Sorry, but your login has failed. Please recheck your login information and resubmit. If your subscription has expired, renew here.
May-Jun 2024
In each issue I try to leave you with some of my limited knowledge in this space. Or at least give you something to think about. I think it is our job at Supply Chain Management Review to -- hopefully -- leave you with at least one bit of knowledge from each article inside our issues. This time, though, I'm going to leave you with the secret to learn more than one thing: Sign up to attend the NextGen Supply Chain Conference in October. Browse this issue archive.Need Help? Contact customer service 847-559-7581 More options
Automating complex warehouse operations can be a formidable challenge that requires deep technical and operational expertise and an awareness of the unique problems involved.
The MIT Center for Transportation & Logistics and global logistics company Maersk organized a roundtable of industry professionals to explore the challenges of warehouse automation. This article is based on highlights from the discussions and the authors’ experience and research.
The mix of challenges companies face when automating warehouse facilities differs with each application. However, some challenges are common to many projects. Here are some key examples.
SC
MR
Sorry, but your login has failed. Please recheck your login information and resubmit. If your subscription has expired, renew here.
May-Jun 2024
In each issue I try to leave you with some of my limited knowledge in this space. Or at least give you something to think about. I think it is our job at Supply Chain Management Review to -- hopefully -- leave you… Browse this issue archive. Access your online digital edition. Download a PDF file of the May-Jun 2024 issue.Automating complex warehouse operations can be a formidable challenge that requires deep technical and operational expertise and an awareness of the unique problems involved.
The MIT Center for Transportation & Logistics and global logistics company Maersk organized a roundtable of industry professionals to explore the challenges of warehouse automation. This article is based on highlights from the discussions and the authors’ experience and research.
Automation demands
The mix of challenges companies face when automating warehouse facilities differs with each application. However, some challenges are common to many projects. Here are some key examples.
Flexibility. The need for flexibility when evaluating new automation is increasingly important. However, different interpretations exist for flexibility. It can mean a solution’s ability to adjust operations as demand and business needs fluctuate. It may also refer to a system’s capacity to handle different loads, including various SKU sizes and packaging types.
Maersk has adopted a flexible approach to retrofitting its legacy warehouses. A notable example is the use of drones to improve inventory management in traditional facilities, allowing more efficient and accurate checks. A different robot solution from warehouse automation company BionicHive is being installed in traditional racking systems to lift and transport goods across the warehouse without using additional floor space. Maersk also partnered with fulfillment specialist Fabric to install a flexible, high-density-storage micro-fulfillment center (MFC) that automates some or all of an existing warehouse’s operations. This MFC can be scaled up later as demand increases.
Fulfillment speed. Fulfillment speed was another factor that roundtable participants considered critical, as e-commerce requires short lead times. Warehouses are under immense pressure to deliver orders quickly and efficiently, and automation is a pivotal tool to help expedite the order fulfillment process and enhance customer satisfaction.
Order fulfillment automation is nothing new; what is new is the unprecedented speed at which some orders are now being picked and packed. Ocado’s grid solution, for instance, is a state-of-the-art cube storage system for online grocery fulfillment that can put together an order of 50 items in just five minutes. A human worker takes more than 10 times longer to complete such a task. The solution uses thousands of robots that travel over a grid system, picking and packing grocery orders. It is being implemented by multiple grocery chains across the globe, including
U.S.-based Kroger and Morrisons in the UK.
Interoperability. Effectively integrating new automation technologies into warehouse operations is a challenge faced by many companies. As a result, interoperability—the ability of automated systems to work with existing warehouse systems—is increasingly important.
However, as more companies look to tailor warehouse automation, the number of startups developing unique technologies that can solve specific challenges has grown exponentially. The designs of these various solutions are based on diverse platforms, standards, or protocols, using many interconnected elements. Consequently, warehouse systems have become more complex and prone to errors. A failure or bug in one part of the system can have a cascading effect, leading to widespread operational issues. Moreover, multiple solutions make it harder to maintain, upgrade, and adapt the integrated system over time. Companies must deal with various vendors with differing support, maintenance, and upgrade policies. Multiple automation solutions require distinct operational and maintenance skill sets, increasing the system’s complexity and requiring “layers of support” (Gooley, 2023).
To address challenges like these, companies need to find and train staff to manage a multi-solution environment, which can be both time-consuming and costly.
Spoiled for choice. In this complex environment, warehouse managers face the challenge of selecting the right automation technologies that align with their warehouse’s specific requirements.
The proliferation of solutions and technology suppliers is making it harder for practitioners to keep pace with technological developments. Also, increasing solution diversity lengthens the time required to analyze each application. When evaluating their options, practitioners must weigh many factors, like facility layout, order profiles, demand patterns, and time to implement. Another complication is the investments required to automate facilities. While automation usually offers long-term benefits, the initial capital expenditure (CAPEX) can be substantial. Companies that are considering automation solutions need to assess the ROI involved and the long-term cost savings that each automation initiative can provide when selecting the best solution.
Evaluating winning solutions
To meet challenges like the ones described above as the field of warehouse automation continues its rapid advance, choosing the right solutions is of crucial importance.
As a global company with numerous facilities and thousands of customers around the world, Maersk follows a structured and comprehensive approach to evaluating and implementing new warehouse technologies. This thorough, methodical approach ensures that solutions are selected and implemented strategically to deliver maximum operational efficiency and customer satisfaction.
Here are the four main stages of this proven process.
- Assess the solution’s business impact. The technologies involved need to resolve a major customer pain point as well as an internal one. A “Gemba walk” follows this initial assessment to observe firsthand the issue in the warehouse that the technology could solve.
- Use Multi-Criteria Analysis (MCA) to compare potential solutions. MCA assesses the value of solving the issue with a particular solution. The primary criteria are safety, throughput improvement (mainly during peak times) and cost efficiency. Technologies that score highest on these criteria advance to the proof of concept (PoC) stage.
- Develop a PoC. This stage encompasses studying, designing, testing, and physically executing the solution. The time required can differ, ranging from a few weeks to several years, depending on whether the technology is new or already established. The process favors scenario analysis based on success probabilities rather than running simulations, which are often complex and laden with assumptions.
- Pilot the solution. Finally, having achieved a successful PoC, Maersk chooses a warehouse to carry out the pilot based on several factors. For example, the local team in the warehouse must possess the right mindset for piloting and improving the technology. Another factor is whether the facility is conducive to scaling, which allows the team to observe the solution’s full deployment and immediate results. Strong support from vendors and customers in the warehouse is vital for effective implementation and feedback.
Putting talent to work
Finally, a piece of the warehouse automation puzzle that is of supreme importance is harnessing the ideas and creativity of employees who are on the front lines of the company’s logistics and supply chain operations. Identifying and nurturing teams with the right knowledge and skills is particularly important. The Maersk Innovation Center plays a crucial role in meeting these goals.
Maersk’s partnership with MIT CTL is a significant part of the Center. This collaboration has created a tailored program for training individuals from various departments within Maersk, particularly in areas crucial to supply chain innovation. Besides classroom instruction, participants visit robotics companies and gain firsthand insights into the industry’s cutting-edge advancements. Modeled after the “Shark Tank” concept, the culmination of the program is a unique competitive event where participants present their innovative ideas to Maersk executives via a five-minute pitch. Maersk executives recognize the most promising proposals and may develop them into PoCs.
The program has trained more than 75 innovation leaders in two years. These individuals have become ambassadors of innovation within Maersk, demonstrating the company’s commitment to fostering talent and driving forward-thinking solutions in the logistics sector.
For more insights into warehouse automation, see the authors’ whitepaper, The Warehouse of the Future: Toward Highly Automated, Interconnected, Sustainable Warehouses at https://ctl.mit.edu/pub/report/warehouse-future. •
SC
MR

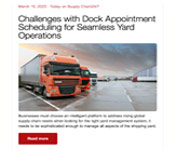
More Warehouse Automation
Explore
Topics
Software & Technology News
- Nine questions are the key to AI success in building resilient supply chains
- Looking back at NextGen 2024
- AI is moving omnichannel closer to the customer
- How technological innovation is paving the way for a carbon-free future in logistics and supply chains
- Körber Supply Chain Software’s Craig Moore says MercuryGate acquisition is about the customer
- Robotic use grows by 10%
- More Software & Technology
Latest Software & Technology Resources
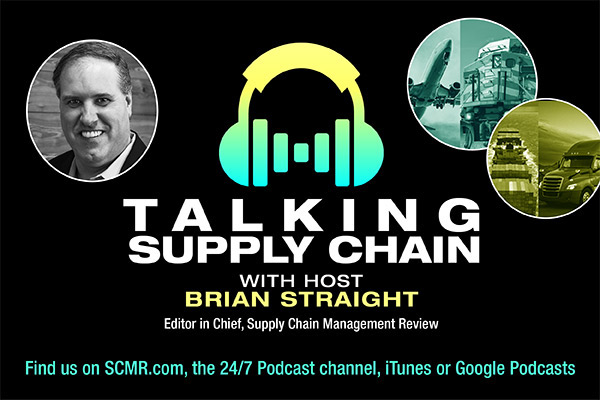
Subscribe
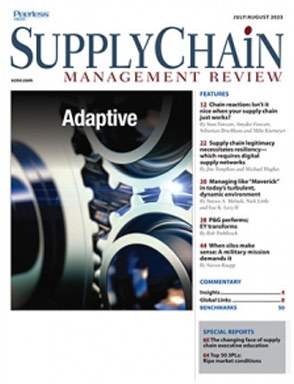
Supply Chain Management Review delivers the best industry content.
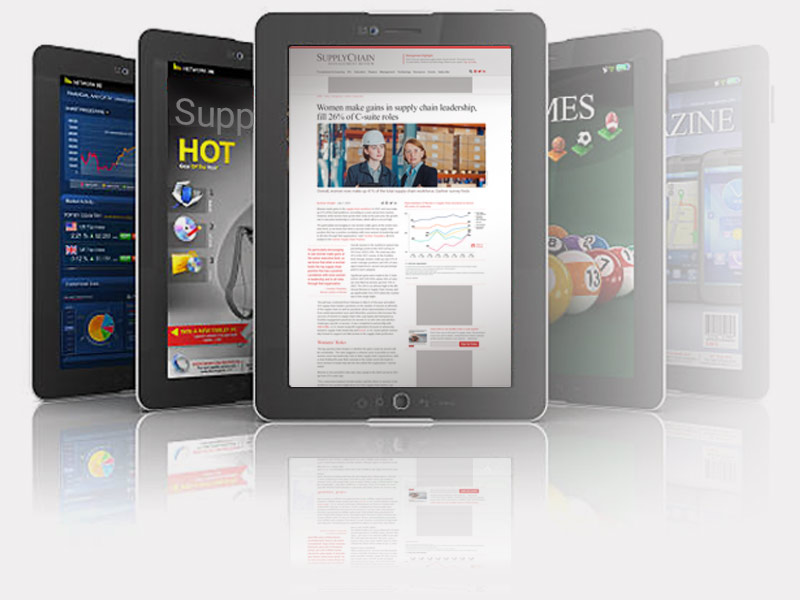
Editors’ Picks

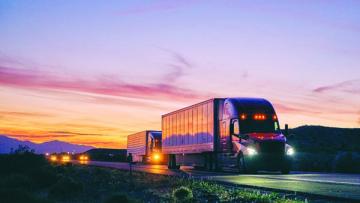

