U.S. companies made only marginal improvements in their ability to collect from customers and pay suppliers in 2013, while showing no improvement in how well they managed inventory, according to the 16th annual working capital survey from REL a division of the Hackett Group, Inc.
“For inventory, the global marketplace has made issues like demand planning more important than ever before,” says Analisa DeHaro, Associate Principal for REL, a division of The Hackett Group. “Companies need to factor in lead times that may not have been an issue when manufacturing was done closer to home. The best companies are becoming more savvy about this, and are more effectively balancing the various elements of inventory management.”
The amount tied up in excess working capital at nearly 1000 of the largest public companies in the U.S. is over a trillion dollars, according to the REL research.
With the U.S. economy slow but stable, gross domestic product increased by 3.2 percent in 2013. But at the same time, the REL/CFO research found that gross margins decreased by 0.3 percent, indicating that companies are spending more internally to generate revenue.
The research also found that companies are continuing to borrow, using low interest rates to improve their cash position, with cash on hand increasing by 12 percent, or $110 billion. At the same time companies continued to ramp up capital expenditures, which have risen by 43 percent over the past three years.
The value of total net working capital rose by 3.2 percent in 2013, and days working capital improved by less than 1 percent. While days sales outstanding and days payable outstanding improved only slightly, Days inventory on hand showed no change at all.
“We’re clearly not seeing a big push on improving inventory performance right now,” says Craig Bailey, director of The Hackett Group. “That’s being driven by a few things. With low interest rates, it doesn’t cost as much to hold inventory, so service and availability become the drivers. In some industries, there’s also an expectation of an upturn in the market, which is leading companies to stockpile inventory.”
According to Bailey, some offshoring trends are also working against inventory improvements.
“As the cost of manufacturing in China continues to increase, companies are moving West within China, or relocating to Vietnam or other countries to find markets where infrastructure and labor costs are lower,” he says. “To facilitate moves like these, companies will commonly build inventory, to allow production to ramp up, and as a fallback in case of startup issues, which are common.”
SC
MR
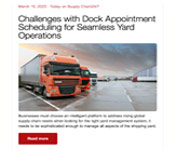
More Finance
- Services sector sees growth in October, reports ISM
- Looking back at NextGen 2024
- Manufacturing again contracts in October, reports ISM
- NextGen Supply Chain Conference set for October 21-23
- Estée Lauder, Schneider Electric and S&S Activewear to receive NextGen End User awards
- 2024 Robotics Application Conference announces session, speaker lineup
- More Finance
Latest Podcast
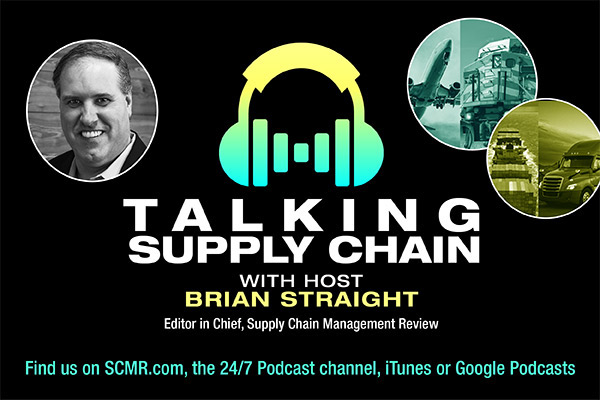
Explore
Business Management News
- Retail sales see gains in October, reports Commerce and NRF
- Balancing green and speed: Home delivery insights from the pandemic era
- AdventHealth named top healthcare supply chain by Gartner
- Unlocking retention: The role employee engagement plays
- Can supply chain managers embrace an entrepreneurial mindset?
- Challenges to ESG reporting
- More Business Management
Latest Business Management Resources
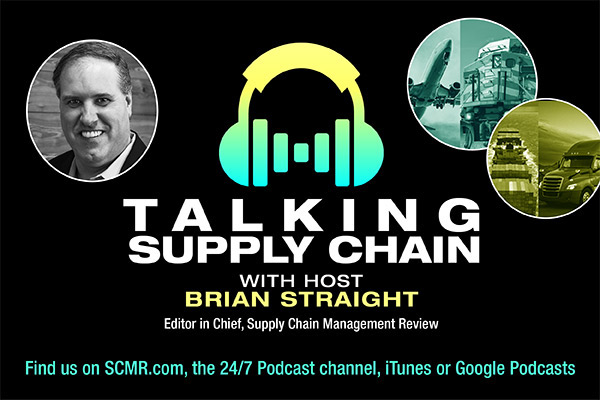
Subscribe
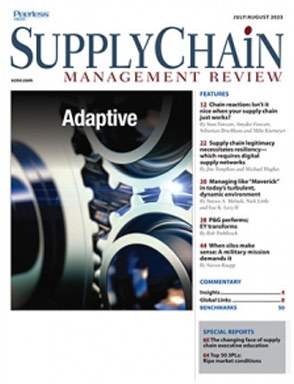
Supply Chain Management Review delivers the best industry content.
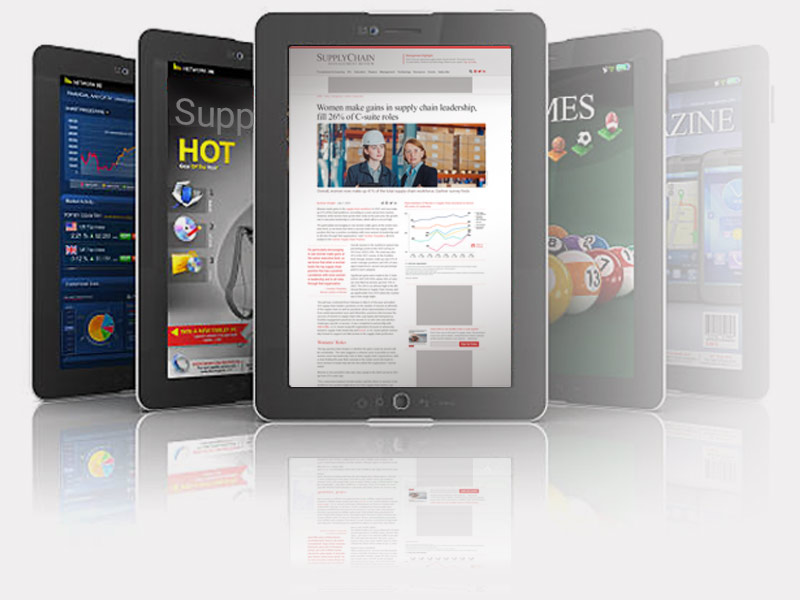
Editors’ Picks

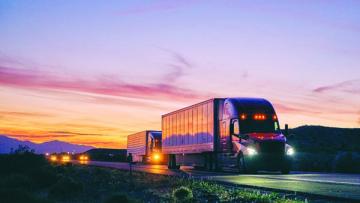

