When will the supply chain world return to “normal?” This is by far the number one question in my inbox these days as supply chain issues continue to make frontpage headlines, factories close down because of supply disruptions and President Biden personally gets involved in supply chain. Talk about supply chain making it out from the small grungy back-offices and onto the front stage with projector lights shining.
With that type of spotlight, it is unfortunate that supply chain leaders have few answers to create immediate relief. There simply are no easy answers and no fast solutions.
Demand fluctuations too big and uncertain: The fluctuations in demand are causing shifts that – using one of the most common phrases of the pandemic – are unprecedented. They are also pretty unpredictable. Unprecedented plus unpredictable makes it unattractive for investors. It is hard to assess what is a fluke, a fad or a trend. Why would anybody make investments in factories and equipment when the demand is so flighty?
Manufacturing plants require years to plan and make operational. In most countries, permitting and construction of manufacturing plants can take years, and often close to a decade. But even in a more agile regulatory and construction environment, the lead time on equipment delivery and installation is often measured in years. When chips are in short supply, there is no easy fix, even if investors are willing to fund the $3 billion to $10 billion of a new wafer manufacturing facility.
Construction of infrastructure is a decade long project. US supply chain pros have warned for years that our infrastructure is too fragile. Operational professionals know that when the volume is increasing over a trend line, it is a bad sign when you max out on capacity during busy times. That’s exactly what happened in prior years when US ports were unable to handle holiday imports. With some optimism and lots of funding, we can get the port restrictions solved by 2031. In the meantime, we are using air at high cost and environmental impact. Most other infrastructure improvement have similar timelines.
Problems may compound. Supply chain professionals are almost by definition great multitaskers. But when supply chain challenges compound, it is easy to feel like a tightrope walker who is also holding a human pyramid while juggling. That’s how it feels when the pandemic intersects with severe weather-related disruptions that intersects with a port crisis that intersects with a component manufacturing shortage that intersects with increased regulations and so forth. Even relatively small additional disruptions, such as a fire in a Japanese chip plant or a ship stuck in the Suez Canal, that hardly would have been noticed by the world community under normal circumstances, brings additional imbalance. The back-up to the back-up may just not be an option.
Yet, of course there are steps we can take in the short and mid-term, such as a strong and resilient procurement strategy, including collaborative strategies with tier 1 and 2 suppliers; simplifying supply chains by removing complexity, increasing buffer inventory and locating inventory close to anticipated markets; and developing visibility and ability to react fast to supply chain events. None of this is easy as demand shifts make earlier procurement commitments dubious as well as predictions about inventory requirements per market. Individually, companies can get still themselves into a stronger position. ALOM set out to be a preferred customer, collaborating with our suppliers over several decades. This is one of several reasons that our inventory arrives and we can support on-time shipping for our customers.
As supply chain is surfacing in politics, U.S. exporters could be helped by improved labor relations in the ports and increasing port outbound capacity and loading, preventing vessels from leaving empty while export goods are left behind. It is frankly also a no-brainer to run ports 24/7, just like the rest of the supply chain. Smart technology for ports or other chokepoint would prevent some of the stop-and-go issues. Truckers could get regulatory relief and support for the independent owner-operators. Near-shoring and shortened supply chains can be supported by consistent and fair regulations and fast processing times.
Yet, even if we work together, the cracks in the supply chain veneer will get bigger as the stress on the supply chains continues. We have allowed complexity to grow, and the pandemic and other supply chain disruptions simply exposed structural problems that were predictable. If we are really, really smart, we may be in better shape in ten years. In the meantime, the company with the most expertise, the most collaboration and the best data management has a considerable advantage.
Hannah Kain is the president and CEO of ALOM, a global supply chain management services and solutions provider serving as a partner to its Fortune 100 clients. Click here to learn more about the firm.
Click here to read more from the author.
SC
MR

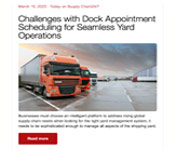
Latest Supply Chain News
Latest Podcast
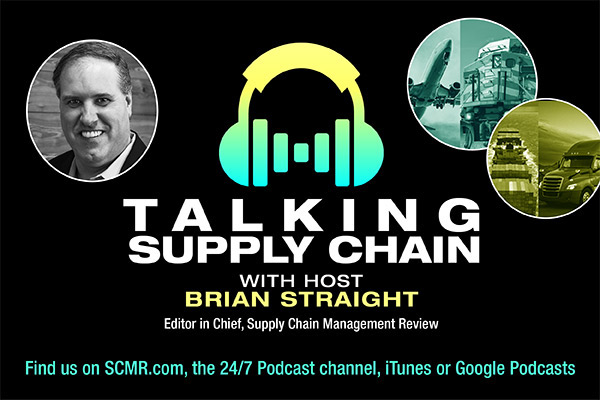
Explore
Latest Supply Chain News
- Challenges to ESG reporting
- With capacity to spare, logistics real estate demand remains subdued
- Tariffs, taxes and trade: The impact of Trump’s reelection on the supply chain
- How to improve demand forecasts for new product families
- Services sector sees growth in October, reports ISM
- Balanced supply chain management Part 4: The key—leading beyond the silo
- More latest news
Latest Resources
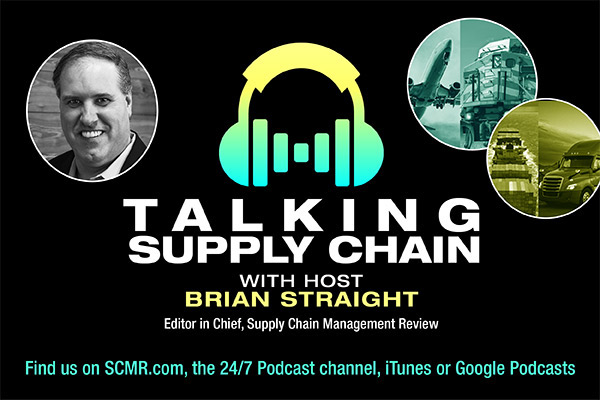
Subscribe
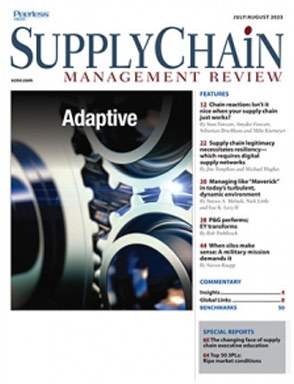
Supply Chain Management Review delivers the best industry content.
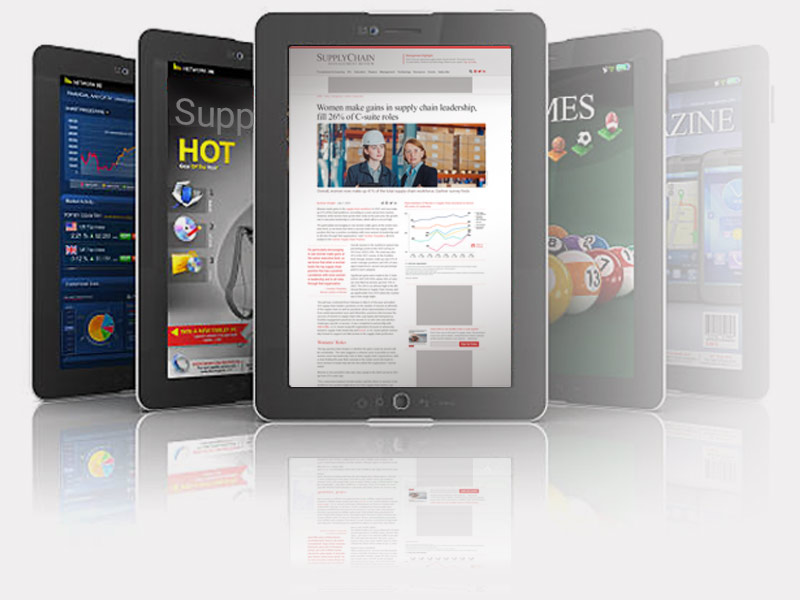
Editors’ Picks

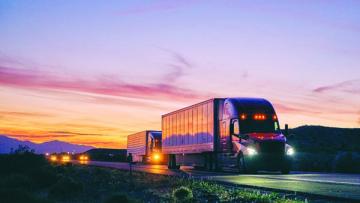

