Sorry, but your login has failed. Please recheck your login information and resubmit. If your subscription has expired, renew here.
September-October 2024
Back in late 2023, in response to global panic about the state of the supply chain, President Joe Biden announced the formation of the White House Council on Supply Chain Resilience. “We’re doubling down on our work at home—starting right here, right now—with the launch of a new Council on Supply Chain Resilience,” Biden said. That council won’t turn in its first official report until later this year, and while the myriad of crises that triggered the administration’s action has mostly subsided, the risks remain. Disruptions such as the recent Microsoft-Crowdstrike computer outage, a pending East Coast longshoreman’s port strike, and… Browse this issue archive.Need Help? Contact customer service 847-559-7581 More options
During and since the global pandemic, businesses and their respective supply chain management teams have acquired considerable process and decision-making data and learning. Simultaneous impacts in product demand levels coupled with corresponding global transportation and logistics disruptions are among them. This learning continues in the manifestation of terrorist attacks involving shipping vessels in the Red Sea area along with other industry-focused disruptions.
Supply chain leaders, if they have not done so already, should be aiming and aligning processes, skill levels, and supporting technology strategies that can better synchronize supply chain planning, internal and external collaboration, and customer fulfillment execution. Such efforts should include a decision-making context spanning an end-to-end supply chain network ecosystem as opposed to a singular functional process of planning or customer fulfillment execution. The process needs to be manifested by synchronization of data, information, and decision-making that factors internal inside-out, external outside-in, cross-business, and supply chain functional dimensions.
SC
MR
Sorry, but your login has failed. Please recheck your login information and resubmit. If your subscription has expired, renew here.
September-October 2024
Back in late 2023, in response to global panic about the state of the supply chain, President Joe Biden announced the formation of the White House Council on Supply Chain Resilience. “We’re doubling down on our… Browse this issue archive. Access your online digital edition. Download a PDF file of the September-October 2024 issue.During and since the global pandemic, businesses and their respective supply chain management teams have acquired considerable process and decision-making data and learning. Simultaneous impacts in product demand levels coupled with corresponding global transportation and logistics disruptions are among them. This learning continues in the manifestation of terrorist attacks involving shipping vessels in the Red Sea area along with other industry-focused disruptions.
Supply chain leaders, if they have not done so already, should be aiming and aligning processes, skill levels, and supporting technology strategies that can better synchronize supply chain planning, internal and external collaboration, and customer fulfillment execution. Such efforts should include a decision-making context spanning an end-to-end supply chain network ecosystem as opposed to a singular functional process of planning or customer fulfillment execution. The process needs to be manifested by synchronization of data, information, and decision-making that factors internal inside-out, external outside-in, cross-business, and supply chain functional dimensions.
Today’s more advanced software, data management, and cognitive analytics-based decision-making technologies can play a more enabling role in end-to-end ecosystem process synchronization and decision-making. However, vision coupled with consideration toward incremental scope utilizing control-layer approaches are likely to provide more meaningful progress.
Leveraging a new awareness of supply chain’s strategic importance
As we navigate further into the “Decade of Disruption,” global and domestic supply chain disruptions have both positively and negatively impacted business bottom-line outcomes. One positive outcome is that C-Suite executives have been compelled to actively sponsor and support supply chain transformational efforts.
“Smart companies are defining the future vision that provides the navigation required to automate the competitive roadmap for best practices and market-leading results.”
Efforts directed at added supply network agility, end-to-end ecosystem supply chain operational or tactical resiliency, coupled with better synchronization of operational and tactical decision-making are apparent. However, the challenge is moving beyond various functional lenses in line-of-business or supply chain.
Identify core objectives
We submit that establishing a broader vision and objectives should consider what end-to-end synchronization and often ecosystem-wide joint B2B business process and decision-making need to include.
Consider when planning and execution “worlds collide” the decision-making needs that differentiate at the moment operational decisions along with tactical and risk mitigation considerations are required. Decisions should be predicated on cognitive analytics based on data and information that have both internal and external sources, and with specific context. Supporting data should factor in structured transactional or operational execution data sources as well as unstructured sources such as in edge physical systems; for example, IoT-enabled operational management systems that may be on the factory floor, transport vehicles, logistics facilities, etc.
The data produced is more operational and detailed and often has to be aggregated and analyzed for trending actions/outcomes (intended and unintended consequences). In the latter category, consider, for example, early-warning risk data related to customer responses to a product introduction, a potential product shortcoming, or a major supplier’s business challenges. Information related to external ecosystem risk events related to weather patterns, global health, natural disasters, or escalating geopolitical events also need to be considered.
Further, consider a growing recognition across various industry settings that efforts addressing more accurate, harmonized, and active data management have always been a core challenge in achieving meaningful supply chain planning and execution synchronization of decision-making processes. Efforts must therefore be preceded by sound and continuous data management and data intelligence capabilities in collaboration with IT support or systems integration services teams.
Examples from functional collisions
As an example, consider that the planning of various components and materials needed to produce a product for customers based on a committed delivery date does not end at the supplier’s or contract manufacturer’s shipping dock. At the point of end-product manufacturing, another required component may have been delayed, impacting the particular factory’s daily production scheduling. The context to a prioritized or changed customer delivery date need is a process-wide consideration.
“Competing against or with time and disruptions are the norm as ecosystem resource collaboration technologies emerge from pervasive computing and next-generation edge applications.”
Certain products may need to be routed to supplemental product assembly or warehousing facilities, to retail online customer fulfillment centers, or shipped directly to the end-customer location. We have all become accustomed to receiving timely notifications from online retail providers as to when to expect shipment delivery, or the ability to track where that shipment currently resides in a specific carrier’s network. Behind the scenes, multiple cloud-based systems are being accessed, and most likely within the overall logistics flow process, important contextual information is missing as to other origins, product operational status, or a likely pending delay because of known disruption.
Consider the synchronization-focused capabilities that COVID-19 vaccine producers Pfizer and Moderna were able to establish across their vaccine production to last-mile delivery logistics distribution processes. There were requirements for constant refrigeration and temperature monitoring, and in the case of Pfizer, somewhat extreme cold temperatures to avoid spoilage. Partnering with specialty logistics and transportation services providers on processes related to specialized vaccine packaging included real-time alerting to temperature and shipment location. Healthcare services and governmental agencies were provided with real-time status on-demand, and shipments could be re-routed if necessary to other vaccine needing regions.
In essence, barriers were reduced because needs and expectations involved an expectation for the need for synchronization of planning and execution processes.
Roadmaps to advanced AI-based decision-making
Many businesses and respective supply chain management teams are seeking to evaluate the likely impact of termed Advanced AI capabilities whether related to chatbot-based GenAI-based or large language-based (LLM) learning models. The synchronizing of supply chain planning and execution process control points and decisions is an area where these technologies can provide benefits.
However, just like a house or a building requires a solid foundation, the benefits of more advanced supply chain decision-making similarly require a solid footing. Data management strategy must therefore be a business and executive-level topic of discussion and understanding. Teams should have an understanding of the differences between traditional or termed Narrow AI and Advanced AI support capabilities. The former AI and machine learning capabilities have already been successfully deployed among supply chain planning and/or execution software applications.
Advanced AI technology is far more sophisticated and predicated on acquired learning and developed insights. If you aren’t collecting the historical data to support Advanced AI algorithms, you may be at a competitive disadvantage. Only time can provide the accurate historical data required for machine learning. That will include subsequent learning of end-to-end ecosystem planning and execution process workflows. The technology further has a reliance on a cohesive and harmonized underlying data management model that likely transcends individual software applications and system platforms.
Consider cloud-based control layer platform approaches
There remains a realization among C-level executives, including supply chain and IT leaders, that costly, “big-bang rip-and-replace” technology implementations occurring in today’s more fast-paced and continually changing industry environments require a more flexible and less costly systems strategy and implementation approach. This includes supply chain transformational efforts.
In our research arm’s advisories and our ongoing Supply Chain Matters market education commentaries, we seek to bring an ongoing awareness to today’s available forms of what we term as supply chain “control layer” focused technology platforms.
A common tenet emerging from the research is that a cloud-based platform is specifically aimed at supporting end-to-end ecosystem decision-making of a particular process. These platforms are positioned to extract, control, and provide status among various existing installed ERP backbone, supply chain planning, procurement, customer fulfillment, manufacturing planning/scheduling, or other existing supply chain processes, data, and information sources. The architecture is such that the control layer extracts essential information and context to be able to serve as a de facto control layer for an end-to-end process. They serve as the data fabric, a digital twin, or a control tower-like manifestation of an end-to-end ecosystem resource planning (ERP4) process.
The benefits of a control layer approach are further manifested in achieving more timely time-to-value, in the ability to support subsequent multiple phases of required planning and execution synchronization timetables, and in mitigating the overall cost of customized data integration.
Ecosystem vision requirements
As the planning and execution “worlds” collide or rather converge, and are enabled by ecosystem visibility, new edge data sources, and increased advanced cognitive analytics, competitive advantage will be gained from resilience, adaptability, and flexibility. Competing against or with time and disruptions are the norm as ecosystem resource collaboration technologies emerge from pervasive computing and next-generation edge applications. Smart companies are defining the future vision that provides the navigation required to automate the competitive roadmap for best practices and market-leading results. •
About the author
Bob Ferrari is the managing director of the Ferrari Consulting and Research Group. He can be reached at [email protected].
About Global Links
Global Links appears in each issue of Supply Chain Management Review. Richard J. Sherman, retired guru of SCM, is the Global Links column editor. If you are interested in participating in the column, he can be reached at [email protected].
SC
MR

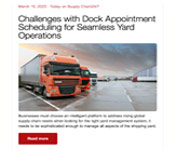
More Supply Chain Planning
- GenAI’s role in advancing supply chain planning
- When worlds collide
- Keynotes from Procter & Gamble, Johnson & Johnson & Whirlpool execs highlight NextGen conference agenda
- One door closes, a better one opens
- Colgate-Palmolive utilizes decision intelligence to accelerate complex decision-making
- More Supply Chain Planning
What's Related in Supply Chain Planning

Explore
Topics
Procurement & Sourcing News
- Retail sales see gains in October, reports Commerce and NRF
- Geopolitical readiness in supply chains: Strategic challenges for leaders
- With capacity to spare, logistics real estate demand remains subdued
- Tariffs, taxes and trade: The impact of Trump’s reelection on the supply chain
- How to improve demand forecasts for new product families
- Aggregators sitting on the throne of Africa’s e-commerce supply chains: What lessons can we learn?
- More Procurement & Sourcing
Latest Procurement & Sourcing Resources
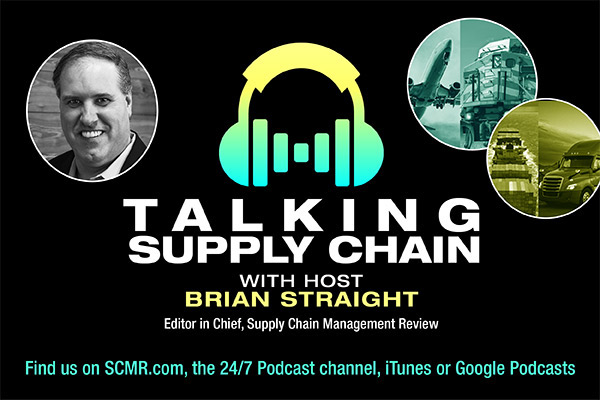
Subscribe
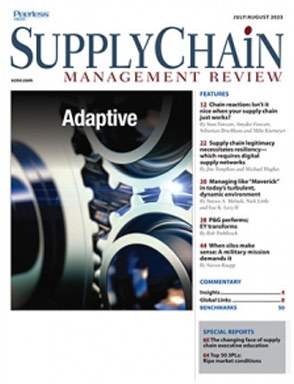
Supply Chain Management Review delivers the best industry content.
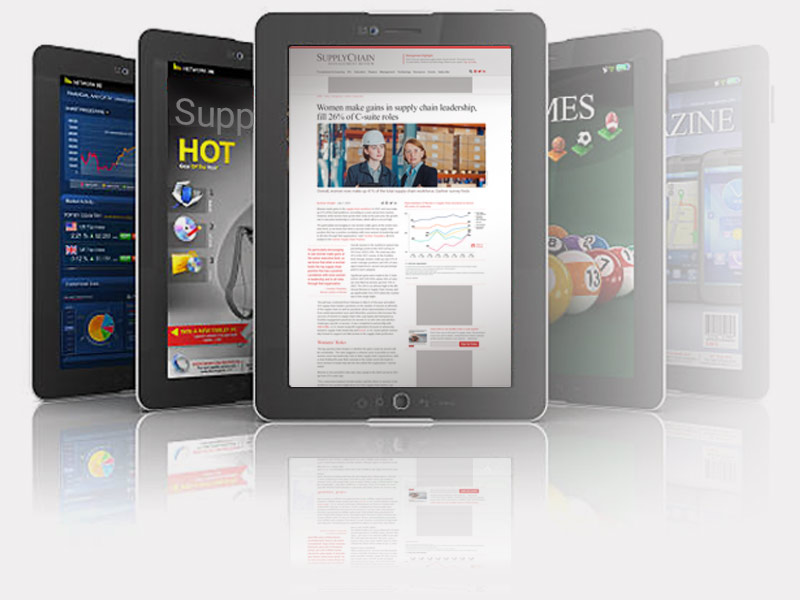
Editors’ Picks

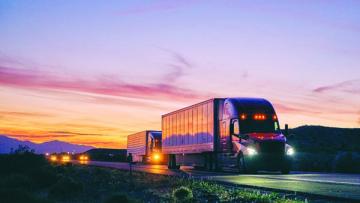

