Sorry, but your login has failed. Please recheck your login information and resubmit. If your subscription has expired, renew here.
November 2014
Supply chain managers are on the lookout for metrics that will allow them to put a number to their progress - or lack thereof. Welcome to KPI's that allow them to demonstrate the quantifiable value that they deliver. At the same time, Murphy's Law may intervene or they may be called upon to put out fires or come to the rescue and make good on the promises sales and marketing have made to customers - regardless of the cost. So, how do you measure success? I hope this month's issue and online bonus feature help you consider how you measure your progress. Browse this issue archive.Need Help? Contact customer service 847-559-7581 More options
A pizza’s just a pizza, right? One pie is pretty much as good as the next? That kind of thinking does not exist at Papa John’s, the nation’s third largest pizza chain, according to the trade magazine Pizza Today. With nearly 4,500 locations around the world, including 3,200 stores in the U.S., and $3 billion in annual sales, the Louisville, Ky.-based company is constantly thinking about the next system or process that can help customers gets their pizza in a timely manner.
The company has experienced tremendous growth with locations in all 50 states and over 36 countries. No matter how big the company gets, Papa John’s is committed to its humble beginnings of using quality ingredients and quality people to build a better pizza and deliver a better pizza experience.
Papa John’s began in 2006 to transform its network of 10 dough manufacturing and distribution centers (called Quality Control Centers) through the use of better technology. The focus of this effort is to use point of sale demand information coupled with upcoming promotions to become more demand driven; done right, fresh ingredients replenish a network of 10 DCs in the right quantities for upcoming sales and are then delivered to its stores twice a week.
![]() |
This complete article is available to subscribers
only. Click on Log In Now at the top of this article for full access. Or, Start your PLUS+ subscription for instant access. |
SC
MR
Sorry, but your login has failed. Please recheck your login information and resubmit. If your subscription has expired, renew here.
November 2014
Supply chain managers are on the lookout for metrics that will allow them to put a number to their progress - or lack thereof. Welcome to KPI's that allow them to demonstrate the quantifiable value that they… Browse this issue archive. Access your online digital edition. Download a PDF file of the November 2014 issue.
![]() |
Download Article PDF |
A pizza’s just a pizza, right? One pie is pretty much as good as the next? That kind of thinking does not exist at Papa John’s, the nation’s third largest pizza chain, according to the trade magazine Pizza Today. With nearly 4,500 locations around the world, including 3,200 stores in the U.S., and $3 billion in annual sales, the Louisville, Ky.-based company is constantly thinking about the next system or process that can help customers gets their pizza in a timely manner.
The company has experienced tremendous growth with locations in all 50 states and over 36 countries. No matter how big the company gets, Papa John’s is committed to its humble beginnings of using quality ingredients and quality people to build a better pizza and deliver a better pizza experience.
Papa John’s began in 2006 to transform its network of 10 dough manufacturing and distribution centers (called Quality Control Centers) through the use of better technology. The focus of this effort is to use point of sale demand information coupled with upcoming promotions to become more demand driven; done right, fresh ingredients replenish a network of 10 DCs in the right quantities for upcoming sales and are then delivered to its stores twice a week.
![]() |
SUBSCRIBERS: Click here to download PDF of the full article. |
SC
MR
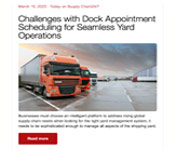
Latest Supply Chain News
- Made in Mexico, manufactured by China
- Retail sales see gains in October, reports Commerce and NRF
- Balancing green and speed: Home delivery insights from the pandemic era
- AdventHealth named top healthcare supply chain by Gartner
- Geopolitical readiness in supply chains: Strategic challenges for leaders
- More News
Latest Podcast
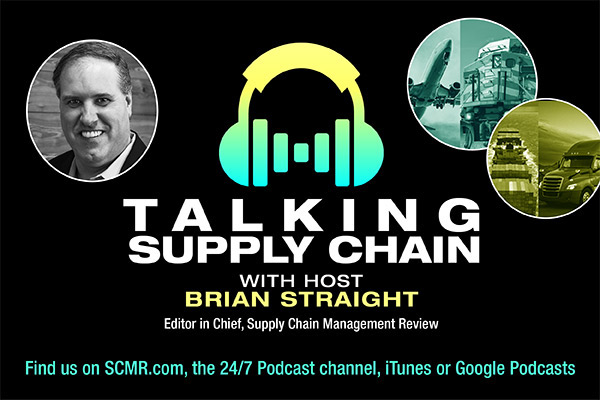
Explore
Latest Supply Chain News
- Made in Mexico, manufactured by China
- Retail sales see gains in October, reports Commerce and NRF
- Balancing green and speed: Home delivery insights from the pandemic era
- AdventHealth named top healthcare supply chain by Gartner
- Geopolitical readiness in supply chains: Strategic challenges for leaders
- Unlocking retention: The role employee engagement plays
- More latest news
Latest Resources
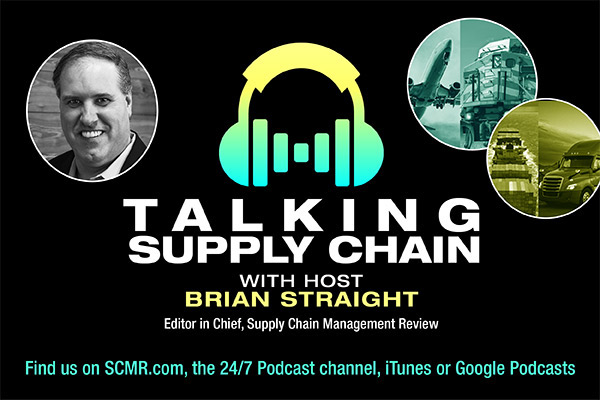
Subscribe
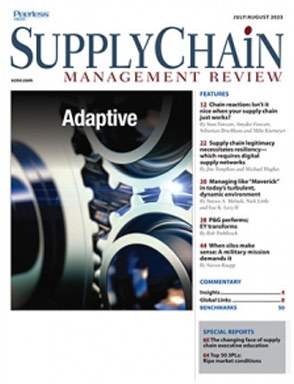
Supply Chain Management Review delivers the best industry content.
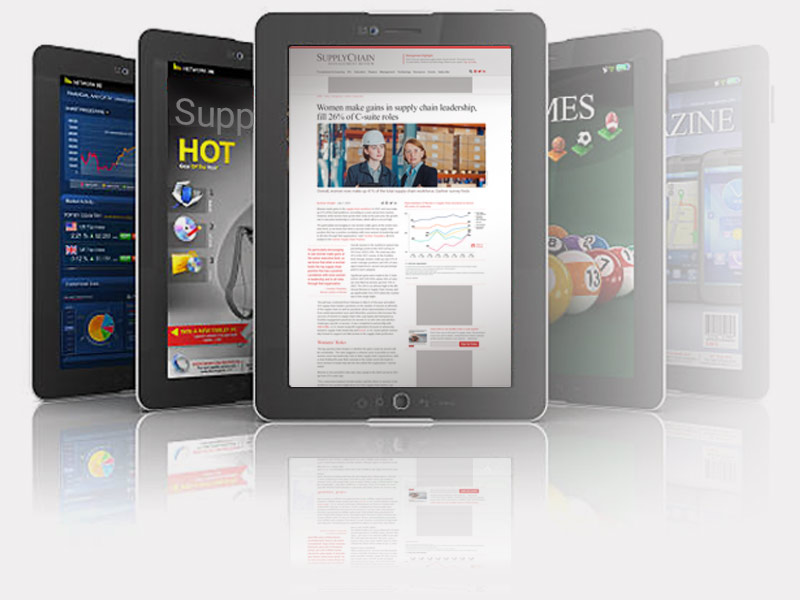
Editors’ Picks

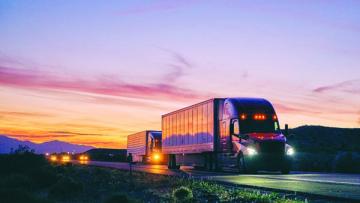

