Sorry, but your login has failed. Please recheck your login information and resubmit. If your subscription has expired, renew here.
January-February 2019
Truth be told, I was not a Boy Scout, or at least not a very good scout and not for very long. But I think there are some lessons for supply chain managers in the Scout motto: Be prepared. When I Wiki’d it this morning, I found the following: Be prepared, which means you are always in a state of readiness in mind and body to do your duty. Browse this issue archive.Need Help? Contact customer service 847-559-7581 More options
Every business can appreciate the value of keeping equipment maintained. But maintenance tasks can be tricky—especially in process manufacturing industries such as chemicals, oil and gas, agribusiness, or food manufacturing. For example, a chemical plant might have 4,000 pieces of equipment, some of which can’t be maintained, repaired, replaced or even inspected while the plant is running. Such plants require a turnaround—a complete cessation of all plant activities to perform necessary maintenance.
Because a turnaround involves lost production, an overrun in turnaround downtime can have severe consequences. At a sold-out plant, one where market demand exceeds demonstrated capacity, an inability to meet that demand can lead to millions of dollars in lost potential revenues. But companies sometimes feel powerless in the face of unplanned events, such as the discovery of unexpected damage to a piece of critical equipment. Is there any way to mitigate the risks associated with maintenance turnarounds?
Yes. Turnarounds can benefit from sound strategy and planning. In one recent project, a global chemical company reduced turnaround schedule slippage in a sold-out plant by 97% (100-plus days). It increased asset utilization by 5% and reduced turnaround costs by 10% to 20%. This article explains how.
This complete article is available to subscribers only.
Log in now for full access or start your PLUS+ subscription for instant access.
SC
MR
Sorry, but your login has failed. Please recheck your login information and resubmit. If your subscription has expired, renew here.
January-February 2019
Truth be told, I was not a Boy Scout, or at least not a very good scout and not for very long. But I think there are some lessons for supply chain managers in the Scout motto: Be prepared. When I Wiki’d it this… Browse this issue archive. Access your online digital edition. Download a PDF file of the January-February 2019 issue.Every business can appreciate the value of keeping equipment maintained. But maintenance tasks can be tricky—especially in process manufacturing industries such as chemicals, oil and gas, agribusiness, or food manufacturing. For example, a chemical plant might have 4,000 pieces of equipment, some of which can't be maintained, repaired, replaced or even inspected while the plant is running. Such plants require a turnaround—a complete cessation of all plant activities to perform necessary maintenance.
Because a turnaround involves lost production, an overrun in turnaround downtime can have severe consequences. At a sold-out plant, one where market demand exceeds demonstrated capacity, an inability to meet that demand can lead to millions of dollars in lost potential revenues. But companies sometimes feel powerless in the face of unplanned events, such as the discovery of unexpected damage to a piece of critical equipment. Is there any way to mitigate the risks associated with maintenance turnarounds?
Yes. Turnarounds can benefit from sound strategy and planning. In one recent project, a global chemical company reduced turnaround schedule slippage in a sold-out plant by 97% (100-plus days). It increased asset utilization by 5% and reduced turnaround costs by 10% to 20%. This article explains how.
SC
MR

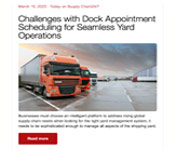
Latest Supply Chain News
- Tariffs, taxes and trade: The impact of Trump’s reelection on the supply chain
- How to improve demand forecasts for new product families
- Services sector sees growth in October, reports ISM
- Balanced supply chain management Part 4: The key—leading beyond the silo
- Managing inbound freight: What has changed in two decades?
- More News
Latest Podcast
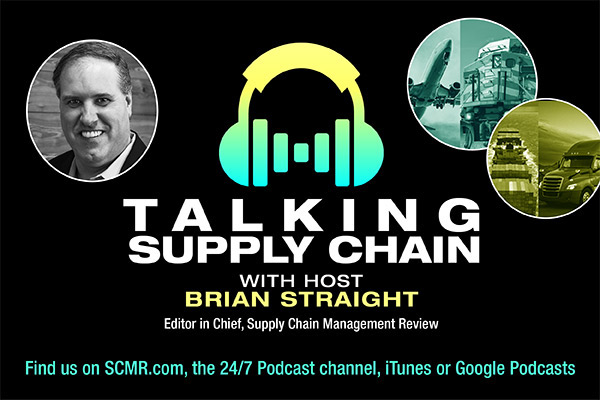
Explore
Procurement & Sourcing News
- Tariffs, taxes and trade: The impact of Trump’s reelection on the supply chain
- How to improve demand forecasts for new product families
- Aggregators sitting on the throne of Africa’s e-commerce supply chains: What lessons can we learn?
- Cross-border transport 2024: Navigating the surge
- Benchmarking the complexity of ESG reporting
- Looking back at NextGen 2024
- More Procurement & Sourcing
Latest Procurement & Sourcing Resources
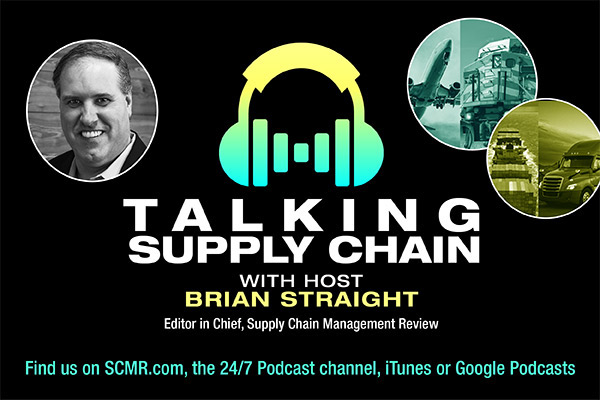
Subscribe
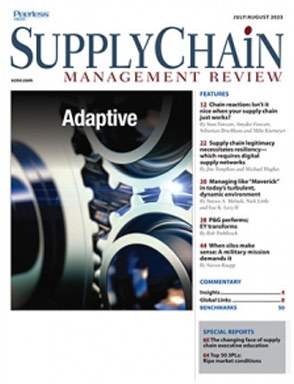
Supply Chain Management Review delivers the best industry content.
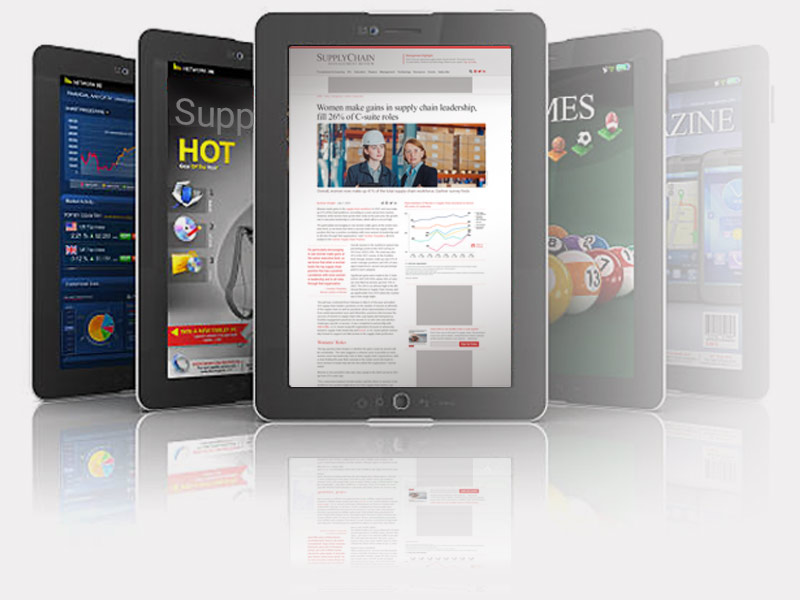
Editors’ Picks



