The COVID-19 pandemic has wreaked havoc on global supply networks, forcing companies all over the world to deal with a slew of issues that threaten the supply chain’s continued operation, or, in some cases, survival. Changes in public policy in response to the COVID-19 pandemic, trade tensions between China and the United States and other factors are driving a decoupling trend. To thrive, businesses will need to devise novel strategies. Companies can use a great decoupling strategy to create an integrated, holistic approach to supply chains, gain a competitive advantage in this evolving world—globalized, yet decoupled—and rapidly transform and control their supply chains on their terms.
By lowering costs and increasing profits, a well-managed supply chain provides a competitive advantage. In contrast, poorly managed supply chains can lead to inefficiencies, compliance issues and consumer dissatisfaction. Companies that have well-defined legal and regulatory frameworks around their supply chain management programs benefit from more frequent commercial opportunities, easier access to higher-quality resources and people, and consistent quality and efficiency advantages.
The dreadful experience of seeing regular people like us turn on one another and lose our feelings of charity while clamoring to stuff items into our shopping carts is the part of a store run that sticks with us the longest. Scenes of frenzied purchases of toilet paper, hand sanitizers, masks, bottled water, and life-saving drugs in the early days of the pandemic will live on for a long time, probably forever, in our cultural memory. It’s even worse when it comes to necessities like food and medicine.
In my opinion, these photographs embody everything that has gone wrong with supply chains over the last four decades. After the Coronavirus first came on our shores, our supply lines were disrupted for more than two years. In the last three months, container ships unloading cargo in American ports have taken longer than they did before the start of the pandemic. Several well-known firms, including Apple, GE, and Mondelez, have warned that their supply chains would be constrained.
According to a recent PwC survey, more than one-third of America’s C-level executives anticipate that supply chain disruptions will continue. Food scarcity is still making headlines around the world, including in the United States. The shortage of semiconductors remains an issue.
Two years is a long time for any intelligent system to learn from its mistakes and correct its path. This appears not to be the case with our supply chains. Naturally, there are many unanswered questions. What exactly is the issue with our supply chains? What was it about the pandemic that caught our supply chain managers off guard? What, more importantly, can be done to remedy the situation?
The criticism that supply chains have become far too lean is valid. A simple solution is to make them less lean by stocking our warehouses. After all, by definition, a disaster defies our best predictions and preparations. As a result, in this blog, we must evaluate this claim.
Keep in mind that no amount of resilience can prevent panic buying, which can result in a low loop and a supply outage. The ongoing disruption of supply systems after the initial shock has left the supply chain struggling to get back on its feet is a greater source of concern.
There are other issues at stake in addition to the ‘too lean’ issue. In my opinion, the elephant in the room is the single-strand supply chain that serves us in the United States, with demand centers concentrated at one end and supply centers concentrated at the other. To get a sense of how serious this problem is, let’s take a quick look at the chip shortage problem and how it has impacted the automotive industry.
A global chip shortage halted car production in three states in February of last year. According to Reuters, the governors of Michigan, Indiana, Ohio, Kentucky, Kansas, South Carolina, Alabama, and Missouri urged President Biden to expand production of chips and “temporarily reallocate a modest portion of their current production to auto-grade wafer production.”
The world was then in the grip of a chip famine, which has since subsided, but not before costing the automotive industry an estimated $210 billion in lost revenue by 2021, according to consultants Alix Partners.
The semiconductor shortage can be traced back to the peak of the first pandemic wave in July 2020, when carmakers in the United States and elsewhere reduced their semiconductor procurement, alarmed by lockdown restrictions.
This prompted chip manufacturers, the vast majority of whom are based outside the United States, to redirect their production lines to the electronics industry, which is experiencing a surge in demand because of the pandemic-induced trend of remote working.
The fundamental nature of COVID-19’s disruptions to global supply chains, combined with rising China-US trade tensions, has resulted in a new normal—in which instability is the norm rather than the exception. Many countries are focusing on national policies to ensure that domestic firms can conduct business with major trading partners who are implementing decoupling or other adjustment measures. Without a doubt, this will have a significant impact on global supply chains.
Decoupled supply chains will be far more resilient to geopolitical tensions and natural disasters and will not expose humanity to the despair and despondency caused by the current crisis. Above all, they will be more beneficial to the environment and climate. That, in and of itself, is an admirable goal.
Nick Vyas is an educator, global thought leader, author, keynote speaker, American Society for Quality Fellow (ASQ), Chair of the ASQ Lean Division, and legal advisor to leaders in the worlds of supply-chain and global trade practice and policy. As the founding Executive Director of USC Marshall’s Kendrick Global Supply Chain Institute and Academic Director of the M.S. Global Supply Chain program, Dr. Vyas educates the next generation of business leaders. He can be reached at linkedin.com/in/thevyasusc
SC
MR

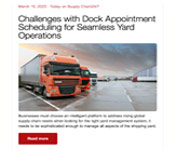
Latest Supply Chain News
Latest Podcast
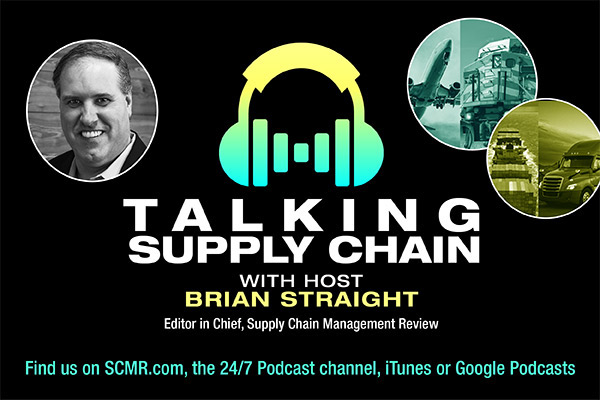
Explore
Latest Supply Chain News
- Strengthening customer fulfillment: Building a strategic stakeholder network
- The hard job of teaching soft skills
- Trump picks former Wisconsin congressman Sean Duffy for DOT secretary
- Made in Mexico, manufactured by China
- Retail sales see gains in October, reports Commerce and NRF
- Balancing green and speed: Home delivery insights from the pandemic era
- More latest news
Latest Resources
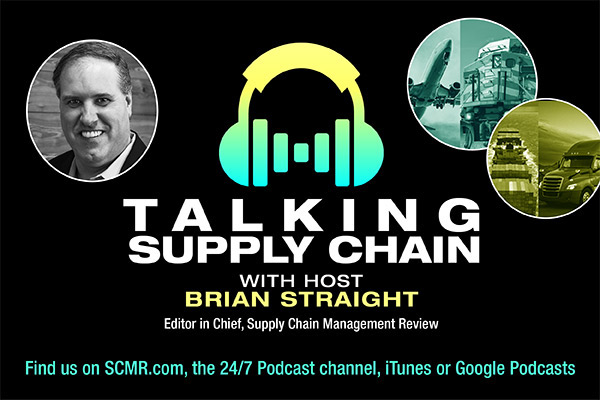
Subscribe
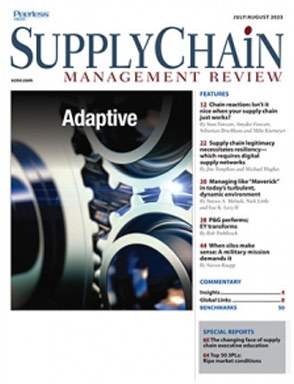
Supply Chain Management Review delivers the best industry content.
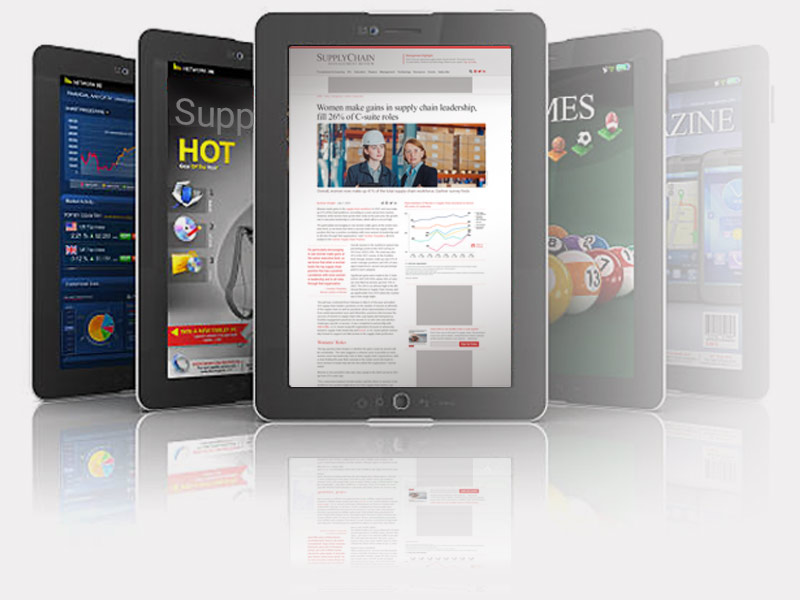
Editors’ Picks

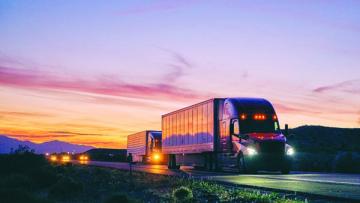

