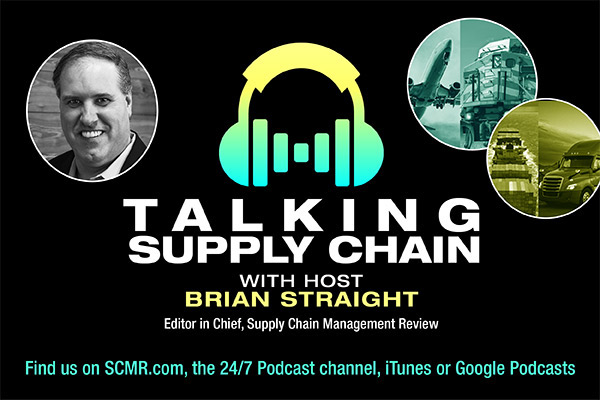
Subscribe
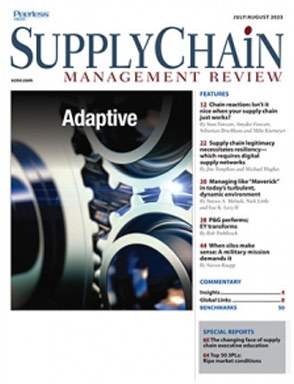
Supply Chain Management Review delivers the best industry content.
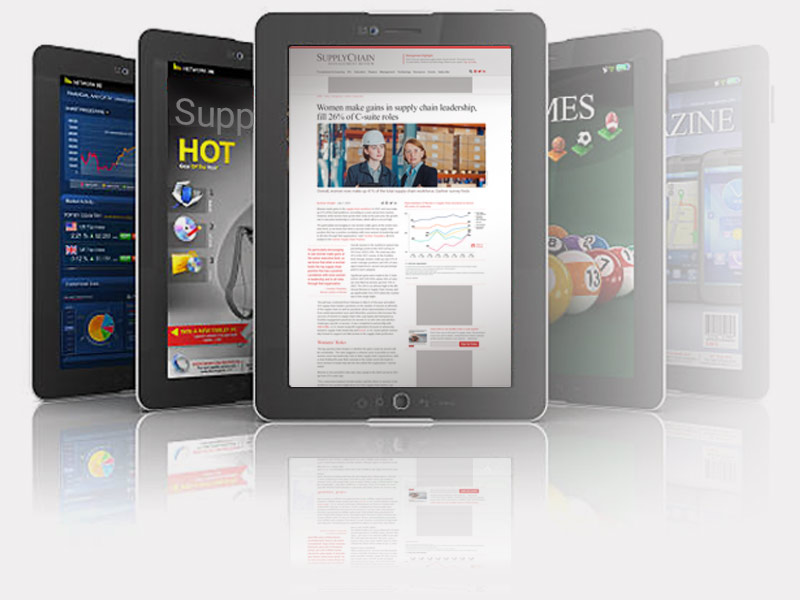
Editors’ Picks



