Sorry, but your login has failed. Please recheck your login information and resubmit. If your subscription has expired, renew here.
September-October 2024
Back in late 2023, in response to global panic about the state of the supply chain, President Joe Biden announced the formation of the White House Council on Supply Chain Resilience. “We’re doubling down on our work at home—starting right here, right now—with the launch of a new Council on Supply Chain Resilience,” Biden said. That council won’t turn in its first official report until later this year, and while the myriad of crises that triggered the administration’s action has mostly subsided, the risks remain. Disruptions such as the recent Microsoft-Crowdstrike computer outage, a pending East Coast longshoreman’s port strike, and… Browse this issue archive.Need Help? Contact customer service 847-559-7581 More options
Efforts, especially in the United States, to reduce the reliance on foreign trade have gained steam over the past decade. The concept of shipping manufacturing jobs overseas in search of cheaper labor accelerated in the early 2000s, turning what was once a workforce employing over 14.5 million people in 2000 to a low of 11.5 million in 2010. From 2011 through 2023, data from the U.S. Bureau of Labor Statistics shows the country has recovered just over 1 million jobs, to 12.9 million by 2023.
Part of that is likely due to the push started under then-President Donald Trump to incentivize domestic manufacturing, and which has continued under the Biden administration. The CHIPS and Science Act, Infrastructure Investment and Jobs Act, Inflation Reduction Act, and the Build America, Buy America Act, as well as the introduction of tariffs in the 2018 to 2020 timeframe on imported goods from China to the U.S., have driven the desire to diversify supply chains and bring manufacturing closer to or even in to the U.S.
SC
MR
Sorry, but your login has failed. Please recheck your login information and resubmit. If your subscription has expired, renew here.
September-October 2024
Back in late 2023, in response to global panic about the state of the supply chain, President Joe Biden announced the formation of the White House Council on Supply Chain Resilience. “We’re doubling down on our… Browse this issue archive. Access your online digital edition. Download a PDF file of the September-October 2024 issue.Efforts, especially in the United States, to reduce the reliance on foreign trade have gained steam over the past decade. The concept of shipping manufacturing jobs overseas in search of cheaper labor accelerated in the early 2000s, turning what was once a workforce employing over 14.5 million people in 2000 to a low of 11.5 million in 2010. From 2011 through 2023, data from the U.S. Bureau of Labor Statistics shows the country has recovered just over 1 million jobs, to 12.9 million by 2023.
Part of that is likely due to the push started under then-President Donald Trump to incentivize domestic manufacturing, and which has continued under the Biden administration. The CHIPS and Science Act, Infrastructure Investment and Jobs Act, Inflation Reduction Act, and the Build America, Buy America Act, as well as the introduction of tariffs in the 2018 to 2020 timeframe on imported goods from China to the U.S., have driven the desire to diversify supply chains and bring manufacturing closer to or even in the U.S.
The other trigger was COVID-19’s global shutdown and the massive materials and product shortages that followed. Companies realized the fragility of supply chains that relied on just-in-time inventory. As countries reopened at varying paces, the search for materials became a hunt akin to finding Bigfoot.
The 2020-2022 timeframe accelerated the nearshoring trend that had already started in the early 2010s and picked up pace under Trump with passage of the United States Mexico Canada Agreement (USMCA).

“Once again, supply chain professionals will be called upon to be flexible and open to rethinking how supply chains operate today,” wrote Rosemary Coates, executive director of the Reshoring Institute, in a November 2022 article on scmr.com. “Shorter, less risky supply chains will drive faster order fulfillment and response times. Patterns and routes will shift in response to where products are being made, and that will lead to the renegotiation of carrier contracts, selection of new services, and new supply chain partners.”
What is reglobalization?
Nearshoring, reshoring, and friendshoring—despite the attention these terms are seeing in 2024—are still just nodes in the global supply chain. In fact, according to Vicky Forman, senior director analyst at Gartner, they are all part of what is being termed “reglobalization.”
“Supply chains are still global,” she said. “No company is just doing nearshoring.”
Forman says that most companies are employing multiple tactics to build resiliency and diversification of their supply chains. Hence, the term reglobalization. However, whereas supply chains used to shift based on where low-cost labor and materials resided, that is now just one of the factors global companies are considering when seeking out partners or deciding on facility locations. Add sustainability, resiliency, geopolitical concerns, and regulatory requirements to the mix and the concept of single-region sourcing presents too much risk in today’s global supply chain.
The World Trade Organization (WTO) 2023 World Trade Report noted that globalization of the supply chain created financial inequities around the world. But as companies have looked to build resiliency in supply chains, those inequalities are creating additional issues, from workforces driven by forced labor, to regions that are unable to invest in infrastructure to support manufacturing growth. The result is that while companies are looking to diversify supply chains and improve risk mitigation efforts, they may be heading into regions where they are simply trading one potential problem for another.
Consequently, the (once again) growing trend of reglobalization is starting to take hold.
“Globalization is still the keystone of international trade following the COVID-19 pandemic, although there seems to be a growing trend toward trade protectionism around the world,” wrote Miaojie Yu, president and chair of professor in economics, Liaoning University, China. “Two prevalent features of trade globalization are the coupling of global trade integration with production disintegration, that is the rising integration of world markets brought about the expansion of global value chains. There is no doubt that protectionism is increasing the cost of trade, but these two features have not collapsed despite crises.”
Companies run toward low-cost networks
Global supply chains are not a new phenomenon—global trade routes connected ancient Greeks with other civilizations. But modern global supply chains typically had one thing in common: low cost. And that meant China.
Coates, at the ISM World conference earlier this year, relayed a story about a trip to a manufacturing facility in China years earlier with a client. On the visit, Coates said she saw very little in terms of safety precautions despite workers cutting metal. Additionally, the employees were making $3.63 per hour compared to a similar job in the U.S. paying $26 per hour and a comparable one in Europe paying $32 per hour at the time.
“My client was very happy with the production here,” Coates said. “They were getting very high-quality goods and were about to award a very big contract to this company. Low cost, low labor costs, low factory costs—all these things and great high-quality parts. All these things contributed to the reasons why so many companies wanted to go to China.”
That low-cost component has started to shift, though, helping drive the push toward reglobalization. Tariffs imposed by the Trump administration are part of the reason, as was passage of the USMCA, which allowed certain goods to be imported to the United States tariff-free. That has driven Chinese investment in Mexican facilities and companies at record levels.
The other change occurring is wages. Whereas China was once a low-cost country, that is no longer true. The Reshoring Institute compiled a list of the average salaries for production workers/machine operators in 2022 among major countries. Not surprisingly, Germany, the United States and the United Kingdom ranked 1-2-3. However, when looking at the other end of the spectrum, China was nowhere to be found. India, Mexico, Vietnam, Malaysia, Thailand, and Brazil all offered lower average salaries than China did.
In 2020, the average manufacturing wage in China was $6.50 an hour compared to $4.82 an hour in Mexico. Add in the extra cost of tariffs on goods coming from China and it’s easy to see why more companies are investing in Mexico.
Where are supply chain networks going?
In addition to Mexico, supply chains are moving globally; hence the reglobalization that Gartner now sees.
A 2023 AlixPartners survey found that companies are targeting a 40% reduction in their exposure to China with the U.S. (plus 30%) and Mexico (plus 10%) expected to see the biggest gains. While the effort remains in the early stages, AlixPartners found that companies are making decisions based on make vs. buy strategies and investing in supplier development, logistics and distribution footprint changes, and global procurement cost modeling.
The trend is not just moving away from China, but also to more localized manufacturing. Accenture surveyed 1,230 senior executives in 14 countries (350 from the U.S.) and 11 industries in the first quarter of 2023 and found that 85% of companies plan to manufacture and sell most of their products in the same region in 2026. Today, that number is 43%. In the U.S., 91% of companies intend to accomplish this, up from 52% today.
In addition, sourcing regionally will almost double to 65% by 2026, up from 38% today. That number, at 50% currently in the U.S., is expected to grow to 82% by 2026. U.S. companies are investing an average of $65 million in reshoring and production facility relocation this year and expect that to accelerate to $188 million by 2026.
As companies look beyond China, where are they going?
A study by Boston Consulting Group (BCG) found that India may be the biggest winner, with exports to the U.S. increasing by $23 billion, a 44% increase from 2018 to 2022. The company said that 90% of North American manufacturers have relocated at least some production from China in the past five years with an equal number saying they plan similar moves in the next five years.
BCG identified India, Southeast Asia, and Mexico as the likely biggest winners from the ongoing reglobalization. Importantly, the BCG study found that executives are willing to sacrifice more than 2% of gross margins, on average, to improve supply chain resilience and avoid future disruptions.
“In our experience, a successful production footprint strategy can reduce manufacturing and supply chain costs by 20% to 50% while improving resiliency and sustainability,” Jonathan Van Wyck, an author of the BCG study, said.
Which region a company expands or moves into seems to be dependent on several factors, including talent availability and local incentives. Right now, Forman said life science companies are often looking toward Eastern Europe, with 31% of these types of companies adding capacity in that region compared to 12% across other industries. Consumer goods companies and retailers are flocking to Southeast Asia outside of China while high-tech companies are growing in North America, where 29% of companies have added capacity, and Western Europe, with 31% growth there.
“In both North America and Western Europe, there are government incentives to add manufacturing capacity targeted at the high-tech industry. These incentives are an important part of the location decision-making process,” the Gartner report noted.
Reasons for reglobalization
“Some of our key findings were that most companies have made changes to their supply chain network in the past two years as they have learned the hard way that an over-reliance on those low-cost networks of the past has left them fairly vulnerable to all of the uncertainty that they’re facing today. And that has driven them to start to prioritize resilience at a higher level than cost,” Forman said.
Forman noted the benefit of resilience as a key to the reglobalization effort. In fact, she said Gartner saw an 11% increase in resilience as a key factor in relocating facilities/partners in the 2024 survey compared to the 2022 version.
The survey found that 73% of companies have added or removed production locations in the past two years. Cost, though, is no longer the driving factor in these decisions. It’s still important, Forman noted, but resiliency is taking on increasing importance.
“The changes being made in the network continue to be driven by a variety of factors as operational and logistics costs are no longer the sole objective when adjusting supply chain networks. Companies have felt the pain of supply chain disruptions; they have learned to redefine network KPIs and are considering the hidden impacts associated with poor resilience, agility, and flexibility in addition to cost,” the Gartner report noted.
Resilience (46%), agility and flexibility (43%), and cost-efficiency (41%) are now the topthree considerations.
Forman added that labor remains a concern—both the cost of labor and access to labor. “It’s not just the availability of labor, it is the availability of the right labor for the processes that the company needs to compete, which varies very much from industry to industry,” she said.
Gartner asked companies to cite three factors as driving changes to their supply chain network over the past two years. In all, eight factors received a vote. In addition to the previous three mentioned, sustainability objectives (38%), streamlining networks (36%), positioning for future growth (35%), regulatory requirements (32%), and external geopolitical pressures (26%) were all mentioned.
“Companies continue to deploy already determined network strategies, often refining or reviewing actions based on the latest operating conditions. The biggest shift in recent years is in the importance of resilience as a factor behind the changes, with an 11% increase compared to 2022,”
the report noted.
Network design changes
So, what changes are occurring to networks? Gartner found several changes taking place, topped by 50% of respondents saying they have added new supply locations with existing supply partners. New partners were cited by 48% of respondents, while buffer inventories (43%) and the addition of owned factories (26%) also were highly mentioned. Few companies are reducing their footprints, although owned facilities (minus 11%) and contract manufacturing locations (minus 10%) are seeing the biggest change.
There are challenges, though.
“Any network change for any reason should look at the long-term pros and cons of that change and assess it against those company objectives,” Forman said. “And that could be shifts in regulations, it could be shifts in incentives or it could be shifting in cost that is driving that uncertainty. But that absolutely should be incorporated into the decision-making.”

In the Gartner survey, 96% of companies said they faced some challenge in new locations, with increasing operating and support costs (25%) and increased logistics costs (23%) cited most often. These challenges also varied by region. For instance, in India, inadequate logistics infrastructure is a major challenge, whereas access to labor is a challenge in North America. Cost, though, remains the primary concern regardless of location, just not the only one any longer.
Expectations being met
Regardless of the reason for a footprint change, the majority of companies doing so are meeting expectations. Only 7% of companies said they missed expectations and 3% said it was too early to say. Overall, though, companies are happy with their decisions. Among the benefits companies are seeing are improved service, cost reduction, improved agility, improved resilience, and reduced carbon emissions.
In all, 37% of companies said the network change exceeded expectations and 32% said it met expectations. Just over two in 10 said it “significantly exceeded expectation.”
“There’s always going to be multiple factors that are driving a decision about where to go, but it’s not all just about where you need to go,” Forman said. “It is also about the processes and the technology that supports a network change as well. [You] can’t just pick up a factory and hope it’s going to work without the right people and processes in place.”
For those companies that are not seeing the expected benefits, the most cited reason was the inability to manage the level of change required or a lack of local workforce, each cited by 43% of respondents.
Forman said that companies looking to continue diversification of their operations increase their risk by locating in only one location. “This is about not betting all of your changes on one single strategy or one single location,” she said. “Companies are taking strategies that look at adding different manufacturing in different locations, but they’re also evaluating their supply base and they’re also evaluating their distribution and how it is all going to work together. And there could be a near [or] reshoring strategy along with a low-cost diversification strategy for different products. It’s a case of not having a one-size-fits-all network and looking at changes and adjustments across the entire network and choosing the appropriate one for that appropriate segment.”
Interestingly, whether a company said it met or exceeded expectations played into what it expects in future change. For those companies that exceeded or significantly exceeded expectations, improving agility and flexibility (48%) was the top driver of change going forward. Companies that met expectations most often said reducing operational cost (50%) will be the top change driver. Whereas companies that missed expectations most often said they will focus on resiliency (53%).

Recent supply chain performance is also contributing to how objectives are shifting. For instance, companies that did not meet objectives in the past two years are shifting focus from sustainability and operational expenses to supporting growth and simplification. Those that met expectations are focusing on network simplification. Even those that exceeded expectations are shifting their objectives, albeit a little less significantly. These companies are more focused on agility and flexibility and meeting regulatory requirements.
“The highest-performing companies that have achieved the foundations of cost-efficiency and resilience over recent years now have the ability to drive changes that will further their competitive advantage,” Gartner wrote. “Whereas those that have not met primary objectives over recent years are further behind on their resilience and diversification strategies, so are still trying to catch up to the leaders.”
Reglobalization is back in vogue
Forman, who was involved in the 2022 survey for Gartner as well, said the results this year are not too surprising, but it was good to see companies seeing benefits of the changes.
“The nice surprise was the fact that all of the hard work on these changes has paid off for most companies and that they have met their expected benefits,” she said. “All of the data that we’ve got is that there is still change ongoing; that it is very much not a one-and-done when it comes to change. There will be another change that they’ve done in the next two years that will have either paid off or not paid off. But we do expect to continue to see companies continue to execute those changes rather than just plan them.”
Companies, according to Gartner’s research and Forman’s observations, must continue to change. Single-strategy networks will expose them to added risk. Whether it is geopolitical, cost/scarcity of labor, technology expertise, or climate, risk is everywhere in 2024. Nearshoring or reshoring is only one part of the equation, Forman noted. Reglobalization takes a more holistic approach and is now back in vogue in supply chain management.
SC
MR

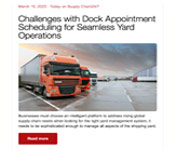
More Risk Mitigation
- Made in Mexico, manufactured by China
- Geopolitical readiness in supply chains: Strategic challenges for leaders
- Mitigating geopolitical uncertainty: 4 essential tactics for industrial CSCOs
- How technological innovation is paving the way for a carbon-free future in logistics and supply chains
- Regulations are forcing organizations to address software supply chain security
- More Risk Mitigation
What's Related in Risk Mitigation
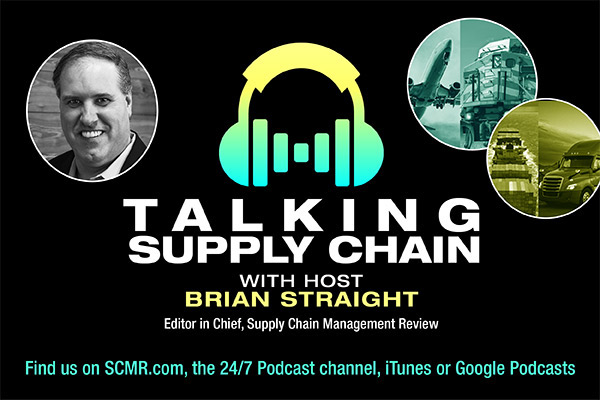
Explore
Topics
Procurement & Sourcing News
- Strengthening customer fulfillment: Building a strategic stakeholder network
- Trump picks former Wisconsin congressman Sean Duffy for DOT secretary
- Made in Mexico, manufactured by China
- Retail sales see gains in October, reports Commerce and NRF
- Geopolitical readiness in supply chains: Strategic challenges for leaders
- With capacity to spare, logistics real estate demand remains subdued
- More Procurement & Sourcing
Latest Procurement & Sourcing Resources
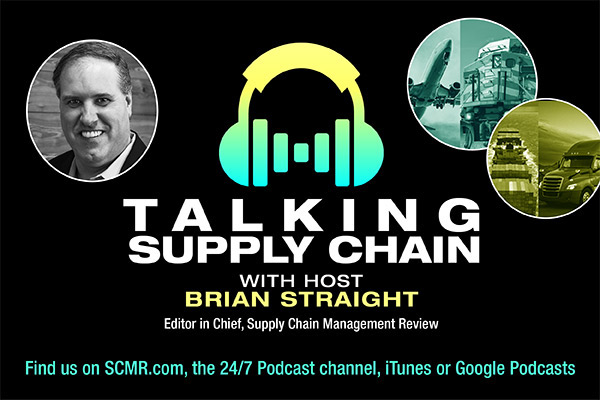
Subscribe
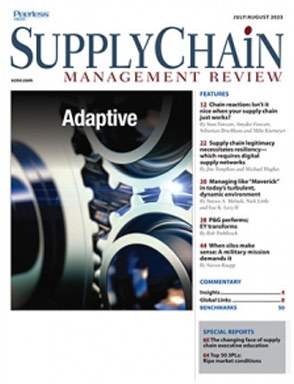
Supply Chain Management Review delivers the best industry content.
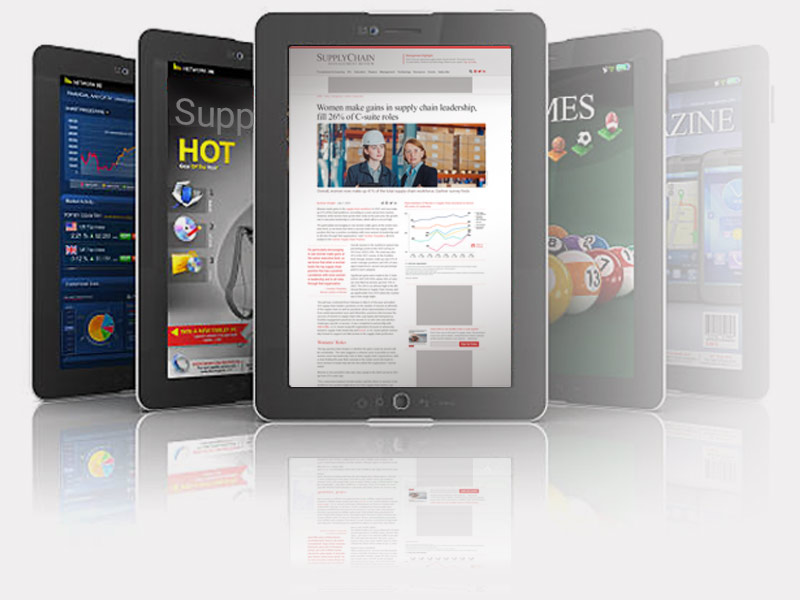
Editors’ Picks

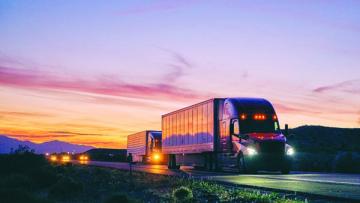

