The materials handling industry has been undergoing a transition from a focus on hardware – speeds and feeds – to an emphasis on the software that the directs the equipment for some time. The transition has been driven by a couple of factors, in my view.
One is physics: No matter how good the motors, drives and gear systems, there’s a limit to the speed at which conveyors, sorters and automated storage systems can safely operate. Software, on the other hand, allows those systems to be more efficient and effective at normal speeds. Sorters, for instance, can sort with less gap space between cartons and parcel packages..
Another is managing complexity: There are just too many SKUs, too many value-added services and too many variations in orders – too many decisions - for people to manage.
The last is the emergence of maintenance as a best practice in warehousing. MRO, and MRO-related software, are long established in manufacturing, where the uptime of automated manufacturing systems is critical. We’re now experiencing that same criticality in warehousing and distribution.
The common denominator in all three examples is the need to operate smart rather than just fast. That’s software.
Based on a conversation I had the other day as part of Day 2 of this year’s MHLC with Hamid R. Montazeri, Dematic’s senior vice president of software and digital solutions development, I think we’re on the cusp of the next generation of warehouse software. This is a case where on-premises and cloud software work together to get the job done. More on this in a minute.
Montazeri and I began talking in general about some of the things he’s seeing at Dematic, as a result of talking to customers as well as his own product managers. The topic here was maintenance software. In that space, a lot of the talk is about predictive maintenance. That’s the ability of equipment management system being able to predict a maintenance event in advance of a breakdown based on real-time operating systems. When we get there, maintenance organizations will be able to move away from performing maintenance at prescribed times to more pinpoint servicing of equipment.
That’s where we are going, but that’s not where we are yet. The first step is to put sensors on various parts of a system – either new equipment going out the door or retrofitted onto existing systems – to gather IoT data. That data, in turn, can go to a data lake where it can be analyzed by machine learning algorithms to do the predictive analysis.
Predictive analytics requires data, and lots of it. “The world of predictive maintenance is 10% algorithms and 90% data,” Montazeri said. “That kind of detailed data isn’t commonly available right now in intralogistics.” To get there, he noted, we first have to get more sensors on our systems. That’s happening now, primarily with newly installed equipment. But it’ll still be some time before we’ve collected enough data, and have enough history, to make meaningful predictions. In the interim, there is real-time condition monitoring, which Dematic is doing now.
Montazeri described that as “a stepping-stone to get to predictive maintenance.” He added: “If you have real-time data, you can compare the signals coming off your equipment to see if they are outside normal characteristics, which alerts you to a potential problem. We can provide that to our customers now, based on real-time and limited data.”
From there, we talked about what Montazeri called an emerging architecture that “combines the world of Cloud and on premises software.” Rather than an either/or situation – your software is either on premises or in the cloud – it’s a hybrid approach that combines Edge computing – or what Montazeri called the Intelligent Edge that puts computing power on premises where the work is being done and there is no room for latency – and Cloud computing – where you can harness storage for data lakes and computing power to crunch a lot of numbers.
“When you take computing to the cloud, there’s a latency added to the time it takes for an equipment action given the time associated with transmission of signals,” Montazeri said. “We’re getting to a point, however, where you can do a lot of calculations cheaply onsite, which is the Intelligent Edge, and combine that with the storage and computing power you have in the Cloud. It can also open the door for creating a software eco-system.”
Montazeri believes this combination could be a transformative step for intralogistics software. It is certainly a different way to think of software systems inside warehouses and distribution centers, and may point the way to the next generation of solutions.
SC
MR
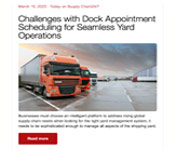
More Software
- Looking back at NextGen 2024
- AI is moving omnichannel closer to the customer
- How technological innovation is paving the way for a carbon-free future in logistics and supply chains
- Körber Supply Chain Software’s Craig Moore says MercuryGate acquisition is about the customer
- Harnessing Edge Computing and AI Vision Systems for Real-Time Logistics Insights
- The art of winning at supply chain technology: Lessons from managing tech for the largest private trucking fleet in the U.S.
- More Software
Latest Podcast
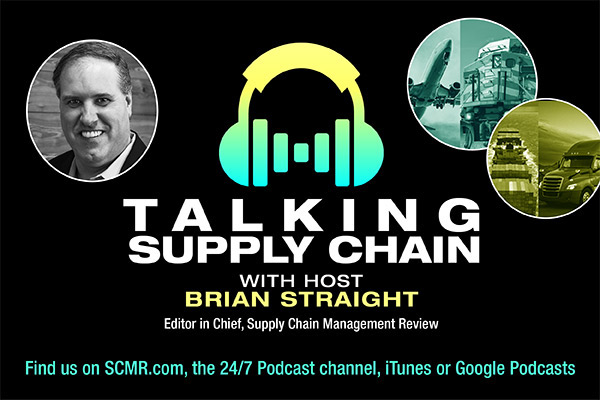
Explore
Software & Technology News
- Nine questions are the key to AI success in building resilient supply chains
- Looking back at NextGen 2024
- AI is moving omnichannel closer to the customer
- How technological innovation is paving the way for a carbon-free future in logistics and supply chains
- Körber Supply Chain Software’s Craig Moore says MercuryGate acquisition is about the customer
- Robotic use grows by 10%
- More Software & Technology
Latest Software & Technology Resources

Subscribe
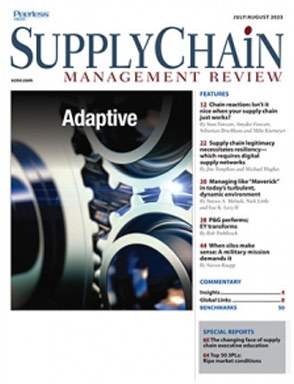
Supply Chain Management Review delivers the best industry content.
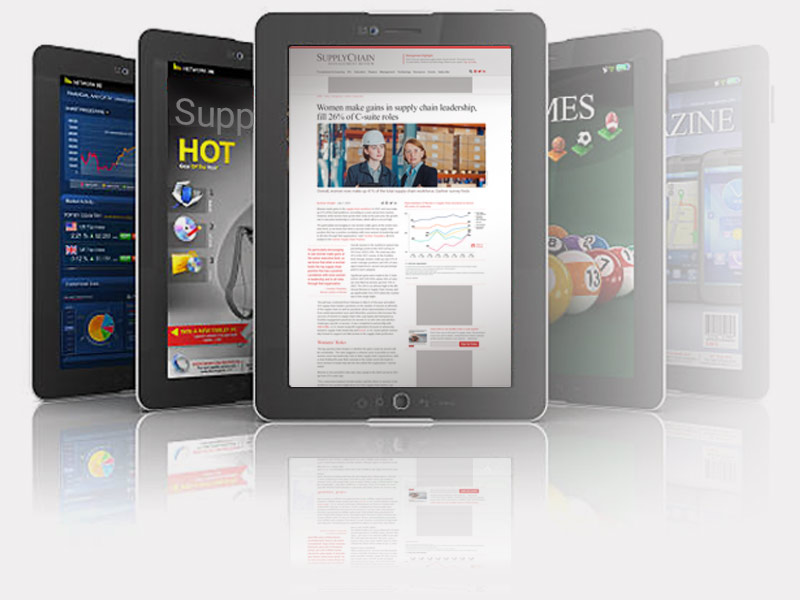
Editors’ Picks



