Sorry, but your login has failed. Please recheck your login information and resubmit. If your subscription has expired, renew here.
May-June 2023
If you were dropped onto this planet and landed at McCormick Place in the heart of Chicago in the middle of March, you would probably conclude that planet Earth had been overrun by robots. Everywhere you turned on the ProMat conference floor, there was a robot lifting something, putting something away, or carrying something to another location. But, despite a conference hall overrun by technology, the on-the-ground reality is a bit different. Not so long ago, commercial real estate firm Prologis estimated the number of facilities with any type of automation at about 10%. But that is changing—quickly. A recent report from JLL found that one-in-two… Browse this issue archive.Need Help? Contact customer service 847-559-7581 More options
Managing spare parts inventory is a balancing act. In asset-heavy industries, uptime is essential to profitable operations. That’s true whether you’re operating a manufacturing line, mining equipment or an oil and gas drilling rig and refinery. Given the choice between too little and too much inventory, many organizations opt for lots of just-in-case parts and materials on the shelf. The view is that the investment in extra inventory is less than the cost of shutting down operations for the lack of a part.
There are other common complicating factors that are familiar to almost anyone responsible for MRO inventory. For one, buying authority is often decentralized across individuals or teams such as the engineering team, the team responsible for scheduling maintenance and new construction projects, or the procurement and/or inventory management team; one hand doesn’t always know what the other hand is buying. For another, overstocks may end up in the landfill if they exceed their expiration date or become obsolete as older equipment is phased out, overhauled or replaced. That’s not just costly, but it has an impact on
sustainability for organizations focusing on ESG.
Those were some of the conditions that confronted Petrobras in 2019. “At that time, we had two problems,” recalls Paulo Henrique Furtado, the inventory manager at the Brazilian energy company. “We had high inventory levels and high levels of surplus inventory. At the same time, we had low customer satisfaction levels because the people within our organization who used spare parts and materials couldn’t always get them when they needed them.
The combination of low customer satisfaction levels and high inventory levels caught the attention of the board of directors. That year, the board directed the supply chain team to seek a benchmark to measure, and then improve, Petrobras’ supply chain performance. In response, one of the world’s largest oil and gas companies launched a transformation project that even today continues to improve its customer service levels and create new inventory management practices that could impact the bottom line. To make that happen, the supply chain organization utilized the Association for Supply Chain Management’s Supply Chain Operations Reference model, or SCOR.
Among the results to date: A 25% reduction in the inventory days of supply from 2019 to 2021; a 40% reduction in active SKU codes; and the avoidance of nearly $800 million in unnecessary inventory purchases. In addition, Petrobras is using transformation to upskill the supply chain team by mapping requirements for each supply chain function, measure the skills gap of each employee, and then create an action plan with specific trainings to fill those gaps. A pilot program in the inventory management department delivered a 32% skills improvement among team members.
This complete article is available to subscribers only.
Log in now for full access or start your PLUS+ subscription for instant access.
SC
MR
Sorry, but your login has failed. Please recheck your login information and resubmit. If your subscription has expired, renew here.
May-June 2023
If you were dropped onto this planet and landed at McCormick Place in the heart of Chicago in the middle of March, you would probably conclude that planet Earth had been overrun by robots. Everywhere you turned on the… Browse this issue archive. Access your online digital edition. Download a PDF file of the May-June 2023 issue.Managing spare parts inventory is a balancing act. In asset-heavy industries, uptime is essential to profitable operations. That’s true whether you’re operating a manufacturing line, mining equipment or an oil and gas drilling rig and refinery. Given the choice between too little and too much inventory, many organizations opt for lots of just-in-case parts and materials on the shelf. The view is that the investment in extra inventory is less than the cost of shutting down operations for the lack of a part.
There are other common complicating factors that are familiar to almost anyone responsible for MRO inventory. For one, buying authority is often decentralized across individuals or teams such as the engineering team, the team responsible for scheduling maintenance and new construction projects, or the procurement and/or inventory management team; one hand doesn’t always know what the other hand is buying. For another, overstocks may end up in the landfill if they exceed their expiration date or become obsolete as older equipment is phased out, overhauled or replaced. That’s not just costly, but it has an impact on
sustainability for organizations focusing on ESG.
Those were some of the conditions that confronted Petrobras in 2019. “At that time, we had two problems,” recalls Paulo Henrique Furtado, the inventory manager at the Brazilian energy company. “We had high inventory levels and high levels of surplus inventory. At the same time, we had low customer satisfaction levels because the people within our organization who used spare parts and materials couldn’t always get them when they needed them.
The combination of low customer satisfaction levels and high inventory levels caught the attention of the board of directors. That year, the board directed the supply chain team to seek a benchmark to measure, and then improve, Petrobras’ supply chain performance. In response, one of the world’s largest oil and gas companies launched a transformation project that even today continues to improve its customer service levels and create new inventory management practices that could impact the bottom line. To make that happen, the supply chain organization utilized the Association for Supply Chain Management’s Supply Chain Operations Reference model, or SCOR.
Among the results to date: A 25% reduction in the inventory days of supply from 2019 to 2021; a 40% reduction in active SKU codes; and the avoidance of nearly $800 million in unnecessary inventory purchases. In addition, Petrobras is using transformation to upskill the supply chain team by mapping requirements for each supply chain function, measure the skills gap of each employee, and then create an action plan with specific trainings to fill those gaps. A pilot program in the inventory management department delivered a 32% skills improvement among team members.
SC
MR

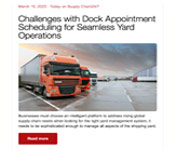
More Inventory Management
- Strengthening customer fulfillment: Building a strategic stakeholder network
- With capacity to spare, logistics real estate demand remains subdued
- How to improve demand forecasts for new product families
- Cross-border transport 2024: Navigating the surge
- Looking back at NextGen 2024
- How to make your CFO a supply chain superfan
- More Inventory Management
Latest Podcast
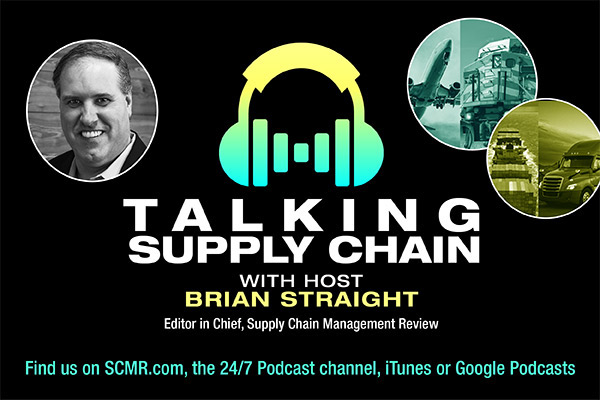
Explore
Topics
Procurement & Sourcing News
- Strengthening customer fulfillment: Building a strategic stakeholder network
- Trump picks former Wisconsin congressman Sean Duffy for DOT secretary
- Made in Mexico, manufactured by China
- Retail sales see gains in October, reports Commerce and NRF
- Geopolitical readiness in supply chains: Strategic challenges for leaders
- With capacity to spare, logistics real estate demand remains subdued
- More Procurement & Sourcing
Latest Procurement & Sourcing Resources
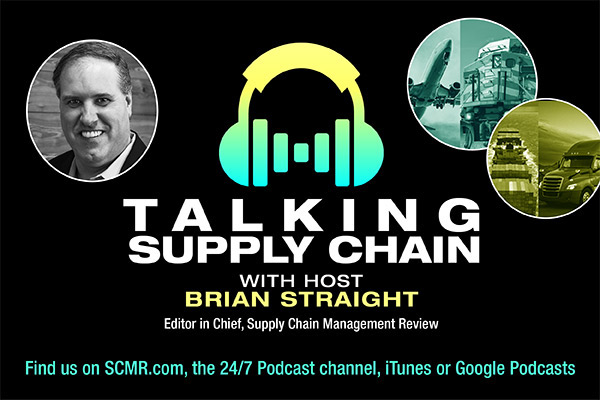
Subscribe
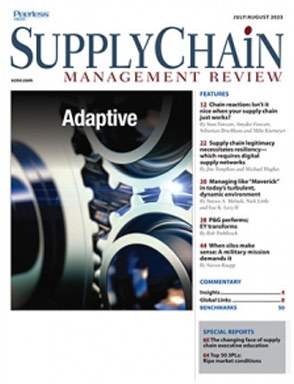
Supply Chain Management Review delivers the best industry content.
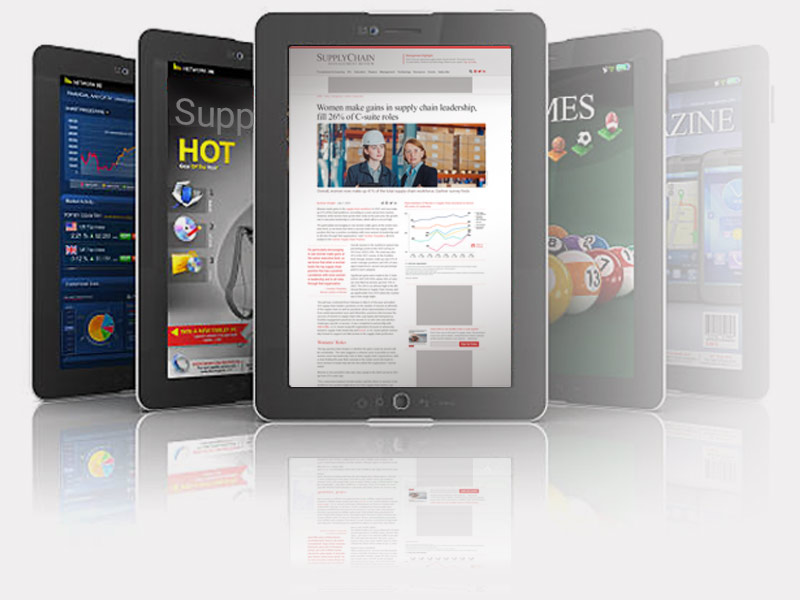
Editors’ Picks

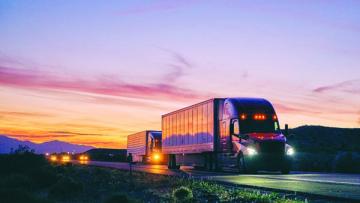

