Sorry, but your login has failed. Please recheck your login information and resubmit. If your subscription has expired, renew here.
March-April 2022
Yesterday, I hosted a webinar on the steps supply chain leaders are taking to redesign their supply chains to cope with this period of unprecedented demand. Earlier last month, I attended the Manifest conference in Las Vegas. The exhibitors featured a lineup of supply chain startups while the attendee list was dominated by venture capital firms looking to get in on the action in our booming industry. This morning, one of the lead news stories is about another disruption threatening to bring global supply chains to a halt: Browse this issue archive.Need Help? Contact customer service 847-559-7581 More options
In March of 2011, an earthquake struck central Japan. One of the affected companies was a supplier named Riken Corporation, surely an unfamiliar name to most. Within days, however, 70% of Japan’s auto production was affected because Riken couldn’t supply a $1.50 piston ring. Producers that relied on pistons like Toyota, Honda, Nissan and Mazda—really any company that made a product with an engine—had no buffer inventory or backup suppliers, something that ensured the disruption would be felt quickly and severely. Toyota temporarily shut down production at all of its Japanese assembly plants.
Several years later, a plant in Germany that makes almost all of the world’s Nylon-12 suffered a catastrophic explosion. Nylon-12 is a critical resin for producing fuel lines and other automotive brake components. The explosion that ripped through the facility destroyed about half of its production capacity. Within hours automotive OEMs across the globe had established crisis management teams to search for new supply sources and material substitutes.
These disruptions predated the pandemic by nearly a decade.
Welcome to the world of supply chain disruptions. Like the bumper sticker, we all know that “stuff happens.” And, as these examples illustrate, disruptions are often newsworthy events. At other times they are more local and subtle, such as when a supplier chooses to no longer serve a customer or a truck fails to make a delivery. Whatever the scope or scale of a disruption, when they occur reaction time is critical. The need to determine as quickly as possible a company’s vulnerability, risk exposure and courses of action become paramount. This article presents a set of questions that must be examined whenever an organization experiences a supply chain disruption that could affect operations.
This complete article is available to subscribers only.
Log in now for full access or start your PLUS+ subscription for instant access.
SC
MR
Sorry, but your login has failed. Please recheck your login information and resubmit. If your subscription has expired, renew here.
March-April 2022
Yesterday, I hosted a webinar on the steps supply chain leaders are taking to redesign their supply chains to cope with this period of unprecedented demand. Earlier last month, I attended the Manifest conference in… Browse this issue archive. Access your online digital edition. Download a PDF file of the March-April 2022 issue.In March of 2011, an earthquake struck central Japan. One of the affected companies was a supplier named Riken Corporation, surely an unfamiliar name to most. Within days, however, 70% of Japan’s auto production was affected because Riken couldn’t supply a $1.50 piston ring. Producers that relied on pistons like Toyota, Honda, Nissan and Mazda—really any company that made a product with an engine—had no buffer inventory or backup suppliers, something that ensured the disruption would be felt quickly and severely. Toyota temporarily shut down production at all of its Japanese assembly plants.
Several years later, a plant in Germany that makes almost all of the world’s Nylon-12 suffered a catastrophic explosion. Nylon-12 is a critical resin for producing fuel lines and other automotive brake components. The explosion that ripped through the facility destroyed about half of its production capacity. Within hours automotive OEMs across the globe had established crisis management teams to search for new supply sources and material substitutes.
These disruptions predated the pandemic by nearly a decade.
Welcome to the world of supply chain disruptions. Like the bumper sticker, we all know that “stuff happens.” And, as these examples illustrate, disruptions are often newsworthy events. At other times they are more local and subtle, such as when a supplier chooses to no longer serve a customer or a truck fails to make a delivery. Whatever the scope or scale of a disruption, when they occur reaction time is critical. The need to determine as quickly as possible a company’s vulnerability, risk exposure and courses of action become paramount. This article presents a set of questions that must be examined whenever an organization experiences a supply chain disruption that could affect operations.
SUBSCRIBERS: Click here to download PDF of the full article.
SC
MR

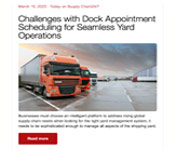
More Risk Management
- Geopolitical readiness in supply chains: Strategic challenges for leaders
- Tariffs, taxes and trade: The impact of Trump’s reelection on the supply chain
- Cross-border transport 2024: Navigating the surge
- Benchmarking the complexity of ESG reporting
- Looking back at NextGen 2024
- The Corporate Sustainability Due Diligence Directive
- More Risk Management
Latest Podcast
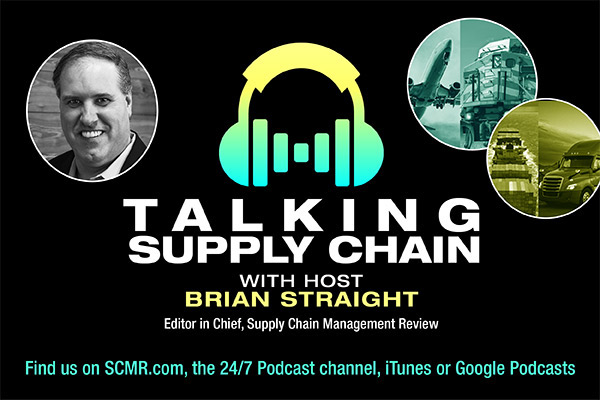
Explore
Topics
Procurement & Sourcing News
- Retail sales see gains in October, reports Commerce and NRF
- Geopolitical readiness in supply chains: Strategic challenges for leaders
- With capacity to spare, logistics real estate demand remains subdued
- Tariffs, taxes and trade: The impact of Trump’s reelection on the supply chain
- How to improve demand forecasts for new product families
- Aggregators sitting on the throne of Africa’s e-commerce supply chains: What lessons can we learn?
- More Procurement & Sourcing
Latest Procurement & Sourcing Resources
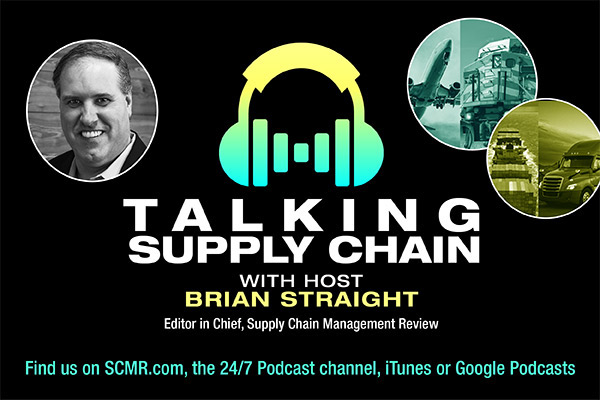
Subscribe
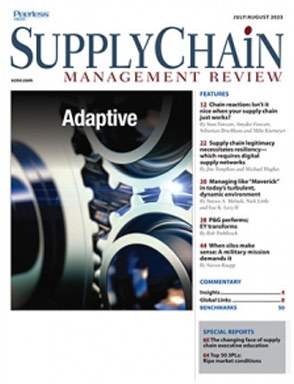
Supply Chain Management Review delivers the best industry content.
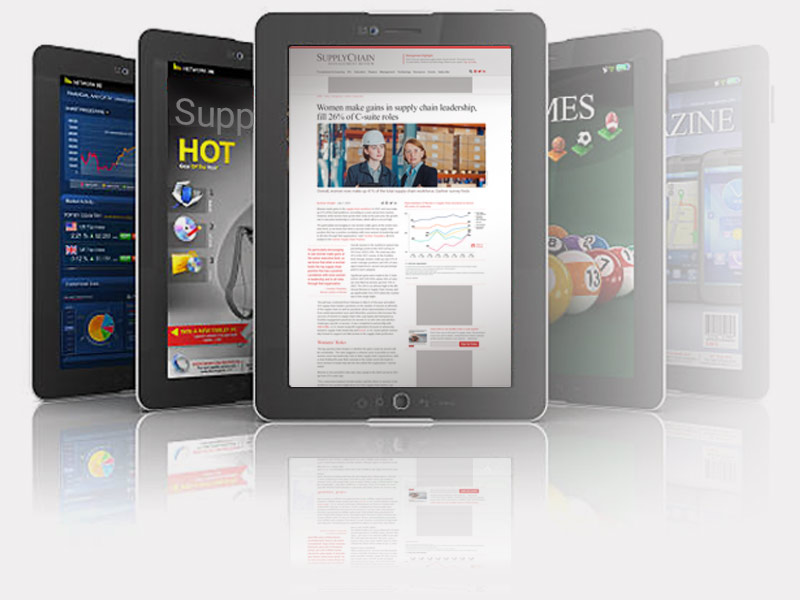
Editors’ Picks

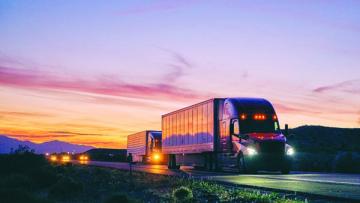

