Sorry, but your login has failed. Please recheck your login information and resubmit. If your subscription has expired, renew here.
March-April 2010
Business today is unrelenting. Just as you’ve finished up a dynamite promotion campaign or launched a superefficient distribution center, the market has a tendency of saying, “Not bad, but what have you done for me lately?” That’s cold! It’s exactly because of that competitive reality that companies today need to constantly fine tune and update every aspect of their performance. Naturally, we’re particularly concerned about that part of the business called supply chain management. Browse this issue archive.Need Help? Contact customer service 847-559-7581 More options
There has been plenty of discussion over the years about how to reduce inventory. Generally, the perspective is from the office of the material planning manager or supply chain manager, since inventory performance is usually thought of as a production metric.
However, there are many aspects of inventory management that are directly influenced by decisions made in the procurement department. Many of the variables that are tied to the reliability of the logistics network are directly related to the locations of the suppliers and to their deliver performance. In addition, contractual agreements that specify high minimum-order quantities or long lead times—or both—can prevent the materials organization from making the necessary adjustments to raw material inputs when demand does not merit high volumes.
It may seem obvious to say that procurement managers must understand the impact of their decisions and strive to accommodate the goals of each operating unit in sourcing arrangements that are effective for all partiers. The decisions made within the procurement department have lasting effects on the rest of the organization; they become part of legally binding contracts that govern the way a company conducts business with its supply base. Unfortunately, it is still common practice to optimize the effectiveness of one function, such as procurement, at the expense of the effectiveness of others.
This article presents six checklist actions to help procurement professionals play more integrated roles in the management of inventory. Managed well, these actions can help improve profitability. Collectively, they can have as great a financial impact on an organization as does a reduction in purchased cost.
![]() |
This complete article is available to subscribers
only. Click on Log In Now at the top of this article for full access. Or, Start your PLUS+ subscription for instant access. |
SC
MR
Sorry, but your login has failed. Please recheck your login information and resubmit. If your subscription has expired, renew here.
March-April 2010
Business today is unrelenting. Just as you’ve finished up a dynamite promotion campaign or launched a superefficient distribution center, the market has a tendency of saying, “Not bad, but what have you done for… Browse this issue archive. Download a PDF file of the March-April 2010 issue.
![]() |
Download Article PDF |
There has been plenty of discussion over the years about how to reduce inventory. Generally, the perspective is from the office of the material planning manager or supply chain manager, since inventory performance is usually thought of as a production metric.
However, there are many aspects of inventory management that are directly influenced by decisions made in the procurement department. Many of the variables that are tied to the reliability of the logistics network are directly related to the locations of the suppliers and to their deliver performance. In addition, contractual agreements that specify high minimum-order quantities or long lead times—or both—can prevent the materials organization from making the necessary adjustments to raw material inputs when demand does not merit high volumes.
It may seem obvious to say that procurement managers must understand the impact of their decisions and strive to accommodate the goals of each operating unit in sourcing arrangements that are effective for all partiers. The decisions made within the procurement department have lasting effects on the rest of the organization; they become part of legally binding contracts that govern the way a company conducts business with its supply base. Unfortunately, it is still common practice to optimize the effectiveness of one function, such as procurement, at the expense of the effectiveness of others.
This article presents six checklist actions to help procurement professionals play more integrated roles in the management of inventory. Managed well, these actions can help improve profitability. Collectively, they can have as great a financial impact on an organization as does a reduction in purchased cost.
![]() |
SUBSCRIBERS: Click here to download PDF of the full article. |
SC
MR
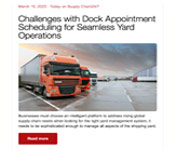
Latest Supply Chain News
- Made in Mexico, manufactured by China
- Retail sales see gains in October, reports Commerce and NRF
- Balancing green and speed: Home delivery insights from the pandemic era
- AdventHealth named top healthcare supply chain by Gartner
- Geopolitical readiness in supply chains: Strategic challenges for leaders
- More News
Latest Podcast
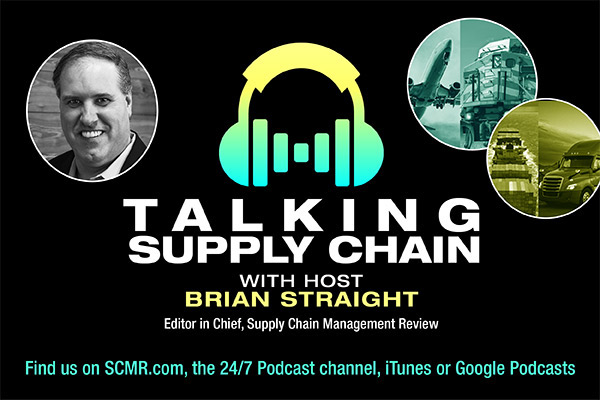
Explore
Topics
Procurement & Sourcing News
- Made in Mexico, manufactured by China
- Retail sales see gains in October, reports Commerce and NRF
- Geopolitical readiness in supply chains: Strategic challenges for leaders
- With capacity to spare, logistics real estate demand remains subdued
- Tariffs, taxes and trade: The impact of Trump’s reelection on the supply chain
- How to improve demand forecasts for new product families
- More Procurement & Sourcing
Latest Procurement & Sourcing Resources
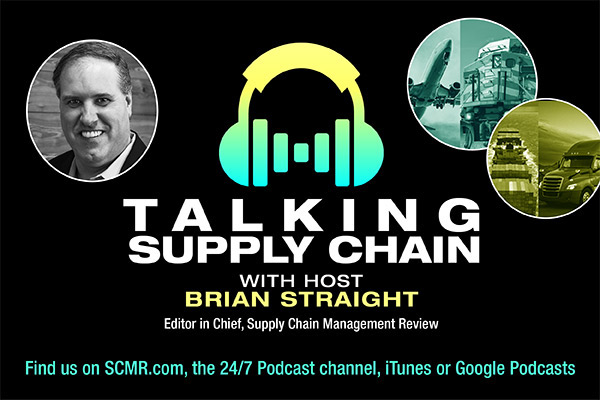
Subscribe
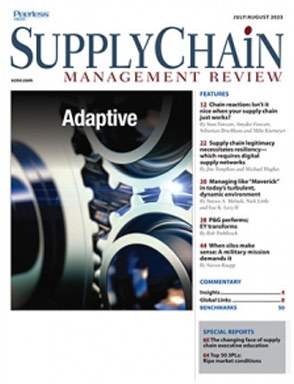
Supply Chain Management Review delivers the best industry content.
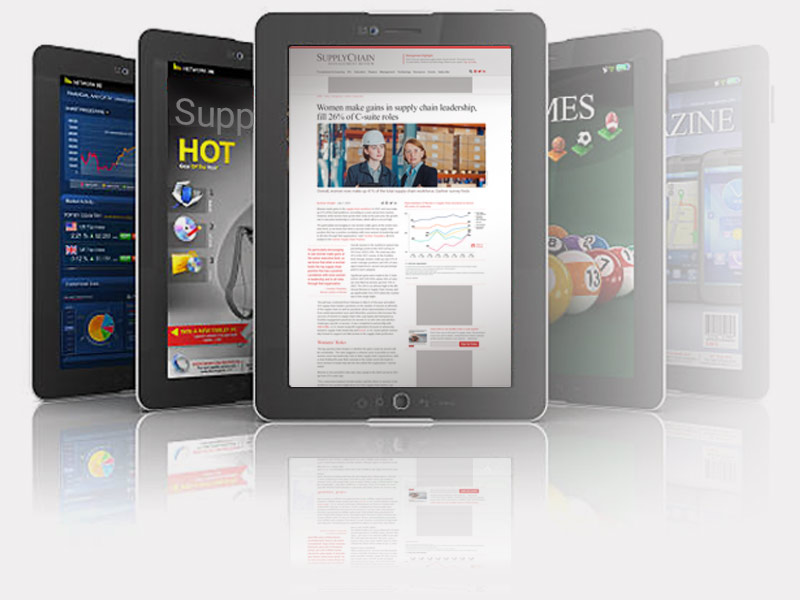
Editors’ Picks

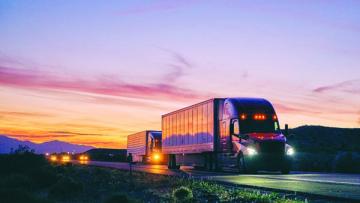

