Sometimes the NextGen Supply Chain is already in warehouses and distribution centers, but is completely overlooked. It's easy to do with so much emphasis on filling today's orders or getting through the current season and onto the next. What's not so easy is playing catchup when your competitor is already making gains with advanced technology and you're not. Worse yet, it's already happening in some unexpected places.
For instance, there are many people who think virtual reality (VR) is much better suited today to the living room than to the supply chain. Not so, says Dave Norton, vice president of corporate quality and customer care at The Raymond Corporation.
And he's not alone in that assessment. Raymond demonstrated its Virtual Reality Simulator for lift truck operator instruction in the HTC Vive booth at last month's Consumer Electronics Show in Las Vegas.
In fact, VR fits in quite well as an enhancement to the three OSHA-mandated training steps – classroom instruction, on-vehicle training and an exam.
The system uses an HTC Vive VR headset that connects to the truck. The student wears the goggles and is walked through several training modules including: basic operating, interacting with pallets, steering and controls. Meanwhile, the trainer, along with other students, can see on a monitor all that the student sees through the goggles, aiding instruction.
Norton cites several advantages to using VR in operator instruction. He says it helps build trainee confidence prior to driving the truck. It also allows experiential learning in alternative scenarios. And VR streamlines the process of getting new drivers up and running.
Raymond is in the process of making the VR system available to its customers and dealers.
Almost as glamorous as operator training is maintenance. We're all familiar with reactive maintenance and preventative maintenance. But now there's predictive maintenance that brings in sensors, big data, data analytics and some artificial intelligence. While new to the supply chain, predictive maintenance has been used for years in jet engines and elsewhere.
Quite simply, predictive maintenance is real-time maintenance. Equipment is maintained because it needs attention not because it broke or it's Tuesday the 25th of the month.
“It's a shift from reasonable expectations to reliable expectations,” says Lorne Weeter, Dematic's senior vice president of customer service. And that's the case whether it's a drive, motor, lift truck of integrated system.
The basis of predictive maintenance is collecting data (sensors) about the operating condition of individual components and pieces of equipment. That data dump (big data) is then analyzed (data analytics) to determine in real time if action is required. Over time, machine learning (artificial intelligence) can not only anticipate equipment condition but help determine who should be working on each maintenance work order based on skills and wages of technicians, optimizing all aspects of maintenance.
Benefits include maintaining equipment only when needed. Furthermore, it eliminates the need to shut down a department for scheduled preventative maintenance. Both trim maintenance costs and downtime.
Predictive maintenance also reduces overall operating costs, says Kevin Reader, Knapp's director of business development and marketing. His company has been working for three years with a German grocer. Today, seven of its distribution centers use predictive maintenance. The goal was to reduce operating costs by 3%, but Reader says that number has been far exceeded.
Several companies will be featuring predictive maintenance programs at Modex 2018.
Then there's the matter of robots in the DC. Autonomous mobile robots are starting to come into their own. In fact, Gartner's Dwight Klappich says this NextGen technology has the largest potential to change warehouse operations in the next five to ten years (see NextGen: The Interview).
Autonomous mobile robots are a first cousin of automatic guided vehicles, which have been in the workplace for more than 35 years. While the latter typically follows a pre-set guide path, autonomous mobile robots are capable of setting their own path to perform transportation tasks.
Navigation technology is at the heart of it all. The most common, known as natural environment or contour navigation, uses lasers to detect objects in the DC. That data is then processed by the Simultaneous Localization and Mapping (SLAM) system to build a facility map. This allows the robot to move about the facility freely.
Another technology here is LiDAR (Light Detection and Ranging) systems that build a two-dimensional view of the facility. As with contour navigation, LiDAR uses SLAM to process the data and build a map for the robot.
A third navigation system uses a stereo camera-based system to collect a 360-degree view of the facility. Every quarter second the system collects millions of data points from the cameras. A data-dense map is then created on-board to navigate the facility.
While relatively new, none of these navigation systems are without experience. Distribution center users include DHL, Walgreens and RK Logistics Group. Seegrid's camera-based navigation system has nearly 900,000 miles on warehouse and DC floors.
So there you have it. Virtual reality in lift truck operator training. Sensors, big data, data analytics and artificial intelligence in predictive maintenance. SLAM, LiDAR and stereo-cameras guiding autonomous mobile robots. All here now. All with experience in the warehouse and distribution center. All part of the NextGen Supply Chain today. Don't get caught napping.
Gary Forger is the special projects editor for Supply Chain Management Review. He can be reached at [email protected].
SC
MR

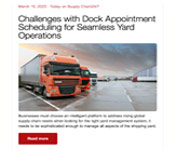
Latest Supply Chain News
Latest Podcast
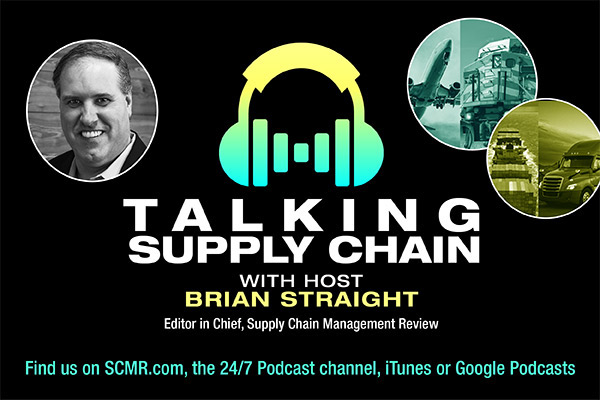
Explore
Software & Technology News
- Nine questions are the key to AI success in building resilient supply chains
- Looking back at NextGen 2024
- AI is moving omnichannel closer to the customer
- How technological innovation is paving the way for a carbon-free future in logistics and supply chains
- Körber Supply Chain Software’s Craig Moore says MercuryGate acquisition is about the customer
- Robotic use grows by 10%
- More Software & Technology
Latest Software & Technology Resources
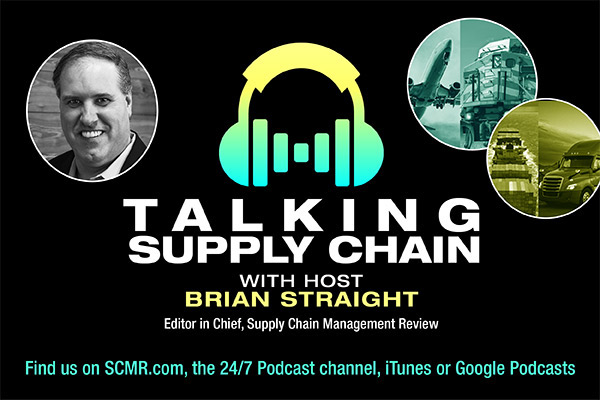
Subscribe
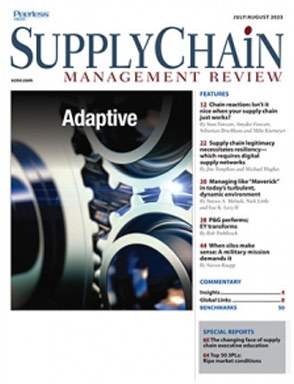
Supply Chain Management Review delivers the best industry content.
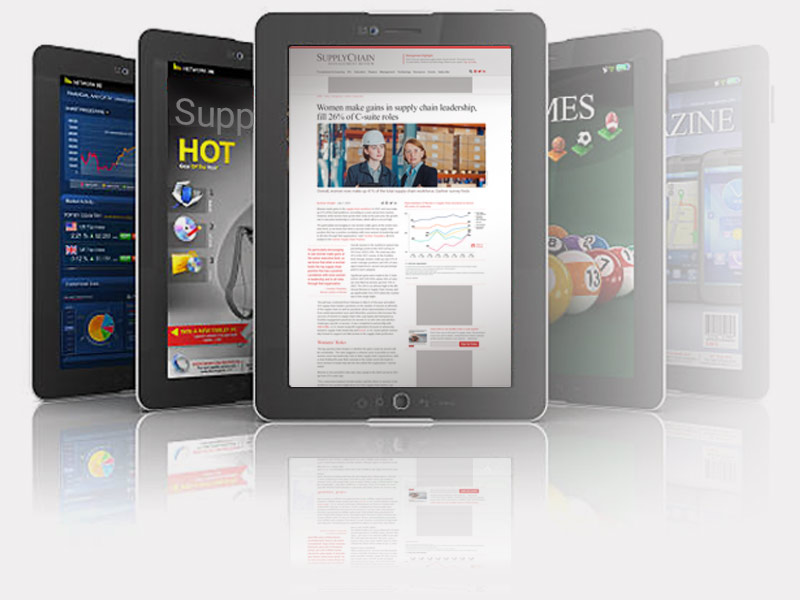
Editors’ Picks

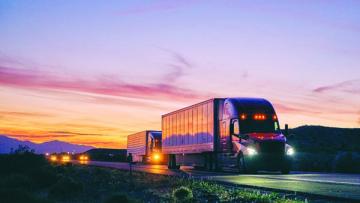

